
Electrostatic powder spraying – how to solve the problem of particle accumulation?
Electrostatic powder spraying – how to solve the problem of particle accumulation?
Particle accumulation during electrostatic powder spraying can lead to issues such as uneven coating, clumping, and defects in the final finish. Here are strategies to solve and prevent particle accumulation:
### 1. **Optimize Powder Flow and Fluidization**:
– **Proper Fluidization**: Ensure the powder is well-fluidized in the hopper. Adjust the fluidizing air pressure to achieve a “boiling” effect, which keeps the powder particles evenly suspended.
– **Check Air Supply**: Ensure a consistent and clean air supply to prevent clumping caused by moisture or contaminants in the air.
### 2. **Control Humidity and Temperature**:
– **Maintain Low Humidity**: High humidity can cause powder particles to clump together. Keep the spraying environment below 60% relative humidity.
– **Regulate Temperature**: Ensure the environment and powder are at a suitable temperature (typically 15°C to 30°C) to prevent condensation and maintain optimal powder flow.
### 3. **Adjust Electrostatic Settings**:
– **Optimize Voltage**: High voltage can cause excessive attraction of powder to certain areas, leading to accumulation. Adjust the voltage to achieve a balance that provides good coverage without excessive build-up.
– **Proper Grounding**: Ensure that the parts and equipment are properly grounded. Poor grounding can lead to uneven electrostatic fields and particle accumulation.
### 4. **Gun Position and Movement**:
– **Correct Gun Distance**: Maintain an optimal distance (typically 6-12 inches) between the spray gun and the part. Too close or too far can cause uneven powder distribution and accumulation.
– **Consistent Movement**: Move the spray gun smoothly and evenly to avoid excessive powder build-up in specific areas.
### 5. **Clean and Maintain Equipment**:
– **Regular Cleaning**: Clean the spray gun, nozzles, and hoses regularly to prevent powder build-up, which can contribute to uneven flow and accumulation.
– **Check for Blockages**: Inspect and clear any blockages in the powder delivery system to ensure consistent flow.
### 6. **Use Quality Powder**:
– **Consistent Particle Size**: Use high-quality powder with consistent particle size to ensure even fluidization and application.
– **Proper Storage**: Store powder in a dry, temperature-controlled environment to prevent moisture absorption and clumping.
### 7. **Monitor and Adjust Reclaimed Powder**:
– **Proper Recovery System**: Ensure the powder recovery system is efficient and properly adjusted to prevent contamination and maintain powder quality.
– **Mix with Virgin Powder**: If using reclaimed powder, mix it with fresh powder to maintain consistent quality and prevent accumulation issues.
### 8. **Optimize Air Pressure**:
– **Adjust Spray Air Pressure**: Use the appropriate air pressure settings to achieve a consistent powder flow without overspraying or accumulation.
– **Check for Air Leaks**: Ensure there are no air leaks in the system that could affect the powder delivery and cause uneven application.
By addressing these factors, you can minimize particle accumulation and achieve a smooth, even coating in the electrostatic powder spraying process.
electrostatic vs powder coating
electrostatic wrap powder coat
electrostatic wrap powder coating
electrostatically applied powder coating
electrostatically powder coated
etfe electrostatic powder
gema electrostatic powder coating system
how electrostatic powder coating works
how electrostatic spray painting/powder coating works
how to apply powder coat electrostaticly to wheel rims
how to electrostatic paint with powder coating
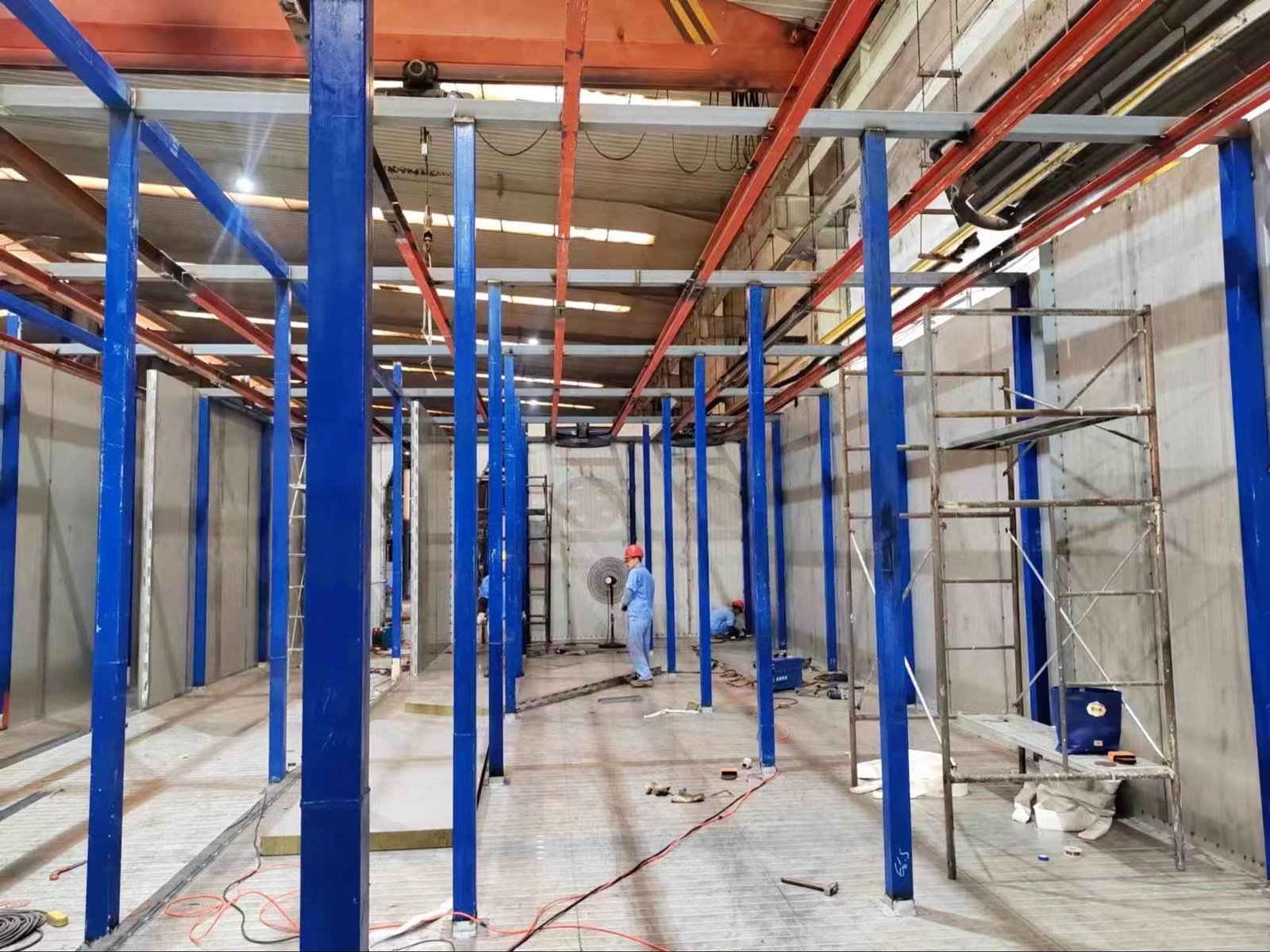