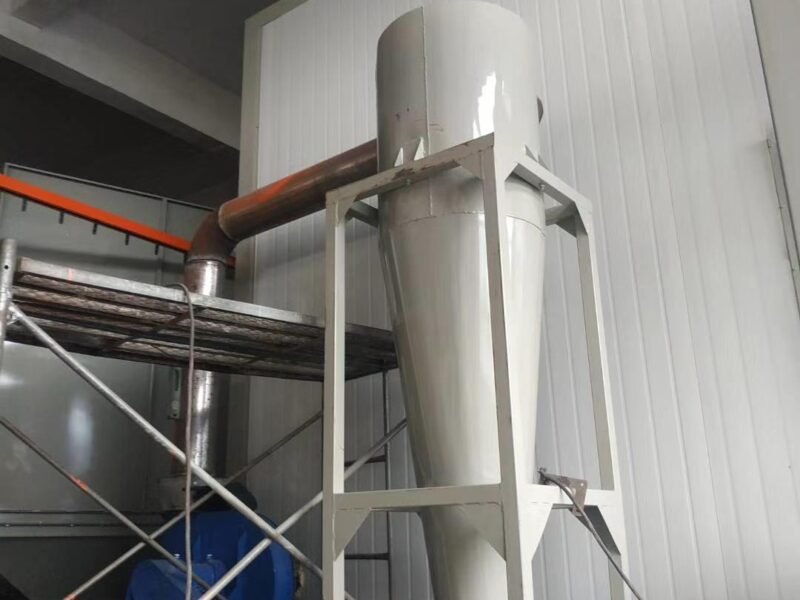
Understanding Electrostatic Spraying and Powder Coating
In the world of surface finishing, two techniques stand out for their efficiency, durability, and widespread application: electrostatic spraying and powder coating. These methods have revolutionized the way industries approach painting and coating, providing superior finishes with reduced waste and environmental impact. This article delves into the principles, processes, benefits, and applications of these two techniques.
### What is Electrostatic Spraying?
**Electrostatic spraying** is a method of applying paint or coating to a surface using charged particles. The technique relies on the principle that opposite charges attract, ensuring that the coating material adheres evenly to the target surface.
#### How It Works
1. **Charging the Particles:** In electrostatic spraying, the paint particles are given a positive electrical charge as they pass through a specialized spray gun. This charge can be imparted by either direct contact with a charged electrode or through an electrostatic field.
2. **Targeting the Surface:** The object to be coated is grounded, providing it with a negative charge. As the positively charged particles are sprayed towards the object, they are attracted to its surface, ensuring even coverage.
3. **Uniform Coverage:** Due to the attraction between the charged particles and the grounded object, the paint wraps around the surface, covering even hard-to-reach areas and complex geometries. This results in a uniform finish with minimal overspray.
#### Advantages of Electrostatic Spraying
– **Reduced Waste:** The efficiency of particle attraction minimizes overspray, reducing material waste and saving costs.
– **High-Quality Finish:** The method produces a smooth and even coat with excellent coverage, reducing the need for touch-ups.
– **Versatility:** Electrostatic spraying can be used with various coatings, including liquid paints, varnishes, and even powders.
– **Environmentally Friendly:** The reduced overspray and material waste contribute to a lower environmental impact.
### Introduction to Powder Coating
**Powder coating** is a dry finishing process that has become increasingly popular as an alternative to traditional wet paint. It is known for its durability, high-quality finish, and environmental benefits.
#### The Powder Coating Process
1. **Preparation:** Before coating, the surface is thoroughly cleaned and pre-treated to remove contaminants like oil, dirt, and rust. This step is crucial for ensuring good adhesion and a smooth finish.
2. **Application:** The coating material, a fine powder made of resin and pigment, is electrostatically charged and sprayed onto the grounded object using a powder spray gun. The charged particles adhere to the surface, forming a uniform layer.
