
How to deal with the honeycomb appearance of electrostatic powder spraying powder coating?
How to deal with the honeycomb appearance of electrostatic powder spraying powder coating?
The **honeycomb appearance** in electrostatic powder coating refers to an uneven, textured defect that resembles a honeycomb structure. This issue can compromise the coating’s appearance and performance. Here’s a detailed guide on the possible causes and solutions:
—
### **1. Poor Surface Preparation**
– **Cause**: Contaminants such as oil, grease, dirt, or rust on the workpiece create uneven adhesion, leading to the honeycomb effect.
– **Solution**:
– Thoroughly clean the surface with degreasers, solvents, or abrasives.
– Use pre-treatment methods like phosphating or sandblasting to prepare the surface.
– Ensure the surface is completely dry before spraying.
—
### **2. Improper Powder Application**
– **Cause**: Uneven or excessive powder application can create inconsistent thickness, leading to honeycomb patterns during curing.
– **Solution**:
– Adjust the powder flow rate and gun settings to ensure even application.
– Maintain the recommended spray gun-to-workpiece distance (typically 6–12 inches).
– Overlap spray passes consistently to avoid thin or thick spots.
—
### **3. Incorrect Curing Process**
– **Cause**: Improper curing temperatures or times can cause uneven melting and flow of the powder.
– **Solution**:
– Verify the curing oven’s temperature and time settings match the powder manufacturer’s specifications.
– Ensure the oven provides uniform heat distribution.
– Avoid under-curing or over-curing, which can disrupt the coating’s uniformity.
—
### **4. Environmental Contamination**
– **Cause**: Dust, moisture, or particles in the spray booth or curing area can embed in the coating, causing honeycomb defects.
– **Solution**:
– Use a clean, filtered air supply and ensure the spray booth is free of contaminants.
– Maintain a controlled environment with low humidity (<50%) and proper ventilation.
—
### **5. Low-Quality Powder**
– **Cause**: Poor-quality, expired, or contaminated powder may not flow evenly during curing.
– **Solution**:
– Use fresh, high-quality powder from a reputable supplier.
– Store powder in a dry, cool environment to prevent contamination or clumping.
—
### **6. Inconsistent Electrostatic Charge**
– **Cause**: A weak or inconsistent electrostatic charge can cause uneven powder deposition.
– **Solution**:
– Check the spray gun’s voltage settings and ensure proper grounding of the workpiece.
– Regularly inspect and maintain the electrostatic charging system.
—
### **7. Faraday Cage Effect**
– **Cause**: Recessed or complex areas of the workpiece may receive uneven powder coverage due to electrostatic shielding.
– **Solution**:
– Reduce the voltage slightly or use a spray gun with a pulsating or cloud mode to improve penetration.
– Adjust the spray angle to reach recessed areas more effectively.
—
### **8. Improper Film Thickness**
– **Cause**: Applying the powder too thickly or unevenly can cause surface defects, including honeycomb patterns.
– **Solution**:
– Maintain the recommended film thickness (typically 2–4 mils or as specified by the manufacturer).
– Avoid over-spraying and remove excess powder buildup before curing.
—
### **9. Incompatible Powder Types**
– **Cause**: Mixing different powder types or using incompatible powders can lead to inconsistent flow and appearance.
– **Solution**:
– Use only one type of powder per application.
– Ensure the powder matches the intended application and curing process.
—
### **10. Gas Outgassing**
– **Cause**: Gas released from porous substrates (e.g., cast aluminum) or trapped moisture during curing can create a honeycomb or pinhole effect.
– **Solution**:
– Preheat the workpiece to degas it before powder application.
– Use powders designed for outgassing-prone materials, such as low-temperature curing powders.
—
### **Steps to Correct Existing Defects**
1. **Identify the Root Cause**: Inspect the workpiece, powder, and process to pinpoint the issue.
2. **Rework**: Sand or grind the defective coating to create a smooth surface.
3. **Reapply Powder**: Re-spray the workpiece following best practices.
4. **Recure Properly**: Ensure the correct curing conditions to avoid repeating the defect.
—
### **Prevention Summary**
– Ensure thorough surface preparation.
– Use high-quality powder and store it properly.
– Maintain consistent spray and curing processes.
– Control the environment in the spray booth and curing oven.
– Regularly inspect and maintain equipment.
By addressing these factors, you can prevent the honeycomb appearance and achieve a smooth, uniform powder coating.
electrostatic epoxy powder coating
electrostatic fluidized bed powder coating
electrostatic gun for powder coating
electrostatic painting powder coatings
electrostatic powder coating equipment
electrostatic powder coating gun
electrostatic powder coating line
electrostatic powder coating process
electrostatic powder coating system
electrostatic powder spray gun
electrostatic spray powder coating
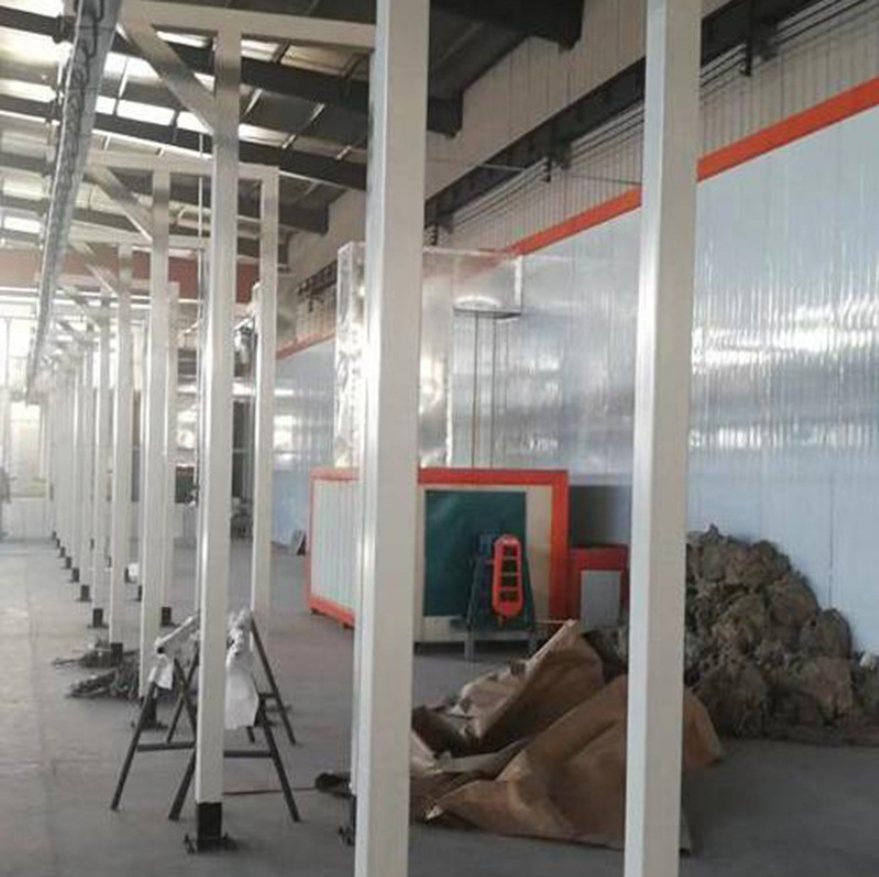