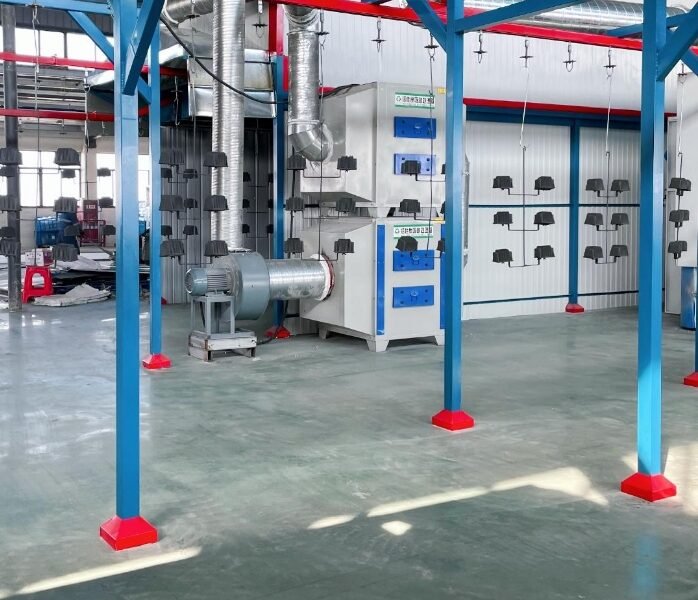
What are the precautions for electrostatic powder spraying?
What are the precautions for electrostatic powder spraying?
Electrostatic powder spraying requires careful attention to safety, equipment handling, and process optimization to ensure high-quality results and a safe working environment. Here are key precautions to consider:
### 1. **Safety Precautions**:
– **Grounding**: Ensure all parts, equipment, and operators are properly grounded to prevent static buildup and minimize the risk of electric shock or fire.
– **Personal Protective Equipment (PPE)**: Operators should wear appropriate PPE, including gloves, safety goggles, dust masks or respirators, and anti-static clothing.
– **Ventilation**: Maintain adequate ventilation in the spray booth to prevent powder accumulation in the air, which could pose a fire or explosion hazard.
– **Fire Prevention**: Keep flammable materials away from the spraying area and ensure fire extinguishers are readily available. Use explosion-proof equipment in areas where powder might accumulate.
### 2. **Equipment Handling**:
– **Regular Maintenance**: Perform routine maintenance on spraying equipment, including cleaning spray guns, hoppers, and filters, to ensure consistent performance and prevent malfunctions.
– **Powder Storage**: Store powders in a cool, dry place to prevent moisture absorption, which can affect the coating quality. Use powders within their recommended shelf life.
– **Color Changes**: Clean equipment thoroughly when changing colors to avoid contamination and ensure uniform application of the new color.
### 3. **Application Process**:
– **Proper Grounding of Parts**: Ensure the parts being coated are securely grounded to allow for effective electrostatic attraction of the powder.
– **Spray Gun Distance and Angle**: Maintain an appropriate distance (typically 6-12 inches) and angle between the spray gun and the part to ensure even coverage and minimize overspray.
– **Powder Flow Rate**: Adjust the powder flow rate and air pressure to achieve a smooth, even application. Excessive flow can lead to uneven coatings and wastage.
– **Temperature Control**: Ensure the curing oven reaches and maintains the correct temperature for the specified duration to achieve proper adhesion and finish.
### 4. **Quality Control**:
– **Surface Preparation**: Clean and pre-treat parts thoroughly to remove contaminants like oil, grease, and rust, which can affect coating adhesion and durability.
– **Coating Thickness**: Monitor the coating thickness to ensure it meets specifications, avoiding issues like orange peel (too thick) or poor coverage (too thin).
– **Inspection**: Inspect coated parts for defects such as pinholes, uneven coverage, or contamination before curing. Address any issues promptly.
### 5. **Environmental and Health Considerations**:
– **Powder Recovery**: Use a powder recovery system to capture overspray and reduce waste. This also helps in maintaining a cleaner working environment.
– **Dust Control**: Regularly clean the spray booth and surrounding areas to prevent powder accumulation and reduce dust exposure.
By following these precautions, operators can ensure a safe, efficient, and high-quality electrostatic powder spraying process, minimizing risks and maximizing the durability and aesthetic appeal of the coatings.
electrostatic fluidization bed for powder coating machine
electrostatic fluidized bed powder coating equipment
electrostatic gun for powder
electrostatic gun for talcum powder
electrostatic gun powder
electrostatic gun powder coating
electrostatic magic diy powder coating paint system
electrostatic magic diy powder coating system
electrostatic magic powder
electrostatic magic powder coating peterborough
electrostatic magic powder coating review
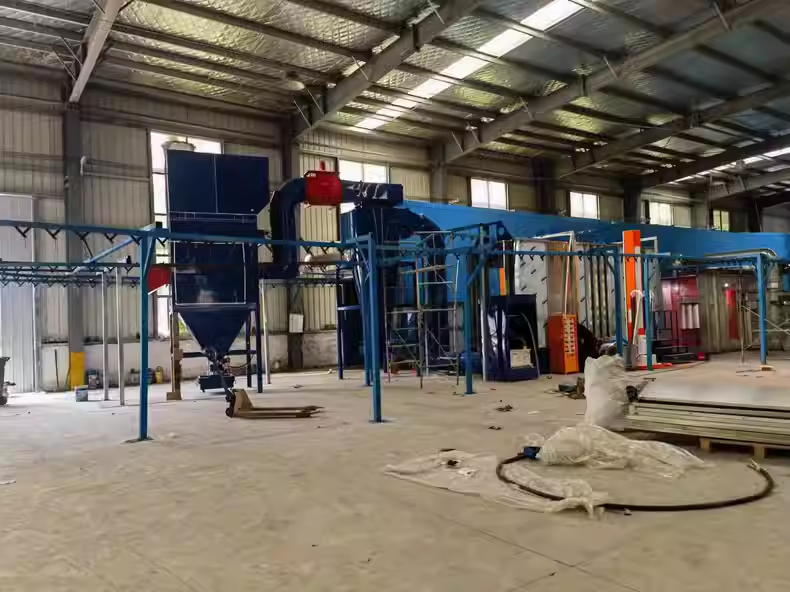