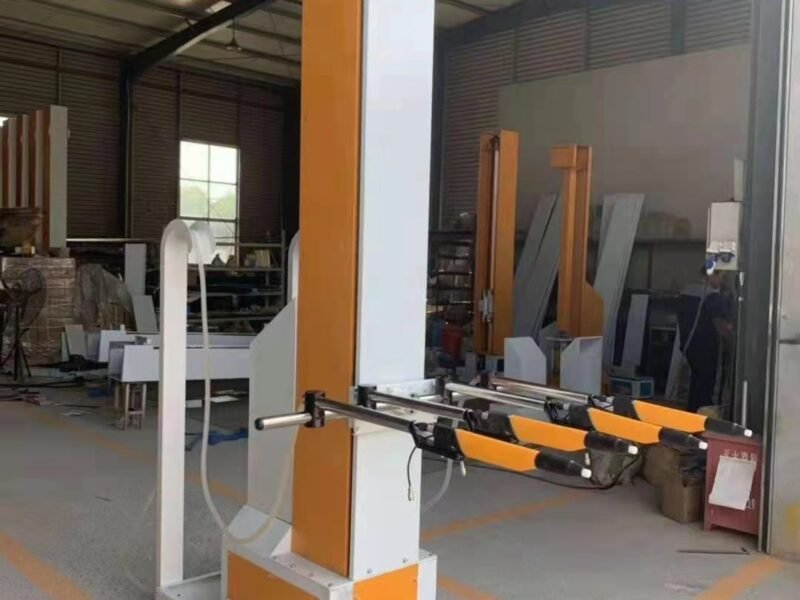
Do you know what the requirements are for electrostatic spraying?
Do you know what the requirements are for electrostatic spraying?
Electrostatic spraying requires adherence to several key requirements to ensure a high-quality, efficient, and safe coating process. Here are the main requirements:
### 1. **Proper Surface Preparation**:
– **Cleaning**:
– The surface must be thoroughly cleaned to remove dirt, grease, oil, and other contaminants that can affect adhesion.
– **Pre-Treatment**:
– Depending on the material, pre-treatment processes like phosphating, chromating, or sandblasting may be required to improve adhesion and corrosion resistance.
### 2. **Controlled Environment**:
– **Temperature and Humidity**:
– The spraying environment should be controlled for temperature (usually between 15°C and 30°C) and humidity (below 60%) to prevent powder clumping and ensure proper adhesion.
– **Ventilation**:
– Adequate ventilation is necessary to remove excess powder particles and prevent the buildup of flammable or hazardous dust.
### 3. **Quality Powder Coating**:
– **Powder Selection**:
– Use high-quality powder coatings suitable for the intended application, ensuring they meet the specific requirements for durability, appearance, and performance.
– **Proper Storage**:
– Store powders in a cool, dry place to maintain their quality and prevent moisture absorption.
### 4. **Electrostatic Spraying Equipment**:
– **Proper Calibration**:
– Equipment should be correctly calibrated for voltage, powder flow rate, and air pressure to ensure consistent coating thickness and quality.
– **Maintenance**:
– Regular maintenance of the spray gun, powder feed system, and recovery system is essential to prevent clogs and ensure smooth operation.
### 5. **Grounding and Safety**:
– **Proper Grounding**:
– Both the parts being coated and the equipment must be properly grounded to ensure effective electrostatic charging and reduce the risk of electric shock.
– **Safety Measures**:
– Implement fire and explosion prevention measures, such as using non-sparking tools and ensuring the spray booth and recovery system meet safety standards.
### 6. **Uniform Application**:
– **Consistent Coating**:
– Ensure the spray gun is held at the correct distance (typically 6-12 inches) and moved evenly across the surface to achieve uniform coverage and avoid defects like sagging or thin spots.
– **Proper Gun Settings**:
– Adjust the gun settings to match the specific powder and part geometry, taking into account factors like the Faraday cage effect for complex shapes.
### 7. **Curing Process**:
– **Curing Oven**:
– The coated parts should be cured in a properly calibrated oven at the specified temperature and duration to ensure complete curing and optimal film properties.
– **Consistent Temperature**:
– Maintain a consistent temperature throughout the oven to prevent uneven curing, which can affect the coating’s appearance and performance.
### 8. **Quality Control**:
– **Inspection**:
– Perform regular inspections for coating defects, such as pinholes, orange peel, or color inconsistencies.
– **Testing**:
– Conduct adhesion tests, thickness measurements, and other quality control tests to ensure the coating meets the required standards.
### 9. **Environmental and Regulatory Compliance**:
– **VOC and Emissions Control**:
– Ensure compliance with environmental regulations regarding VOC emissions and waste disposal.
