How to deal with the yellowing of electrostatic powder spraying powder coating?
How to deal with the yellowing of electrostatic powder spraying powder coating?
**Yellowing** in electrostatic powder coating occurs when the color of the coating shifts towards yellow, affecting the aesthetic quality of the finish. It can happen during or after the curing process and is often due to chemical or environmental factors. Here’s a guide to the causes and solutions:
—
### **1. Overcuring**
– **Cause**: Excessive curing time or high temperatures in the oven can degrade the pigments or resins in the powder, leading to discoloration.
– **Solution**:
– Verify and adhere to the powder manufacturer’s recommended curing temperature and time.
– Regularly calibrate the curing oven to ensure even and accurate temperature distribution.
—
### **2. Improper Oven Ventilation**
– **Cause**: Insufficient ventilation in the curing oven can cause fumes or byproducts of curing to accumulate, leading to yellowing.
– **Solution**:
– Ensure proper airflow and ventilation in the curing oven.
– Clean the oven regularly to remove any buildup of contaminants.
—
### **3. UV or Heat Exposure**
– **Cause**: Prolonged exposure to sunlight (UV rays) or high temperatures after curing can cause the coating to yellow over time.
– **Solution**:
– Use UV-resistant powders for outdoor applications.
– Minimize exposure to direct sunlight or extreme heat by applying protective measures like shading.
—
### **4. Contaminants in the Powder or Equipment**
– **Cause**: Contaminants like old powder residues, grease, or dirt in the powder spray system or curing oven can result in discoloration.
– **Solution**:
– Clean the powder spraying equipment, hoses, and hopper regularly.
– Prevent cross-contamination by using separate equipment for different colors.
—
### **5. Low-Quality Powder**
– **Cause**: Poor-quality powders may contain unstable pigments or resins that yellow more easily during curing or over time.
– **Solution**:
– Purchase powder coatings from reputable manufacturers with proven stability and quality.
– Check the powder’s shelf life and store it in a cool, dry place.
—
### **6. Chemical Reactions**
– **Cause**: The powder coating may react with gases, cleaning chemicals, or other environmental substances, leading to discoloration.
– **Solution**:
– Avoid using acidic or harsh cleaning agents on the coated surface.
– Use pre-treatment processes compatible with the powder coating material to prevent residual chemical reactions.
—
### **7. Moisture or Humidity**
– **Cause**: High humidity during powder storage, application, or curing can affect the powder’s composition, leading to discoloration.
– **Solution**:
– Store powder in a dry environment with low humidity (<50%).
– Ensure the workpiece and powder are dry before application.
—
### **8. Substrate Issues**
– **Cause**: Contaminants or impurities in the substrate material can leach into the coating during curing, causing yellowing.
– **Solution**:
– Thoroughly clean and pre-treat the substrate to remove contaminants.
– Use primers or barrier layers for substrates prone to leaching.
—
### **9. Aging and Weathering**
– **Cause**: Over time, environmental factors such as sunlight, oxygen, and pollutants can degrade the coating and cause yellowing.
– **Solution**:
– Use powders formulated for long-term durability and resistance to environmental factors.
– Apply a clear topcoat for additional protection.
—
### **Steps to Correct Existing Yellowing**
1. **Assess the Severity**: Determine whether the yellowing is surface-level or affects the entire coating.
2. **Clean the Surface**: Use mild cleaning agents to remove any external contaminants or stains.
3. **Reapply Coating**: If the yellowing cannot be cleaned or is deep, sand or strip the coating and reapply a fresh layer.
4. **Optimize Processes**: Adjust curing settings, equipment maintenance, or environmental controls to prevent recurrence.
—
### **Prevention Summary**
– Follow manufacturer recommendations for curing conditions.
– Maintain clean equipment and a controlled environment.
– Use high-quality, UV-resistant powders for outdoor applications.
– Store powder in proper conditions to maintain stability.
By addressing these factors, you can minimize yellowing and ensure durable, visually appealing coatings.
electrostatic powder coating
electrostatic painting vs powder coating
electrostatic powder painting
electrostatic powder
electrostatic powder coating machine
electrostatic powder paint
electrostatic powder spray
electrostatic powder spraying
powder electrostatic
958 electrostatic powder coating machine
armur electrostatic powder
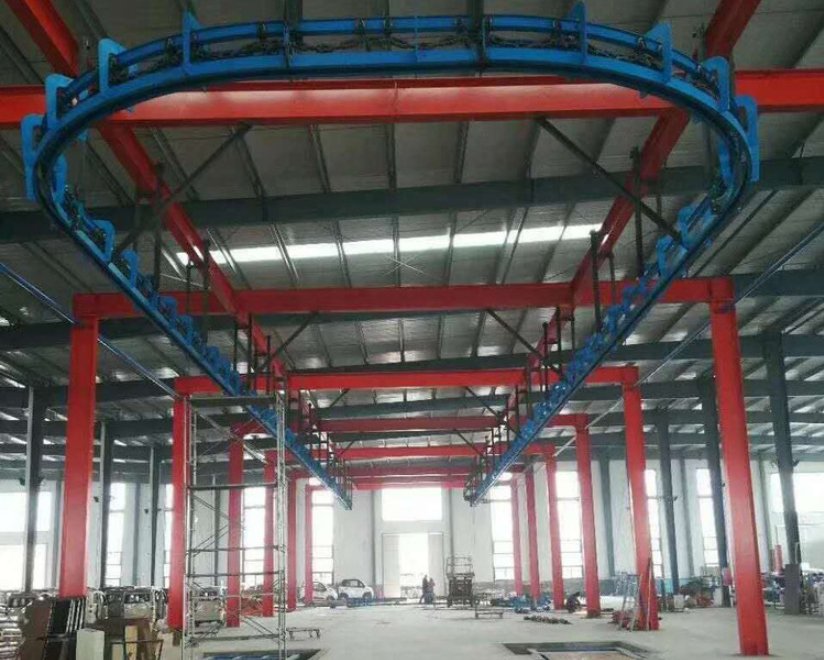