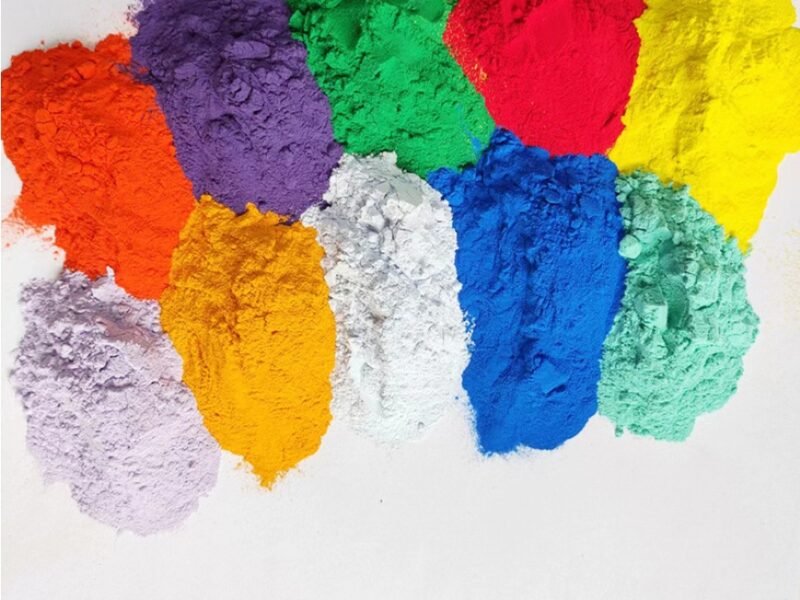
How to calculate the cost of powder electrostatic spraying?
How to calculate the cost of powder electrostatic spraying?
Calculating the **cost of powder electrostatic spraying** involves accounting for various factors, including material usage, labor, equipment costs, energy consumption, and overhead. Here’s a step-by-step guide to estimating the cost:
—
### **1. Material Costs**
– **Powder Coating Price:**
– Determine the cost per kilogram of the powder coating material. For example, powder may cost $8–$20 per kg, depending on the type and quality.
– **Coating Thickness:**
– Specify the desired thickness (in microns) for the coating. Common ranges are 60–120 microns.
– **Coverage Rate:**
– Calculate the area covered per kilogram of powder, based on the material’s **specific gravity** and desired thickness. Use the formula:
\[
\text{Coverage (m²/kg)} = \frac{1000}{\text{Specific Gravity} \times \text{Coating Thickness (microns)}}
\]
– Example: For a powder with a specific gravity of 1.5 and a coating thickness of 80 microns:
\[
\text{Coverage} = \frac{1000}{1.5 \times 80} = 8.33 \, \text{m²/kg}
\]
– **Material Waste:**
– Factor in material recovery efficiency (e.g., 95–98% for reclaimable powders). Multiply the coverage area by the efficiency rate.
—
### **2. Labor Costs**
– Determine the labor cost per hour, including wages, benefits, and overhead.
– Estimate the time required for spraying and curing:
– Pre-treatment (cleaning, preparation): Time depends on the complexity of the workpiece.
– Spraying: Calculate time based on the size and complexity of the object.
– Curing: Account for time spent in the curing oven.
– Example: If labor costs $25/hour and the total time for spraying and curing a part is 1.5 hours:
\[
\text{Labor Cost} = 25 \times 1.5 = 37.50
\]
—
### **3. Equipment Costs**
– **Depreciation:**
Divide the cost of equipment (e.g., spray guns, booths, ovens) over its expected lifespan to determine hourly or per-use costs.
– **Maintenance:**
Add maintenance costs, including cleaning, part replacement, and service fees.
—
### **4. Energy Costs**
– **Electricity:**
– Estimate energy consumption for the spray booth, powder application equipment, and curing oven.
– Example: If the curing oven uses 10 kW per hour, and the electricity cost is $0.12 per kWh, curing for 30 minutes costs:
\[
\text{Energy Cost} = 10 \times 0.12 \times 0.5 = 0.60
\]
– **Compressed Air:**
– Include the cost of operating the air compressor for the spray gun.
—
### **5. Pre-Treatment Costs**
– Factor in costs for chemicals (e.g., degreasers, phosphates), water usage, and disposal of waste from cleaning processes.
– Example: If chemical pre-treatment costs $5 per workpiece, include this in the calculation.
—
### **6. Overhead Costs**
– Include facility costs such as rent, utilities, and administrative expenses.