– **Worker Safety**:
– Provide appropriate personal protective equipment (PPE) for workers, including masks, gloves, and protective clothing.
By meeting these requirements, the electrostatic spraying process can achieve high-quality, durable coatings while maintaining safety and efficiency.
electrostatic powder coatings definition
electrostatic powder combustible dust k value
electrostatic powder cooating system
electrostatic powder fluid bed for powder coating hopper
electrostatic powder inc
electrostatic powder k values
electrostatic powder line
electrostatic powder paint suppliers
electrostatic powder painting equipment company
electrostatic powder painting equipment manufacturer
electrostatic powder painting equipment products
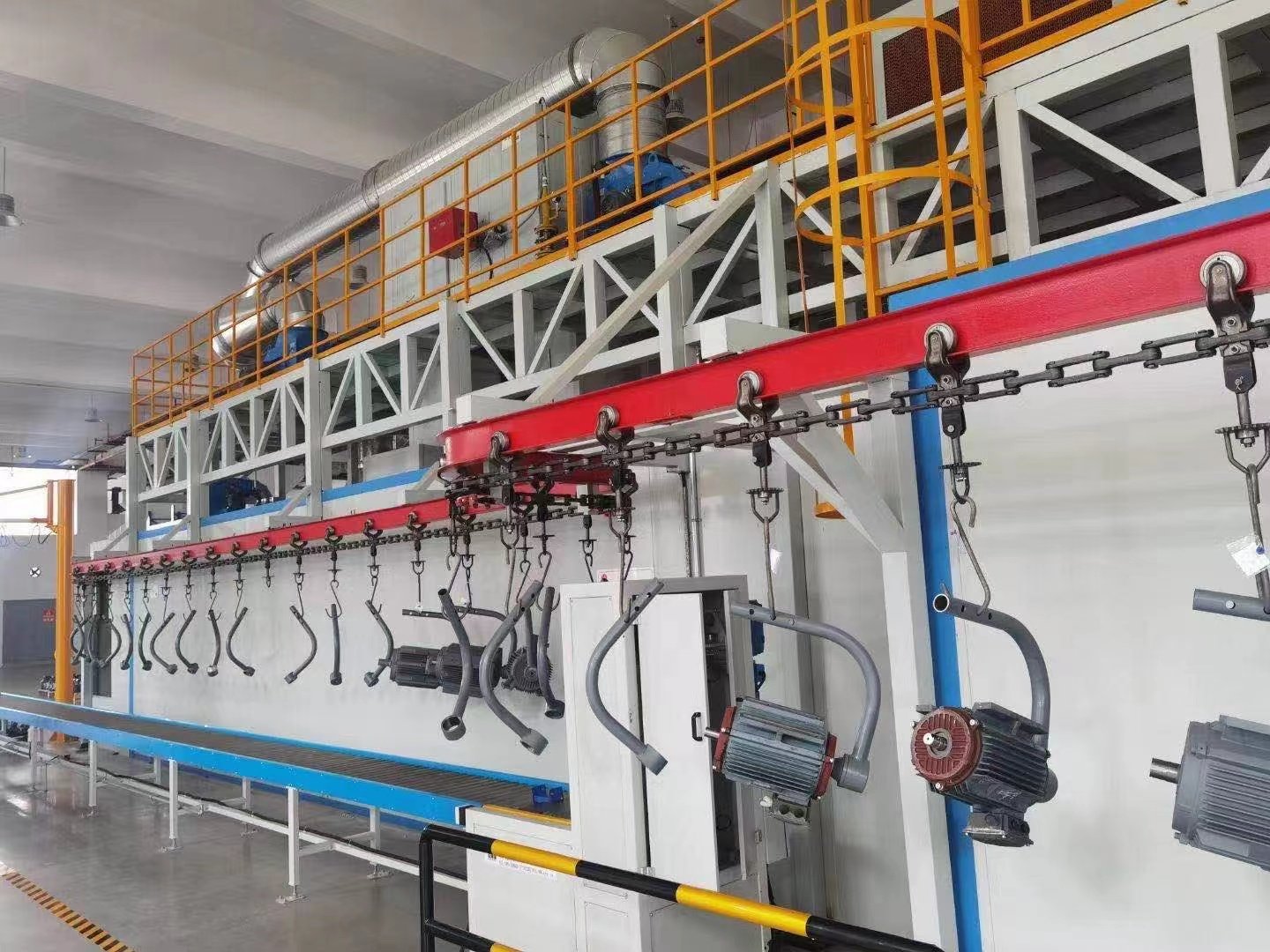