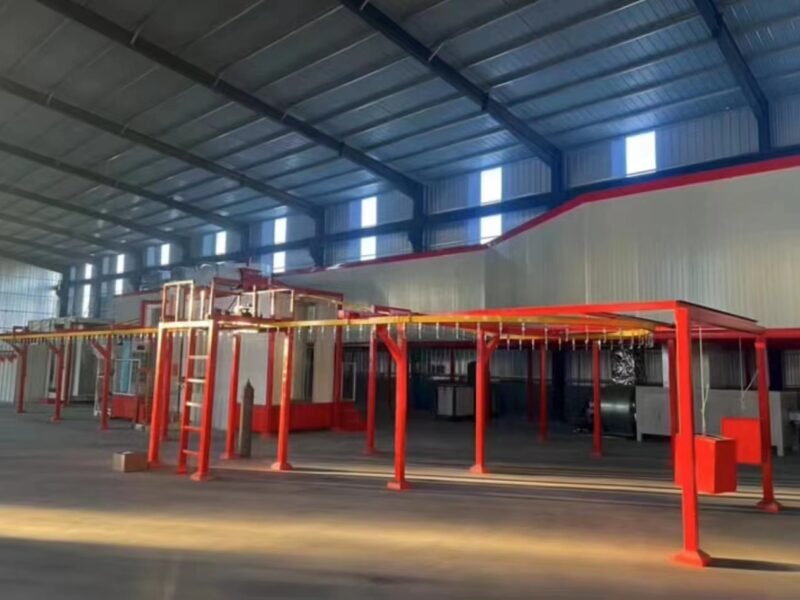
How to choose powder for electrostatic powder spraying
How to choose powder for electrostatic powder spraying
Choosing the right **powder** for **electrostatic powder spraying** (also known as **powder coating**) is crucial for achieving the desired finish and performance for the coated surface. The choice of powder depends on several factors, including the material you’re coating, the intended use of the item, and environmental considerations. Here’s a guide on how to choose the right powder:
### 1. **Type of Powder Coating**
Powder coatings are made from a combination of resin, hardener, pigments, and additives, and they come in various formulations. The most common types of powder coatings are:
– **Epoxy Powder Coatings**:
– **Best for**: Indoor applications, as they offer excellent adhesion, chemical resistance, and a smooth finish.
– **Pros**: Durable, good corrosion resistance, excellent adhesion.
– **Cons**: Poor UV resistance, so not ideal for outdoor or direct sunlight exposure.
– **Polyester Powder Coatings**:
– **Best for**: Outdoor applications due to better UV resistance and color retention.
– **Pros**: Good outdoor weathering, better UV stability than epoxy, highly durable.
– **Cons**: Not as chemically resistant as epoxy, but performs well in most environments.
– **Hybrid (Epoxy-Polyester Blend)**:
– **Best for**: General-purpose coatings that require a balance between indoor and outdoor durability.
– **Pros**: Offers a compromise between the strong corrosion resistance of epoxy and the UV resistance of polyester.
– **Cons**: Somewhat less durable than pure epoxy or polyester in extreme conditions.
– **Polyurethane Powder Coatings**:
– **Best for**: Highly durable, heavy-duty industrial applications, including automotive and heavy machinery.
– **Pros**: Excellent chemical resistance, hardness, and durability.
– **Cons**: Can be more expensive, and may require special curing processes.
– **Fluoropolymer Powder Coatings (e.g., PTFE)**:
– **Best for**: Extremely harsh environments (e.g., highly corrosive conditions) or for special functional coatings like non-stick surfaces.
– **Pros**: Excellent chemical and heat resistance.
– **Cons**: Expensive, less commonly used for general applications.
### 2. **Finish Type**
The finish you choose for the coating will impact the appearance and functionality of the coated surface. Powder coatings come in several finish types:
– **Gloss**: Offers a shiny, reflective surface. Ideal for smooth and sleek finishes.
– **Matte**: Offers a non-reflective finish that is commonly used for modern or industrial looks.
– **Satin**: A middle ground between gloss and matte, providing a subtle sheen.
