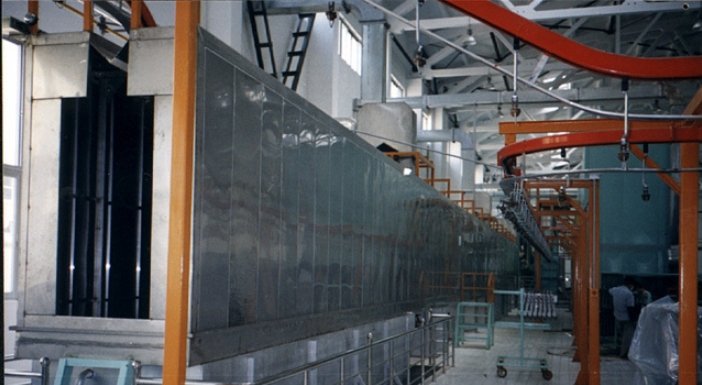
Explosion-proof structure, explosion-proof method and process of powder spraying room on powder electrostatic spraying production line
In powder electrostatic spraying production lines, **explosion-proof design** is crucial because of the potential for **combustible dust** and **electrostatic discharge** (ESD) that could lead to a fire or explosion. Since powder coatings are often flammable and can create hazardous dust clouds in the air, it’s essential to implement safety measures that protect both workers and equipment. Here’s a breakdown of the **explosion-proof structure**, **explosion-proof methods**, and **processes** for powder spraying rooms:
—
### **Explosion-Proof Structure for Powder Spraying Rooms**
#### **1. Design and Layout Considerations**
– **Room Layout**: Powder spraying rooms should be designed with sufficient space to allow airflow and prevent powder buildup. Adequate ventilation and airflow systems help prevent the accumulation of flammable powders in confined spaces.
– **Explosion-Proof Walls and Floors**: The room’s structure must be constructed using **explosion-resistant materials** such as **steel, concrete, or non-combustible panels**. The walls and floors should be designed to withstand internal pressure in case of an explosion. The flooring should also be smooth and easy to clean to prevent powder accumulation.
– **Ceiling and Ventilation**: The ceiling should be high enough to ensure proper airflow and reduce the chances of powder buildup near the ceiling. **Explosion-proof ventilation systems** (fans, exhaust ducts) should be used to remove combustible dust from the air before it reaches hazardous levels.
#### **2. Explosion-Proof Equipment**
– **Spray Guns and Electrostatic Generators**: These devices must be designed with **spark-resistant materials** and be grounded properly to avoid creating static sparks that could trigger a fire or explosion. Explosion-proof spray guns with conductive properties can minimize the risk of sparks.
– **Electrical Equipment**: All electrical equipment in the spray booth, including lights, motors, fans, and power outlets, should be **explosion-proof** and meet **ATEX** (European Union) or **UL (Underwriters Laboratories)** explosion-proof standards. These certifications ensure that electrical components are sealed and designed to prevent sparks.
– **Powder Recovery System**: The powder recovery system, which collects oversprayed powder, must be **dust-tight** and use **explosion-proof fans** and motors to ensure that no ignition sources are present. Recovery hoppers and ducts should be well-sealed to avoid powder leakage.
#### **3. Structural Explosion-Proof Features**
– **Pressure Relief Panels**: Explosion-proof rooms should include **pressure relief panels** or **rupture discs** that release excess pressure in the event of an explosion. These panels prevent the building from sustaining structural damage by allowing the pressure to escape in a controlled manner.
– **Explosion Suppression Systems**: These systems are activated if an explosion is detected. They use specialized agents (such as chemicals or inert gases) to suppress the explosion and prevent it from spreading.
—
### **Explosion-Proof Methods for Powder Spraying Rooms**
#### **1. Ventilation and Airflow Control**
– **Explosion-Proof Ventilation Systems**: Ventilation plays a key role in reducing the concentration of explosive dust in the air. High-efficiency **explosion-proof exhaust fans** should be installed to draw flammable powders away from the work area. These fans need to be regularly maintained to ensure they’re free of buildup and operating at optimal capacity.
– **Airflow Management**: Properly designed air curtains or airflow control devices should be placed at entry and exit points to prevent the ingress of combustible dust outside the spray booth. **Negative pressure** (suction-based systems) should be maintained to ensure that dust is continuously pulled away from the work area.
#### **2. Grounding and Electrostatic Control**
– **Proper Grounding of Equipment**: As electrostatic powder spraying involves high voltages (e.g., 60 kV-100 kV), grounding of all equipment is essential to prevent electrostatic discharges (ESDs), which could ignite flammable powder. All electrostatic spraying equipment, including the spray guns and powder feeders, must be grounded according to manufacturer instructions.
– **Use of Conductive Materials**: Spray booths should have conductive flooring and walls to help dissipate any static charge that might accumulate on surfaces, thus preventing the risk of a spark. **Static-neutralizing devices** can be used to further mitigate electrostatic buildup.
