
How to operate epoxy powder electrostatic spraying equipment correctly?
How to operate epoxy powder electrostatic spraying equipment correctly?
Operating epoxy powder electrostatic spraying equipment correctly involves several steps, including preparation, equipment setup, application, and maintenance. Here’s a detailed guide:
### 1. **Preparation**:
– **Surface Preparation**:
– Clean the parts thoroughly to remove contaminants like oil, grease, dirt, and rust. This can be done through degreasing, sandblasting, or chemical pre-treatment.
– Ensure the surface is dry and free from any residues that could affect powder adhesion.
– **Powder Preparation**:
– Check that the epoxy powder is within its shelf life and stored properly (in a cool, dry place).
– Fluidize the powder in the hopper by introducing low-pressure air to ensure it flows consistently.
### 2. **Equipment Setup**:
– **Grounding**:
– Ensure the parts to be coated, the spray gun, and the operator are properly grounded to prevent static buildup.
– **Spray Gun Settings**:
– Adjust the voltage settings on the spray gun according to the manufacturer’s recommendations (usually between 60-100 kV).
– Set the appropriate powder flow rate and air pressure for consistent application.
– **Booth and Ventilation**:
– Ensure the spray booth is clean and equipped with proper ventilation to manage overspray and maintain a safe working environment.
– **Curing Oven**:
– Preheat the curing oven to the recommended temperature for the epoxy powder (usually 180-220°C or 356-428°F).
### 3. **Application Process**:
– **Positioning**:
– Arrange the parts on racks or hangers to allow full access and ensure they are properly spaced for even coating.
– **Spraying**:
– Hold the spray gun 6-12 inches from the surface at a consistent distance and angle.
– Apply the powder in smooth, even strokes, overlapping slightly to ensure full coverage without excessive buildup.
– Pay attention to edges, corners, and recessed areas to avoid thin spots or Faraday cage effects (where powder does not reach complex geometries).
– **Inspection**:
– Inspect the coated parts for uniformity and coverage before curing. Reapply powder if necessary to correct any defects.
### 4. **Curing**:
– **Curing Cycle**:
– Place the coated parts in the preheated oven.
– Cure according to the manufacturer’s recommended time and temperature to ensure proper crosslinking of the epoxy resin.
– Monitor the oven temperature to maintain consistent curing conditions.
– **Cooling**:
– Allow the parts to cool down gradually after curing to avoid thermal shock and ensure the coating’s integrity.
### 5. **Post-Application Maintenance**:
– **Cleaning**:
– Clean the spray gun, hopper, and booth regularly to prevent powder buildup and contamination, especially when changing colors.
– **Inspection and Quality Control**:
– Inspect the finished parts for defects such as pinholes, uneven thickness, or poor adhesion.
– Perform any necessary rework or touch-ups.
### 6. **Safety Measures**:
– **Personal Protective Equipment (PPE)**:
– Wear gloves, goggles, dust masks or respirators, and anti-static clothing to protect against powder inhalation and skin contact.
– **Fire Safety**:
– Keep flammable materials away from the spraying area and ensure fire extinguishers are accessible.
By following these steps, you can ensure the correct and efficient operation of epoxy powder electrostatic spraying equipment, resulting in high-quality and durable coatings.
electrostatic magic powder coating system
electrostatic manual powder coating system cl 668 l3
electrostatic paint powder coating
electrostatic paint sprayer vs powder coating
electrostatic paint vs powder coat
electrostatic painting and powder coating
electrostatic painting and powder coating las vegas nv
electrostatic painting powder coating
electrostatic painting powder coating what is the difference between
electrostatic painting powder coding
electrostatic painting wet vs powder coating
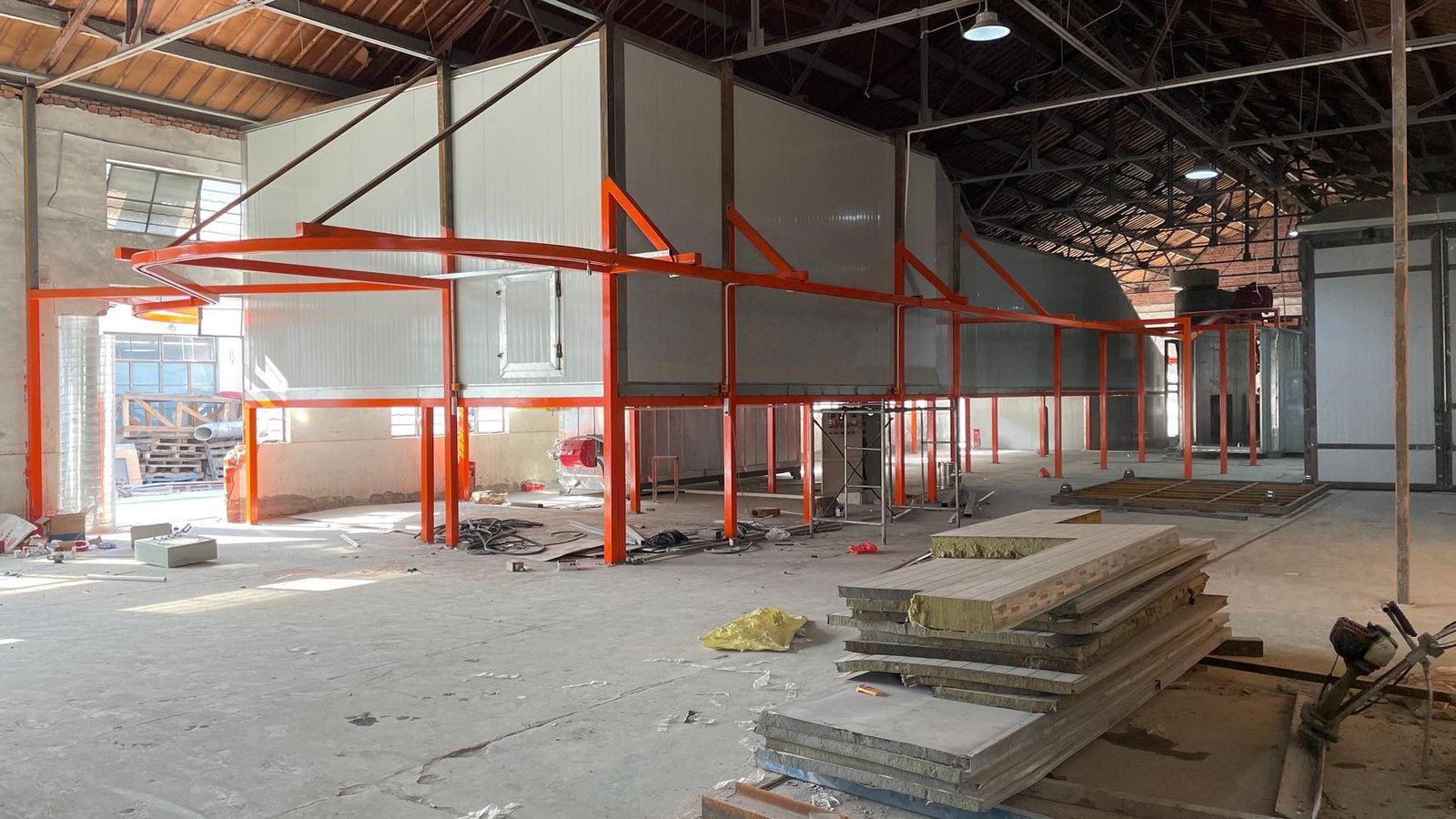