– **Textured**: Provides a rough or pebbled texture, often used for decorative or slip-resistant finishes.
– **Wrinkle**: Gives a wrinkled texture, used for specific aesthetic or functional requirements.
### 3. **Color and Appearance**
– **Color Selection**: Choose a color that meets the design or branding needs of the project. Powder coatings come in almost any color, and manufacturers offer custom colors, though this may increase cost.
– **Special Effects**: Some powders include metallic flakes, pearlescent finishes, or other unique effects. These powders can create visually striking finishes, but may require more precise application techniques.
### 4. **Application Environment**
– **Indoor vs. Outdoor Use**:
– **Indoor**: If the coated item will be used indoors or in controlled environments (e.g., furniture, appliances), epoxy or hybrid powders are usually suitable.
– **Outdoor**: For outdoor use, especially in direct sunlight or harsh weather conditions, **polyester** or **polyurethane** powders are preferred for their UV resistance and color retention.
– **Exposure to Harsh Conditions**: If the item will be exposed to harsh chemicals, moisture, or extreme temperatures (e.g., automotive parts, machinery), choose a **polyurethane** or **epoxy-polyester** blend for superior durability.
### 5. **Durability and Performance Requirements**
– **Chemical Resistance**: If the coated object needs to withstand chemicals, oils, or solvents (e.g., industrial machinery), go for **epoxy** or **polyurethane** powders, which provide good chemical resistance.
– **Abrasion and Scratch Resistance**: For applications where high wear resistance is required (e.g., automotive parts or outdoor equipment), **polyurethane** or **epoxy-polyester blend** coatings are ideal.
– **Corrosion Resistance**: **Epoxy powders** are excellent for corrosion resistance, making them a good choice for metal coatings that will be exposed to moisture (e.g., pipes, outdoor furniture).
– **Temperature Resistance**: If the coated surface will be exposed to extreme temperatures (e.g., oven parts, engine components), choose a powder that is specifically formulated for **high-temperature resistance** (e.g., **high-temperature polyester** or **epoxy**).
### 6. **Curing Requirements**
Different powder coatings may have different curing temperatures and times. Be sure the powder you choose is compatible with your curing oven and process.
– **Standard Curing**: Most powder coatings cure at **350–400°F (175–205°C)** for **10–20 minutes**, but this can vary by formulation.
– **Low-Temperature Curing**: Some powders are formulated to cure at lower temperatures (e.g., **250–300°F / 120–150°C**), which can be useful for heat-sensitive materials.
### 7. **Environmental and Health Considerations**
– **VOC-Free**: Powder coatings are typically low in volatile organic compounds (VOCs), making them a more environmentally friendly option compared to liquid paints. Always verify that the powder meets local environmental regulations.
– **Health Safety**: Ensure that proper safety equipment, such as respirators and ventilation, is used during application, especially when handling powders that could be hazardous when inhaled.
### 8. **Application Method**
– **Electrostatic Charge Compatibility**: The powder must be compatible with the electrostatic spraying process. Ensure that the powder you select is formulated for electrostatic application, as some formulations may not be optimized for that process.
### 9. **Cost Considerations**
– **Material Costs**: Premium powder coatings, such as metallic or custom colors, can be more expensive. Make sure to balance the performance requirements with your budget.
– **Operational Costs**: Some powder types may require specific curing times or conditions, which can affect energy consumption and the overall cost of the application process.
### Summary of Key Points:
– **Epoxy**: Best for indoor use, corrosion resistance.
– **Polyester**: Best for outdoor use, UV resistance, and color retention.
– **Hybrid**: Balanced properties for both indoor and outdoor.
– **Polyurethane**: Best for heavy-duty, industrial use with high chemical and abrasion resistance.
– **Fluoropolymer**: Best for extreme environments, such as highly corrosive conditions.
