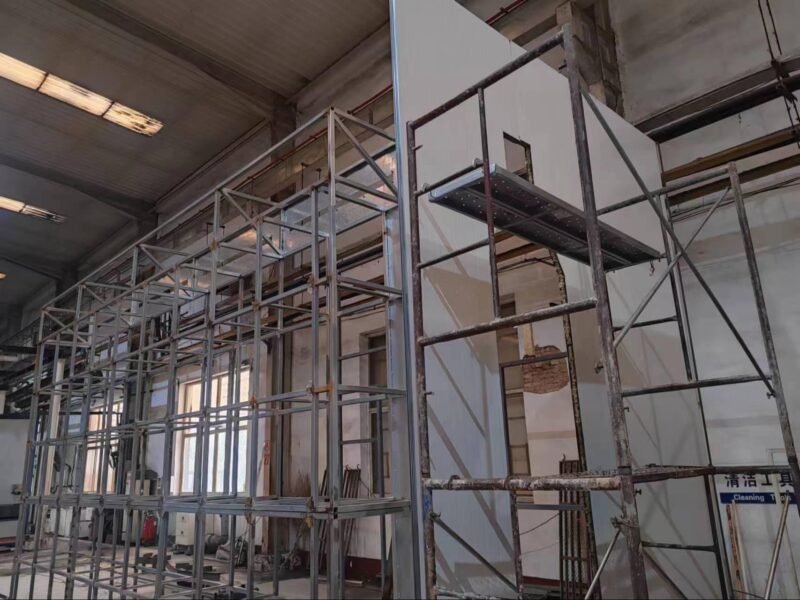
Electrostatic Powder Spraying Risk Identification
Electrostatic Powder Spraying Risk Identification
Electrostatic powder spraying, while widely used for its efficiency and durability, carries several risks associated with the process, equipment, and materials. Identifying these risks is crucial to ensure safety and prevent accidents, equipment damage, or compromised product quality. Below are key risk areas associated with electrostatic powder spraying, along with the measures that can be taken to mitigate them.
### **1. Fire and Explosion Risks**
Electrostatic powder spraying involves the use of fine powder particles, which can become suspended in the air. Under the right conditions, these particles can become explosive, especially in enclosed areas.
#### **Risk Factors**:
– **Flammable Powder**: Powder coating materials (especially organic powders) can be flammable, and an airborne concentration of these particles can ignite if exposed to sparks or heat.
– **Electrostatic Discharge (ESD)**: Poor grounding or incorrect handling of equipment can cause electrostatic sparks, which may ignite the powder cloud.
– **Accumulation of Powder**: Excessive accumulation of powder in spray booths, equipment, or ducts can increase the risk of explosion.
#### **Mitigation Measures**:
– **Proper Ventilation**: Ensure adequate ventilation in the spray booth and working area to prevent the buildup of airborne powder.
– **Grounding and Bonding**: Ensure that all equipment and the substrate are properly grounded to prevent static discharge.
– **Explosion-Proof Equipment**: Use explosion-proof motors, fans, and electrical systems in powder coating areas to minimize ignition sources.
– **Regular Cleaning**: Clean booths, equipment, and recovery systems regularly to prevent powder accumulation.
—
### **2. Respiratory and Health Hazards**
Powder particles, if inhaled, can pose serious respiratory risks to operators. Although powder coatings generally have fewer health risks than solvent-based coatings, they can still cause irritation or sensitization.
#### **Risk Factors**:
– **Inhalation of Powder**: Inhalation of fine powder particles can lead to respiratory issues, especially if the powder contains hazardous materials such as isocyanates or heavy metals.
– **Skin and Eye Irritation**: Prolonged exposure to certain powder coating materials may cause skin irritation or eye discomfort.
– **Allergic Reactions**: Some powders contain chemicals that can trigger allergic reactions or sensitization over time.
#### **Mitigation Measures**:
– **Personal Protective Equipment (PPE)**: Operators should wear masks or respirators, safety goggles, and protective clothing to avoid inhalation or contact with the powder.
– **Powder Handling Precautions**: Ensure that powders are handled in a well-ventilated area, and avoid unnecessary exposure.
– **Safe Material Selection**: Use powders that comply with local safety and environmental regulations, avoiding hazardous or toxic materials whenever possible.
– **Training**: Provide thorough training on the correct use of PPE and the safe handling of powder materials.
—
### **3. Electrical Risks**
Electrostatic powder spraying requires high-voltage equipment to charge powder particles. If this equipment is improperly maintained or handled, it can pose electrical risks to operators and equipment.
#### **Risk Factors**:
– **Electrocution**: Direct contact with high-voltage parts of the spray gun or control units can cause electric shock or electrocution.
– **Faulty Grounding**: Inadequate grounding can result in unintentional arcing, causing electric shock or equipment damage.
– **Equipment Failure**: Faulty or poorly maintained electrical equipment can lead to malfunction, increasing the risk of fire or accidents.