3. **Curing:** After application, the coated object is heated in a curing oven. The powder melts and flows into a continuous film, chemically reacting to form a hard, durable finish. The temperature and time required for curing depend on the specific powder used and the thickness of the coating.
#### Advantages of Powder Coating
– **Durability:** Powder-coated surfaces are highly resistant to chipping, scratching, fading, and wear. The coating provides a tough and resilient finish suitable for various applications.
– **Environmental Impact:** Unlike traditional liquid paints, powder coating does not require solvents, resulting in minimal volatile organic compound (VOC) emissions. This makes it an environmentally friendly option.
– **Color Variety and Finish Options:** Powder coating offers a wide range of colors and finishes, including matte, gloss, metallic, and textured options, allowing for greater customization and aesthetic appeal.
– **Cost-Effectiveness:** The process is efficient, with high transfer efficiency and minimal waste, reducing overall costs.
### Comparing Electrostatic Spraying and Powder Coating
While electrostatic spraying and powder coating share similarities, such as using electrostatic principles for application, they differ in material state and specific applications.
#### Material State
– **Electrostatic Spraying:** Involves liquid paint or coating materials. Suitable for projects requiring a thin layer of coating and specific finishes.
– **Powder Coating:** Utilizes dry powder, requiring curing for film formation. Ideal for applications demanding thicker and more durable coatings.
#### Application and Finish
– **Electrostatic Spraying:** Provides excellent coverage on complex surfaces and is often used for automotive finishes, metal furniture, and appliances.
– **Powder Coating:** Offers robust protection against environmental factors and is preferred for outdoor equipment, industrial machinery, and household items.
### Applications Across Industries
Both techniques find applications in various industries due to their efficiency and high-quality finishes.
#### Automotive Industry
– **Electrostatic Spraying:** Used for applying primers, base coats, and clear coats, offering a sleek and durable finish.
– **Powder Coating:** Ideal for components like wheels, bumpers, and trim parts, providing resistance to corrosion and wear.
#### Industrial Equipment
– **Electrostatic Spraying:** Applied to machinery and equipment parts for protection against rust and wear.
– **Powder Coating:** Suitable for heavy-duty equipment and structures exposed to harsh environments, ensuring longevity and protection.
#### Consumer Goods
– **Electrostatic Spraying:** Utilized in home appliances and furniture, providing a range of finishes and colors.
– **Powder Coating:** Commonly used for outdoor furniture, bicycles, and household items, offering durability and aesthetic appeal.
### Future Trends and Innovations
As technology advances, both electrostatic spraying and powder coating continue to evolve, with new innovations enhancing their capabilities.
#### Smart Coatings
– **Self-Healing Coatings:** Research is underway to develop coatings that can repair minor scratches and damage, extending the lifespan of coated surfaces.
– **Antimicrobial Coatings:** Incorporating antimicrobial properties into coatings for hygiene-sensitive applications, such as medical equipment and public spaces.
#### Automation and Robotics
– **Robotic Spraying Systems:** The integration of robotics in spraying processes improves precision, consistency, and efficiency, reducing labor costs and increasing productivity.
– **AI and Machine Learning:** Implementing AI-driven systems for real-time monitoring and optimization of spraying parameters, ensuring consistent quality and reducing material waste.
#### Sustainable Coating Materials
– **Bio-based Powders:** Development of powders from renewable resources to reduce environmental impact and reliance on fossil fuels.
– **Low-Temperature Curing:** Advancements in curing technology allow for lower-temperature curing, reducing energy consumption and expanding substrate compatibility.
