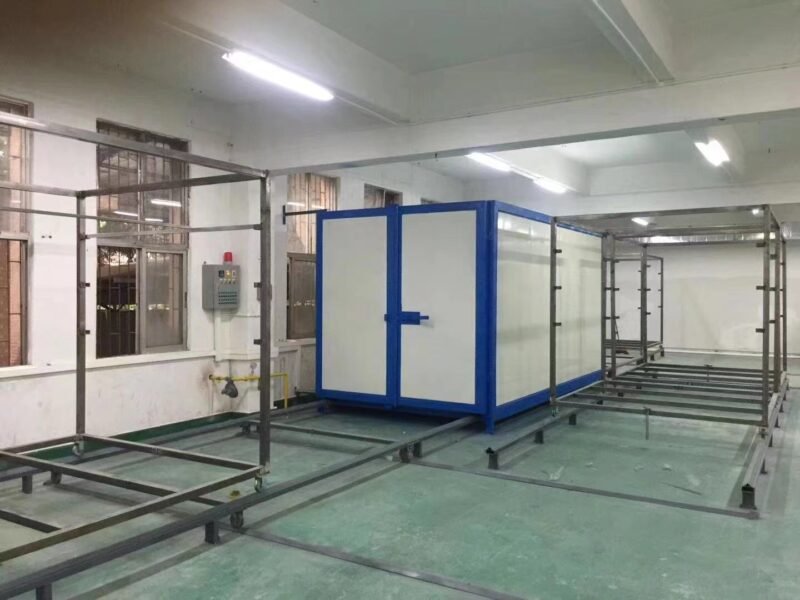
How to distinguish the quality of electrostatic powder spraying?
How to distinguish the quality of electrostatic powder spraying?
Distinguishing the quality of electrostatic powder spraying involves evaluating several factors related to the coating’s appearance, durability, and adhesion. Here are the key aspects to assess:
### 1. **Visual Inspection**:
– **Uniformity of Coating**:
– Check for even thickness and consistency across the entire surface. A high-quality coating should be smooth and uniform without visible thin spots or excessive buildup.
– **Color Consistency**:
– The color should be consistent and match the specified shade. Look for any variations or patchiness, which may indicate improper application or issues with the powder.
– **Finish Quality**:
– Assess the surface finish for the desired texture (glossy, matte, textured) and ensure it meets the specifications. Look for defects like orange peel, pinholes, or runs.
### 2. **Adhesion**:
– **Cross-Cut Test**:
– Perform a cross-cut adhesion test by making small cuts in a grid pattern on the coated surface, then applying adhesive tape and pulling it off. Minimal or no coating should be removed if adhesion is good.
– **Pull-Off Test**:
– A pull-off adhesion test involves applying a specified force to detach the coating. This measures the coating’s adhesion strength and its ability to bond to the substrate.
### 3. **Coating Thickness**:
– **Thickness Measurement**:
– Use a coating thickness gauge to measure the coating’s thickness and ensure it falls within the specified range. Consistent thickness is crucial for both appearance and performance.
### 4. **Durability Tests**:
– **Scratch Resistance**:
– Test the coating’s resistance to scratching using a standardized scratch test or pencil hardness test. A high-quality coating should resist damage from minor abrasions.
– **Impact Resistance**:
– Perform an impact resistance test by dropping a weight onto the coated surface. The coating should withstand the impact without cracking or flaking.
– **Flexibility**:
– Evaluate the coating’s flexibility by bending the coated part or using a mandrel test. The coating should not crack or peel under bending stress.
### 5. **Environmental Resistance**:
– **Corrosion Resistance**:
– Conduct a salt spray test or immersion test to assess the coating’s resistance to corrosion, especially for parts exposed to harsh environments.
– **UV Resistance**:
– Expose the coating to UV light to test its resistance to fading, chalking, or degradation. This is especially important for outdoor applications.
– **Chemical Resistance**:
– Test the coating’s resistance to various chemicals, such as solvents, acids, or alkalis, depending on the intended application.
### 6. **Curing Quality**:
– **Curing Inspection**:
– Ensure the coating is fully cured by conducting a solvent resistance test (e.g., MEK double rub test). A properly cured coating should resist solvent removal.
– **Gloss Retention**:
– Check the gloss level of the coating after curing to ensure it matches the specifications and shows no signs of over-baking or under-baking.
### 7. **Powder Reclaim and Reuse**:
– **Powder Consistency**:
– If using reclaimed powder, ensure it maintains consistent flow and application properties to avoid variations in coating quality.
