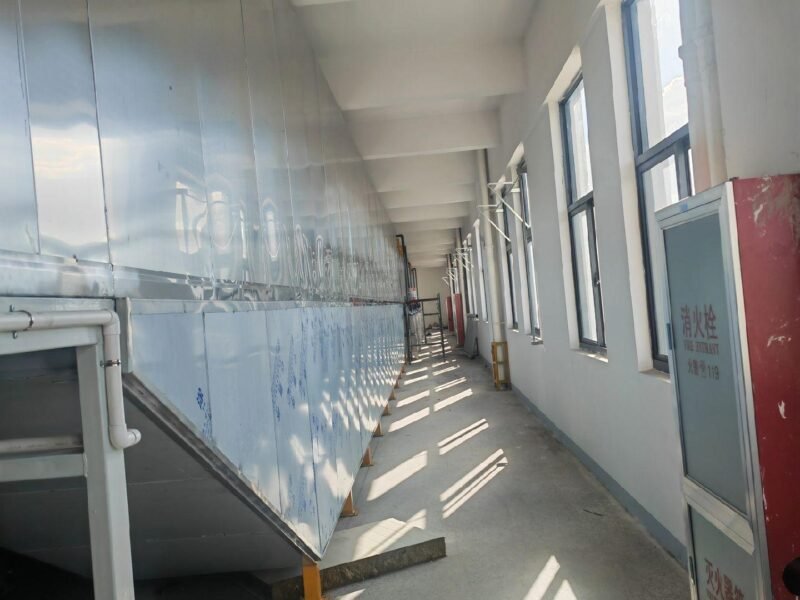
What is the key influence of powder electrostatic spraying equipment coating on spraying quality?
What is the key influence of powder electrostatic spraying equipment coating on spraying quality?
The quality of the coating achieved through powder electrostatic spraying is significantly influenced by various aspects of the spraying equipment. Here are the key factors:
### 1. **Electrostatic Charging System**:
– **Voltage and Current Control**:
– Properly adjusted voltage and current are critical for creating an optimal electrostatic field. This ensures the powder particles are uniformly charged and attracted to the grounded parts, leading to even coating and minimal overspray.
– **Consistent Charge Distribution**:
– Equipment that provides a consistent electrostatic charge helps in achieving uniform powder deposition, especially on complex geometries and edges.
### 2. **Spray Gun Design and Functionality**:
– **Nozzle Design**:
– Different nozzle types (flat, round, etc.) affect the spray pattern and coverage. The correct nozzle ensures even distribution and reduces the risk of overspray or thin spots.
– **Adjustable Settings**:
– Guns with adjustable settings for flow rate, pattern size, and air pressure allow fine-tuning to match the specific part geometry and coating requirements, improving quality and efficiency.
### 3. **Powder Feed System**:
– **Consistent Powder Flow**:
– A well-functioning powder feed system ensures a steady and controlled flow of powder, preventing issues like clumping, surging, or inconsistent coverage.
– **Proper Fluidization**:
– Good fluidization in the hopper ensures that the powder remains evenly distributed and doesn’t settle, which is crucial for consistent spraying.
### 4. **Grounding and Part Positioning**:
– **Effective Grounding**:
– Proper grounding of parts and equipment is essential for creating a strong electrostatic field, ensuring powder particles adhere evenly to the surface.
– **Stable Part Positioning**:
– Properly positioned parts ensure that all areas receive uniform coverage, and reduce the likelihood of missed spots or excess buildup.
### 5. **Automation and Control Systems**:
– **Precision Automation**:
– Automated systems provide consistent and repeatable motion, ensuring uniform coating application across multiple parts or complex geometries.
– **Process Control**:
– Advanced control systems allow real-time monitoring and adjustment of spraying parameters, leading to improved consistency and quality.
### 6. **Powder Recovery System**:
– **Efficient Recovery**:
– A good recovery system minimizes waste and ensures that reclaimed powder maintains its quality, which is crucial for consistent application and cost efficiency.
– **Contamination Control**:
– Proper separation of different powder types and cleanliness in the recovery system prevents contamination that can affect coating quality.
### 7. **Environmental Controls**:
– **Stable Temperature and Humidity**:
– Environmental controls integrated into the equipment help maintain optimal spraying conditions, reducing the risk of defects caused by temperature or humidity fluctuations.
– **Dust and Contamination Control**:
– Ensuring a clean spraying environment prevents dust or other contaminants from affecting the coating finish.
### 8. **Curing Oven Performance**:
– **Uniform Heating**:
– A well-calibrated curing oven with consistent temperature distribution ensures the powder coating cures evenly, avoiding defects like under-curing or over-curing that can affect adhesion and durability.
– **Proper Temperature Control**:
– Accurate temperature control tailored to the specific powder formulation is crucial for achieving the desired coating properties.
### 9. **Maintenance and Calibration**:
– **Regular Maintenance**:
– Regular maintenance of the equipment ensures that all components are functioning optimally, preventing issues like inconsistent flow or electrical problems.
– **Calibration**:
– Periodic calibration of equipment settings ensures that the spraying parameters remain within the optimal range for high-quality coating results.
By focusing on these key aspects of the powder electrostatic spraying equipment, the overall spraying quality can be significantly enhanced, resulting in smooth, uniform, and durable coatings.
electrostatic adhesion powder
electrostatic charge powder
electrostatic coating powder
electrostatic coating vs powder coating
electrostatic dissipative powder coatings
electrostatic drum powder paint process
electrostatic dry powder coating
electrostatic enamel powder
electrostatic enamel powder coating
electrostatic fluidization bed for powder coating
electrostatic fluidization bed for powder coating machine