### Conclusion
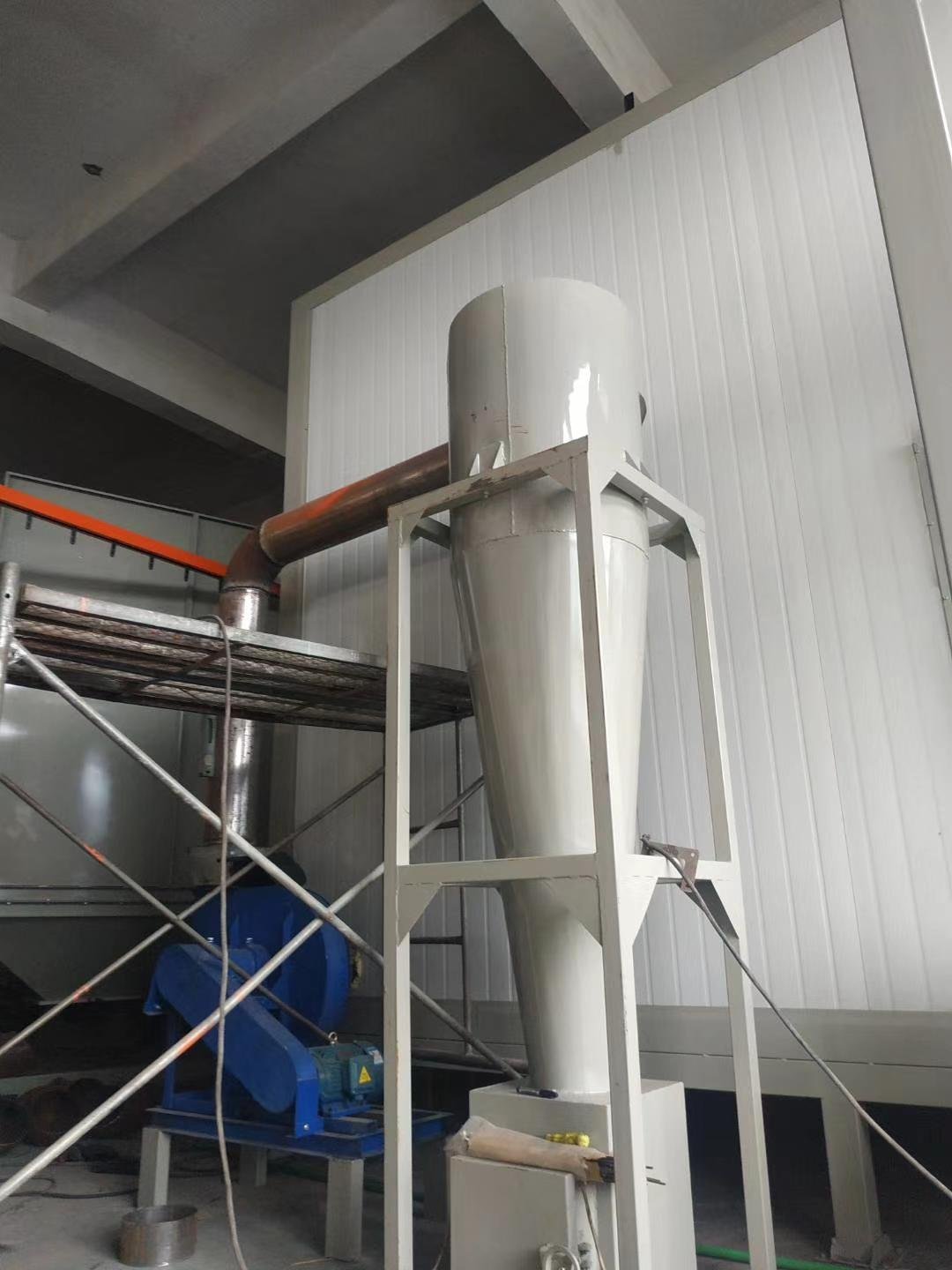
Electrostatic spraying and powder coating are pivotal in modern manufacturing, offering superior finishes, durability, and environmental benefits. As industries continue to prioritize efficiency and sustainability, these techniques are set to play an even more significant role in the future of surface finishing. With ongoing research and technological advancements, we can expect further improvements in coating materials and application methods, driving innovation across various sectors.