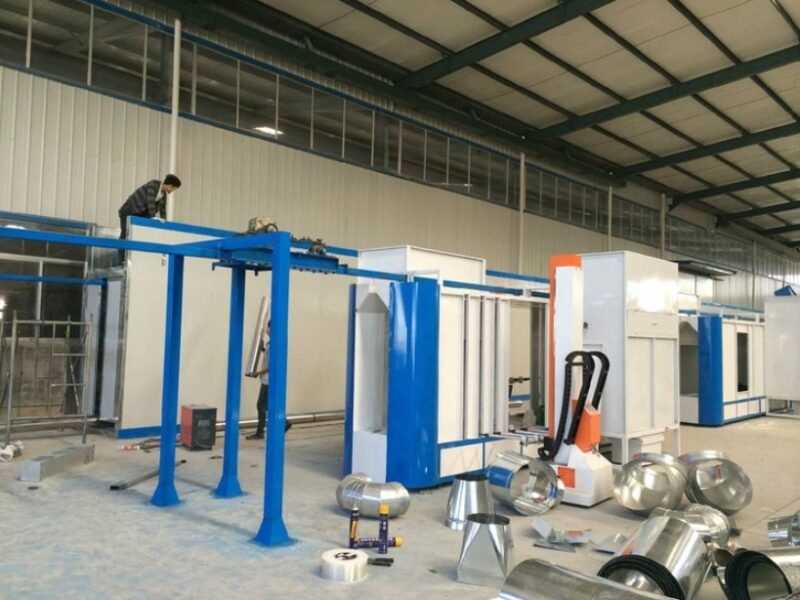
How to deal with the poor impact strength of electrostatic powder spraying powder coating?
How to deal with the poor impact strength of electrostatic powder spraying powder coating?
**Poor impact strength** in electrostatic powder coatings can result in coatings that crack, chip, or peel when subjected to physical stress or impact. This issue is often a result of poor formulation, application, or curing processes. Here’s how to address and prevent this problem:
—
### **1. Incorrect Curing Parameters**
– **Cause**: Insufficient or excessive curing time or temperature can affect the chemical bonds in the powder, weakening the impact resistance of the coating.
– **Solution**:
– Ensure proper curing according to the powder manufacturer’s specifications (temperature and time).
– Use a thermometer to verify the actual temperature inside the curing oven and ensure even heat distribution.
– Avoid under-curing or over-curing, as both can negatively affect the coating’s impact resistance.
—
### **2. Poor Powder Formulation**
– **Cause**: The powder itself may have a poor resin system that is not designed to withstand impact stress (e.g., rigid, brittle formulations).
– **Solution**:
– Use powders specifically formulated for high impact resistance (e.g., epoxy-polyester hybrids, polyurethanes, or thermoplastic powder coatings).
– Consult with your powder supplier to choose the right formulation for the intended application and impact load.
– Consider using powders that include flexibilizers or impact modifiers in their chemical composition.
—
### **3. Incorrect Film Thickness**
– **Cause**: Coating the workpiece with too thin or too thick a layer can affect its ability to absorb impact forces.
– **Solution**:
– Apply the recommended film thickness (usually between 2-4 mils).
– A too-thin coating may not have enough material to absorb impact forces, while a too-thick coating may become brittle.
– Ensure uniform powder application to avoid weak spots.
—
### **4. Poor Surface Preparation**
– **Cause**: Inadequate cleaning or preparation of the substrate can result in poor adhesion, making the coating more prone to cracking or chipping under impact.
– **Solution**:
– Thoroughly clean and prepare the workpiece (removing oils, rust, dust, and debris) using sandblasting, chemical treatments, or abrasive cleaning methods.
– Apply a suitable primer to improve adhesion if necessary, especially for difficult-to-coat metals.
—
### **5. Improper Powder Application Technique**
– **Cause**: Improper spraying technique can result in uneven coating or areas of weak bonding, compromising impact strength.
– **Solution**:
– Maintain the correct spray gun-to-workpiece distance (typically 6–12 inches).
– Use consistent spray motion to ensure an even, smooth coating.
– Avoid excessive powder buildup or under-spraying, which can lead to inconsistent hardness or strength.
—
### **6. Poor Substrate Compatibility**
– **Cause**: Some substrates may not bond well with the powder, resulting in reduced adhesion and poor impact strength.
– **Solution**:
– Use a primer or pre-treatment for substrates that are known to be difficult to coat (e.g., aluminum or galvanized steel).
– Make sure the workpiece is compatible with the specific type of powder coating you’re using.
—
### **7. Low-Quality or Expired Powder**
– **Cause**: Old or improperly stored powder can lose its impact resistance properties over time, leading to weak coatings.
– **Solution**:
– Always use fresh, high-quality powder coatings from reputable manufacturers.
– Store powder in a cool, dry place, and regularly check for clumps or signs of degradation.
– Sift powder before use to remove any clumps or contaminants.
—
### **8. Temperature or Humidity Issues During Application**
– **Cause**: High humidity or low temperatures during application can affect the powder’s flow, curing, and final hardness.
– **Solution**:
– Maintain optimal environmental conditions for powder spraying (e.g., temperature between 65°F and 85°F and humidity below 50%).
– Avoid spraying in damp conditions that may cause powder clumping or improper curing.
—
### **9. Mechanical Stress During Handling**
– **Cause**: Handling of the workpieces before the coating has fully cured can lead to deformation or cracking.
– **Solution**:
– Allow sufficient curing time for the powder coating to fully harden before handling or applying any stress to the part.
– Handle coated parts with care to avoid mechanical impact while they are still curing or cooling.
—
### **10. Testing and Quality Control**
– **Cause**: Lack of quality control during the application process may lead to weak spots that can compromise the impact resistance.
– **Solution**:
– Conduct quality control tests, including impact resistance testing, on the finished coating.
– Apply test pieces to evaluate the impact performance and adjust process parameters as needed.
– Utilize automated systems that ensure consistent application and curing.
—
### **Summary of Solutions**:
1. **Optimize curing parameters** to ensure proper bonding and flexibility of the coating.
2. **Choose the right powder formulation** designed for high impact strength.
3. **Maintain proper film thickness** for balanced flexibility and strength.
4. **Ensure proper surface preparation** to promote adhesion.
5. **Use correct application techniques** to avoid weak spots or uneven coverage.
6. **Select the appropriate substrate and primer** for better adhesion.
7. **Use high-quality, fresh powder** and store it properly.
8. **Maintain optimal environmental conditions** during spraying and curing.
9. **Allow proper curing time** before handling coated parts.
By following these guidelines and making adjustments to your process, you can significantly improve the impact strength of your electrostatic powder coating.
china electrostatic powder coating equipment
china electrostatic powder coating machine
china electrostatic powder painting equipment
china electrostatic powder painting equipment manufacturer
china electrostatic powder painting equipment supplier
corrosion resistant electrostatic powder
difference between electrostatic painting and powder coating
difference between powder coating and electrostatic paint
diy electrostatic powder coating
ectfe electrostatic powder
electrostatic adhesion powder