– Allocate overhead per job or per hour based on facility utilization.
—
### **7. Total Cost Calculation**
Combine all the costs calculated above:
\[
\text{Total Cost} = \text{Material Cost} + \text{Labor Cost} + \text{Equipment Cost} + \text{Energy Cost} + \text{Pre-Treatment Cost} + \text{Overhead Cost}
\]
—
### **Example Calculation**
Suppose you are coating a metal part with these parameters:
– Part size: 2 m²
– Powder cost: $10/kg
– Specific gravity: 1.4
– Coating thickness: 80 microns
– Recovery efficiency: 95%
– Labor cost: $30/hour (1 hour total)
– Energy cost: $1.50 for curing
– Equipment depreciation: $2 per use
– Pre-treatment cost: $5 per piece
– Overhead allocation: $10
1. **Material Cost:**
\[
\text{Coverage} = \frac{1000}{1.4 \times 80} = 8.93 \, \text{m²/kg}
\]
\[
\text{Powder Used} = \frac{2}{8.93 \times 0.95} = 0.24 \, \text{kg}
\]
\[
\text{Material Cost} = 0.24 \times 10 = 2.40
\]
2. **Labor Cost:**
\[
30 \times 1 = 30
\]
3. **Energy Cost:**
\[
1.50
\]
4. **Equipment Cost:**
\[
2
\]
5. **Pre-Treatment Cost:**
\[
5
\]
6. **Overhead Cost:**
\[
10
\]
**Total Cost:**
\[
2.40 + 30 + 1.50 + 2 + 5 + 10 = 50.90
\]
The total cost to coat the 2 m² part would be approximately **$50.90**.
—
### **Tips for Cost Optimization**
– Use reclaim systems to reduce material waste.
– Train operators for efficient spraying and reduced rework.
– Optimize curing oven schedules to minimize energy consumption.
– Purchase powder coatings in bulk to lower material costs.
By following this method, you can accurately calculate and optimize the cost of powder electrostatic spraying.
electrostatic powder coating voltage
electrostatic powder coating vs powder coating
electrostatic powder coating wikipedia
electrostatic powder coating without baking
electrostatic powder coating without making
electrostatic powder coatings
electrostatic powder coatings definition
electrostatic powder combustible dust k value
electrostatic powder cooating system
electrostatic powder fluid bed for powder coating hopper
electrostatic powder inc
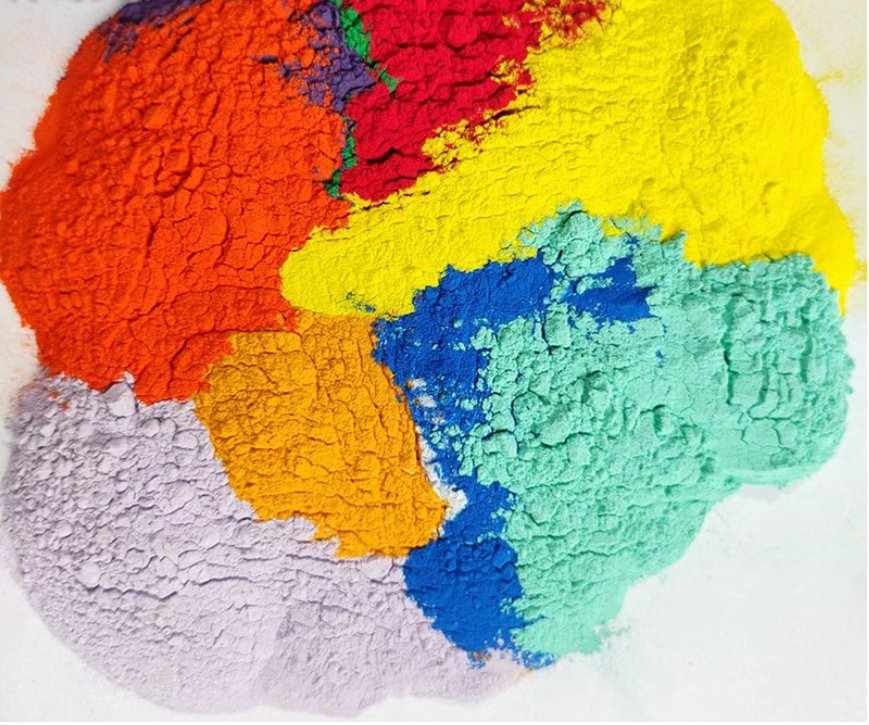