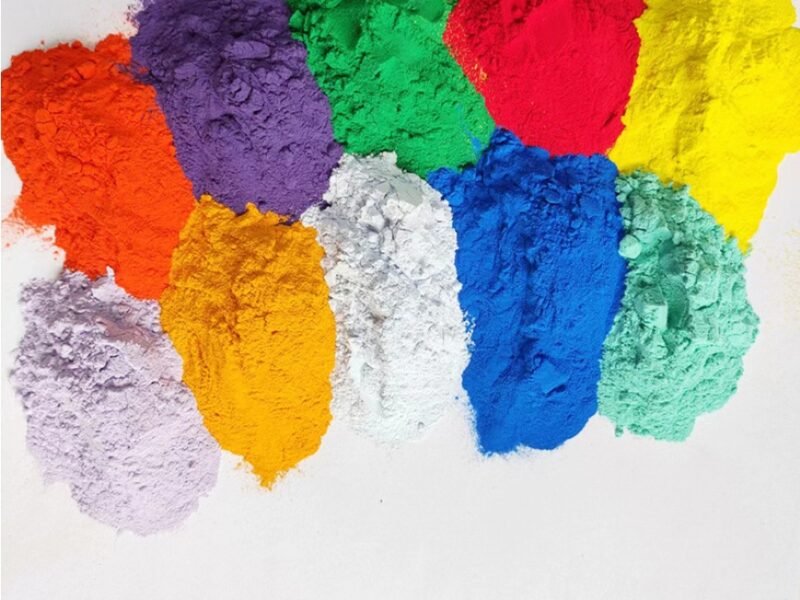
How to analyze the need for grounding of high-voltage electrostatic generators in electrostatic powder spraying equipment?
Grounding high-voltage electrostatic generators in electrostatic powder spraying equipment is crucial to ensuring safe operation and optimal performance. Proper grounding helps prevent electrical hazards, improves the efficiency of the electrostatic charge application, and minimizes powder loss. Here’s how to analyze the need for grounding in these systems:
### **1. Understanding the Role of Grounding in Electrostatic Powder Spraying**
– **Electrical Safety**: High-voltage electrostatic generators used in powder spraying systems operate at high voltages, typically between 60 kV to 100 kV. Grounding helps prevent accidental electrical shocks to operators or damage to equipment in case of malfunction or electrical surges.
– **Enhance Powder Attraction**: Electrostatic grounding ensures that the electrostatic charge on the spray gun and the workpiece is properly balanced, ensuring effective attraction of powder to the substrate. Poor grounding may lead to inefficient powder transfer, resulting in uneven coating and wastage.
– **Prevent Electrostatic Discharge (ESD)**: Proper grounding prevents uncontrolled discharges (sparking), which could damage the spray gun, workpieces, or other sensitive components of the system, as well as cause safety hazards, especially in areas with flammable materials.
—
### **2. Key Considerations for Analyzing the Need for Grounding**
– **Voltage and Power Supply Type**:
– High-voltage electrostatic generators require proper grounding due to their high-voltage output. Analyze whether the voltage output of the electrostatic system aligns with the required safety standards and whether the power supply requires specific grounding precautions.
– Verify that the power supply used for the electrostatic generator is compatible with the grounding system, ensuring the return path for current is properly routed to ground.
– **Manufacturer’s Recommendations**:
– Always refer to the manufacturer’s specifications for the electrostatic spraying equipment, including the recommended grounding procedure. Manufacturers typically provide guidelines on how to ground the generator and related equipment to ensure both performance and safety.
—
### **3. Identify Areas That Require Grounding**
Proper grounding should be applied to multiple parts of the electrostatic powder spraying system:
– **Electrostatic Generator**:
– The high-voltage output of the electrostatic generator should be properly grounded to prevent electrical buildup and ensure the system operates safely and effectively.
– Ensure that the generator’s frame, power supply, and electrical components are grounded according to the manufacturer’s specifications.
– **Spray Gun**:
– The spray gun should be grounded to ensure that the electrostatic charge is effectively transferred to the workpiece, not lost due to static buildup or discharge.
– A well-grounded spray gun ensures that the powder is electrostatically attracted to the workpiece and not wasted through overspray.
– **Workpiece**:
– The workpiece (or the workpiece holder) must also be grounded to complete the circuit for electrostatic powder attraction. If the workpiece is not grounded, the powder may not adhere properly, leading to uneven coating and excessive overspray.
– **Powder Booth**:
– The powder booth or spray area should be properly grounded, as static buildup in the booth can cause dust or powder particles to cling to surfaces. Grounding the booth ensures that any electrostatic charge generated within the booth is safely dissipated.
– **Air Supply**:
– In some cases, grounding the air supply system, particularly if compressed air is used to convey powder, can prevent charge buildup in the system and ensure smooth powder flow without excessive clumping or discharge.
—
### **4. Check for Proper Grounding Resistance**
– **Grounding Resistance Testing**: Use a **ground resistance tester** to check the resistance between the system’s grounded components (such as the electrostatic generator, spray gun, and booth) and the main ground. Typically, the grounding resistance should be below 1 ohm to ensure effective grounding.