By carefully evaluating these factors, you can distinguish the quality of electrostatic powder spraying and ensure that the coating meets the desired standards for appearance, performance, and durability.
electrostatic powder coating machine manufacturer
electrostatic powder coating machine price
electrostatic powder coating machine products
electrostatic powder coating machine supplier
electrostatic powder coating machine suppliers
electrostatic powder coating machine wx-958
electrostatic powder coating manufacturer
electrostatic powder coating manufacturers
electrostatic powder coating method
electrostatic powder coating paint
electrostatic powder coating pdf
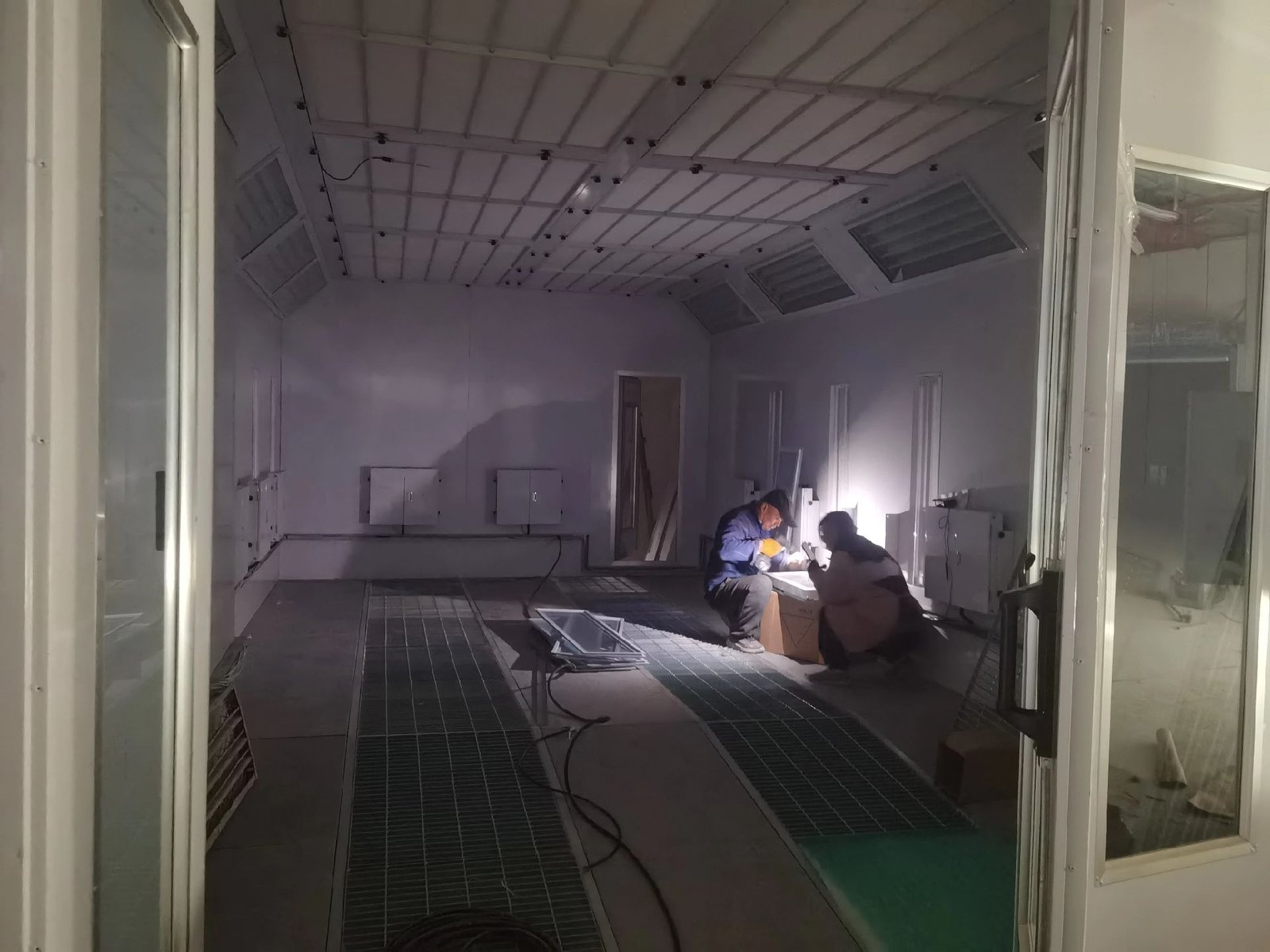