#### **3. Explosion-Proof Lighting and Electrical Systems**
– **Explosion-Proof Lighting**: All lights in the spray booth should be **sealed** and **explosion-proof** to prevent sparks. Using **LED lights** or **fluorescent lights** that are rated for hazardous environments ensures safety.
– **Electrical Wiring**: Electrical wiring in the powder spraying room should be installed in sealed, non-combustible conduits. Electrical junction boxes should be explosion-proof and have covers to prevent the accidental sparking of wires.
#### **4. Powder Collection and Disposal Systems**
– **Efficient Powder Recovery**: A powder recovery system should be used to collect oversprayed powder. The system should be sealed and use explosion-proof motors and fans to prevent dust ignition.
– **Powder Storage**: Recovered powder should be stored in **airtight containers** to prevent dust from spreading. Any excess powder should be disposed of in a way that minimizes dust exposure and the risk of ignition.
—
### **Explosion-Proof Process in Powder Spraying Rooms**
#### **1. Pre-Process Safety Measures**
– **Safety Checks**: Before starting the spraying process, verify that all equipment is properly grounded, and that the ventilation and recovery systems are functioning correctly. Ensure that all electrical equipment meets explosion-proof standards.
– **Hazardous Area Classification**: Classify the room into hazardous zones based on the likelihood of dust accumulation and the potential for ignition. This will determine the required explosion-proof equipment standards and safety precautions.
#### **2. Spray Process Control**
– **Controlled Application of Powder**: During the spraying process, monitor the powder flow rate to ensure that excessive powder does not accumulate in the air, leading to dangerous concentrations. Use automated spraying systems to ensure precise powder application and minimize waste.
– **Regular Cleaning**: Clean the booth regularly using **explosion-proof vacuums** to remove any dust that may have accumulated. Cleaning should be done during shutdown periods to prevent the ignition of powder particles.
#### **3. Post-Process Safety**
– **Post-Spraying Ventilation**: After spraying, continue to run the ventilation system for some time to remove any remaining airborne dust and reduce the risk of residual powder igniting.
– **Inspection of Equipment**: After the spraying process, inspect the equipment for any signs of wear, damage, or dust accumulation. Ensure that the grounding and electrical systems are still intact and functioning.
—
### **Conclusion**
Explosion-proof design and methods in a powder spraying room are critical for ensuring safety in electrostatic powder coating production lines. The key elements involve a combination of proper equipment design, safe operational practices, and continuous monitoring. Explosion-proof structures, effective ventilation, grounding of equipment, and explosion suppression systems are essential to minimize the risk of explosions and fires due to the accumulation of combustible dust or electrostatic discharge.
Would you like further details on specific explosion-proof equipment or safety regulations for powder coating environments?
electrostatic powder coating technician jobs
electrostatic powder coating technology
electrostatic powder coating theory
electrostatic powder coating thickness
electrostatic powder coating voltage
electrostatic powder coating vs powder coating
electrostatic powder coating wikipedia
electrostatic powder coating without baking
electrostatic powder coating without making
electrostatic powder coatings
electrostatic powder coatings definition
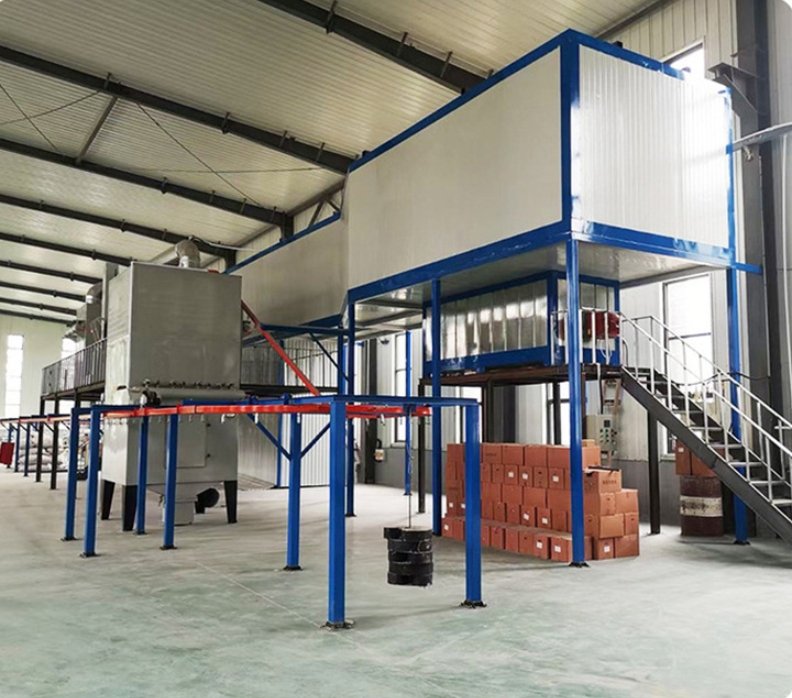