By carefully evaluating the application needs (e.g., environment, durability, aesthetic preferences), you can choose the right type of powder coating for your project. If in doubt, consult with a supplier who can help match the powder type to your requirements.
how does electrostatic powder coating work
powder coat electrostatic
powder coating electrostatic
powder coating electrostatic charge
ryobi electrostatic sprayer powder coating
what is electrostatic powder coating
electrostatic magic powder coating
electrostatic paint vs powder coating
electrostatic powder coating machine factory
electrostatic powder coating spray gun
electrostatic powder coating suppliers
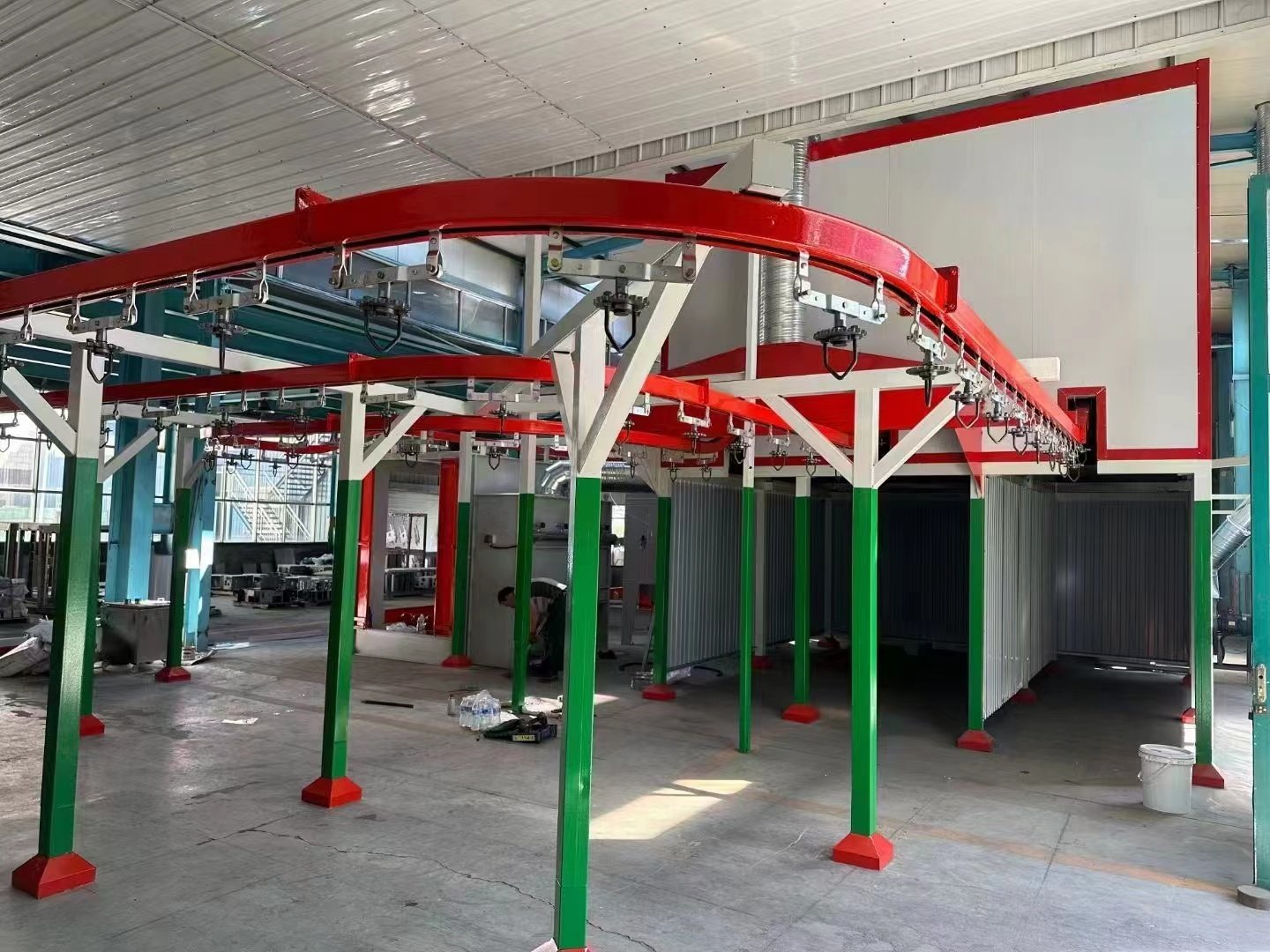