#### **Mitigation Measures**:
– **Regular Maintenance**: Regularly inspect and maintain all electrical equipment, including spray guns, control units, and grounding connections.
– **Insulation and Shielding**: Ensure that electrical components are properly insulated and shielded to prevent operator contact.
– **Use of Proper Grounding Techniques**: Always ground both the substrate and the equipment to avoid static buildup and potential discharge.
– **Lockout/Tagout (LOTO)**: Implement proper LOTO procedures during maintenance or repair work to avoid accidental electrocution.
—
### **4. Mechanical Risks**
The equipment used in electrostatic powder spraying, such as conveyor systems, spray booths, and curing ovens, presents mechanical hazards.
#### **Risk Factors**:
– **Moving Parts**: Conveyor belts, robotic arms, and rotating parts of the spray booth can cause injury if not properly guarded.
– **Pinch Points**: Moving parts may create pinch points that can lead to operator injury.
– **Equipment Failure**: Malfunctioning spray guns, booths, or ovens can lead to part failures, which may result in injuries or production delays.
#### **Mitigation Measures**:
– **Guarding and Shields**: Use safety guards and shields to prevent accidental contact with moving parts.
– **Emergency Stop Systems**: Equip machinery with emergency stop mechanisms that can quickly shut down the system in case of malfunction.
– **Regular Inspection**: Inspect conveyor systems, ovens, and other equipment for wear and tear, ensuring that all moving parts function safely.
– **Operator Training**: Train operators on safe equipment usage and handling, focusing on avoiding pinch points and other mechanical risks.
—
### **5. Overheating and Thermal Risks**
During the curing phase of powder coating, parts are heated to high temperatures, which can pose thermal hazards.
#### **Risk Factors**:
– **Burns**: Operators may accidentally come into contact with hot surfaces or parts, resulting in burns.
– **Overheating**: Excessive temperatures during the curing process can damage equipment or the coated part, posing risks of fire or material failure.
#### **Mitigation Measures**:
– **Proper Insulation**: Ensure that curing ovens and hot surfaces are properly insulated to protect operators.
– **Temperature Control Systems**: Use precise temperature control systems to prevent overheating in curing ovens.
– **Personal Protection**: Provide operators with heat-resistant gloves and other protective gear when handling hot parts or equipment.
—
### **6. Environmental Risks**
Electrostatic powder spraying can generate waste, pollutants, and other environmental concerns if not properly controlled.
#### **Risk Factors**:
– **Powder Waste**: Excessive overspray and improper powder recovery can result in large amounts of powder waste, which may be costly and harmful to the environment.
– **Airborne Particles**: Fine powder particles released into the atmosphere can contribute to air pollution and affect the surrounding environment.
– **Energy Consumption**: High-energy use, especially during the curing process, can have a significant environmental footprint.
#### **Mitigation Measures**:
– **Powder Recovery Systems**: Use efficient powder recovery systems such as cyclone or cartridge filters to reclaim and reuse overspray, minimizing waste.
– **Emission Control**: Ensure that powder booths are equipped with adequate filtration and ventilation to reduce airborne particles.
– **Energy Efficiency**: Use energy-efficient ovens and equipment to reduce energy consumption and lower environmental impact.
– **Compliance with Regulations**: Adhere to local environmental regulations to ensure safe disposal of waste and emissions control.
—
### **7. Product Quality Risks**
Compromised product quality can result from various factors during electrostatic powder spraying.
#### **Risk Factors**:
– **Uneven Coating**: Improper spraying techniques or equipment malfunction can result in uneven powder application, leading to defects such as orange peel, pinholes, or poor adhesion.
– **Curing Defects**: Incorrect curing temperatures or times can result in undercured or overcured coatings, reducing durability and appearance.
– **Contamination**: Contaminants such as dust or moisture can affect the final finish, leading to coating defects.
#### **Mitigation Measures**:
– **Operator Training**: Provide adequate training on spraying techniques to ensure even coating and correct operation of equipment.
– **Regular Equipment Calibration**: Calibrate spray guns and curing ovens regularly to ensure consistent performance.
– **Controlled Environment**: Maintain a clean, temperature- and humidity-controlled environment to prevent contamination during spraying.
—
### **Conclusion:**
Electrostatic powder spraying presents several risks, including fire and explosion hazards, respiratory and health issues, electrical hazards, mechanical injuries, thermal risks, environmental concerns, and potential product quality defects. Effective risk identification, proper equipment maintenance, operator training, and adherence to safety regulations are essential in mitigating these risks and ensuring a safe, efficient, and high-quality powder coating process.
electrostatic powder coating manufacturers
electrostatic powder coating method
electrostatic powder coating paint
electrostatic powder coating pdf
electrostatic powder coating plant
electrostatic powder coating principle
electrostatic powder coating principles and pharmaceutical applications
electrostatic powder coating problems
electrostatic powder coating process pdf
electrostatic powder coating ptfe
electrostatic powder coating services