– **High resistance** can indicate poor or ineffective grounding, which could lead to electrical hazards and poor powder coating performance.
– **Continuous Monitoring**: Periodically check grounding systems to ensure they remain intact and effective, especially in systems that see frequent use or high-power operation.
—
### **5. Evaluate Grounding in Different Environments**
– **Electrostatic Powder Coating Booth**:
– In a powder coating environment, grounding is especially critical due to the potential for hazardous materials (such as flammable powders) and high-voltage electrostatic fields. Ensure that all conductive parts of the spray system, including the booth, are grounded to prevent buildup of dangerous static charges.
– **Hazardous and Flammable Environments**:
– If the powder coating process is conducted in a hazardous environment (e.g., with combustible powders or in an explosion-prone atmosphere), grounding becomes even more critical. Proper grounding helps prevent accidental sparks or electrostatic discharges that could ignite flammable materials.
– **Indoor vs Outdoor Setup**:
– In indoor setups, where humidity and environmental factors are more controlled, grounding issues can be more easily addressed. In outdoor setups, factors such as weather (rain, wind) and humidity can influence the effectiveness of grounding, requiring additional care and preventive measures.
—
### **6. Implementing a Grounding Plan**
– **Develop a Grounding System**: Establish a comprehensive grounding plan based on the equipment layout and environmental conditions. This plan should outline which components need to be grounded, how grounding is achieved (e.g., grounding rods, conductive paths), and how to verify its effectiveness.
– **Use Conductive Materials**: Use high-conductivity grounding materials (such as copper or aluminum) to minimize resistance in the grounding system and improve electrical flow.
– **Proper Grounding Rod Installation**: Ensure grounding rods are placed correctly in the soil and meet local electrical codes. The depth and placement of these rods depend on the local environment, soil conductivity, and system voltage requirements.
—
### **7. Monitor for Static Buildup and Electrostatic Discharge**
– **Monitor Static Charge**: Use an **electrostatic voltmeter** to measure static charge on critical components (e.g., spray gun, workpiece). If excessive charge is detected, check the grounding system to ensure it is performing as expected.
– **Test for Sparking**: Regularly check for visible sparking or discharge, which can indicate grounding issues. Sparking could damage both the equipment and the workpieces.
—
### **Conclusion**
To analyze the need for grounding high-voltage electrostatic generators in powder spraying equipment, focus on ensuring safe electrical operation, efficient powder attraction, and preventing electrostatic discharge. Proper grounding of the generator, spray gun, workpiece, powder booth, and other components is necessary for both safety and coating quality. Regular testing and monitoring of the grounding system help to prevent issues and maintain efficient operation.
Would you like more information on specific testing or grounding equipment for electrostatic systems?
electrostatic powder coating principle
electrostatic powder coating principles and pharmaceutical applications
electrostatic powder coating problems
electrostatic powder coating process pdf
electrostatic powder coating ptfe
electrostatic powder coating services
electrostatic powder coating site youtube.com
electrostatic powder coating spray gun machine
electrostatic powder coating standard
electrostatic powder coating system manufacturer
electrostatic powder coating technician
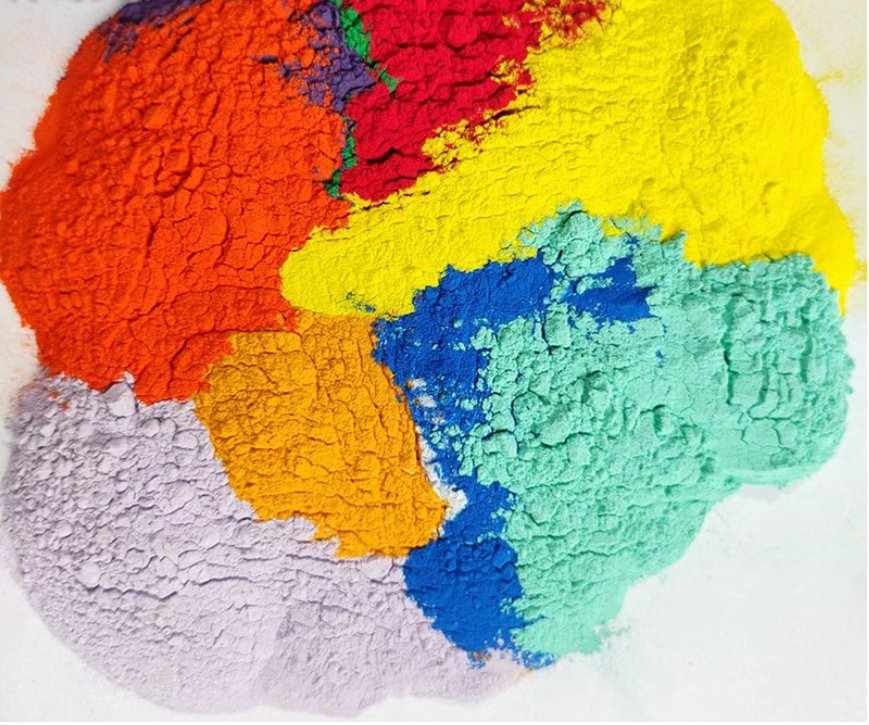