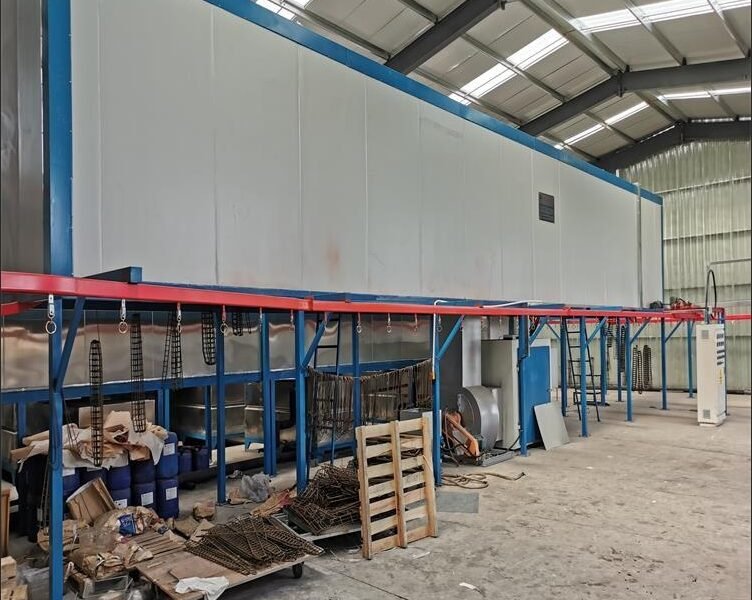
How to choose suitable electrostatic spraying powder?
How to choose suitable electrostatic spraying powder?
When choosing a **suitable electrostatic spraying powder** (also known as **powder coating**) for a project, the selection process depends on several factors that determine the final performance, appearance, and durability of the coated surface. Here’s a comprehensive guide on how to select the right powder for electrostatic spraying:
### 1. **Consider the Substrate (Material Being Coated)**
The material you’re coating will significantly influence the type of powder you should choose:
– **Metal (Steel, Aluminum, etc.)**: Powders designed for metal substrates, especially **epoxy** or **polyester** powders, are commonly used. For aluminum, special powders that prevent outgassing and ensure smooth finish should be considered.
– **Plastic**: Some powders are formulated specifically for plastic substrates, requiring lower curing temperatures and careful bonding agents.
– **Other Materials**: For non-metal materials (e.g., wood, glass, ceramics), make sure to use powders designed to bond effectively with those surfaces, as powders designed for metal might not perform well.
### 2. **Powder Type: Select the Right Formula**
Different powder formulations are tailored for specific performance needs. The most common types include:
– **Epoxy Powder Coatings**:
– **Best for**: Indoor applications or environments with moderate wear and moisture exposure (e.g., appliances, furniture, automotive parts).
– **Pros**: Excellent adhesion, corrosion resistance, and smooth finish.
– **Cons**: Poor UV resistance; not suitable for outdoor applications.
– **Polyester Powder Coatings**:
– **Best for**: Outdoor applications exposed to UV light, weathering, and environmental conditions (e.g., exterior architectural parts, garden furniture, outdoor signs).
– **Pros**: Superior UV resistance, color retention, and weatherability.
– **Cons**: Less resistant to harsh chemicals than epoxy.
– **Hybrid (Epoxy-Polyester Blend) Powder Coatings**:
– **Best for**: General-purpose applications that need a balance between corrosion resistance and outdoor durability.
– **Pros**: A compromise between the benefits of epoxy and polyester.
– **Cons**: Not as high-performing in extreme conditions as pure epoxy or polyester.
– **Polyurethane Powder Coatings**:
– **Best for**: Industrial, automotive, or heavy-duty applications where enhanced chemical resistance, abrasion resistance, and durability are required.
– **Pros**: Exceptional hardness, chemical resistance, and durability.
– **Cons**: Typically more expensive, and curing may require more precise conditions.
– **Fluoropolymer (e.g., PTFE)**:
– **Best for**: Extremely harsh environments, including non-stick surfaces, high heat, and chemical exposure.
– **Pros**: Excellent chemical and heat resistance, low friction properties.
– **Cons**: Expensive and used only in specialized applications.
### 3. **Finish Type and Aesthetics**
Powder coatings offer a variety of finishes. Consider the desired appearance of the final product:
– **Glossy**: Provides a shiny and reflective finish, suitable for modern, clean looks (e.g., automotive parts, appliances).
– **Matte**: A non-reflective finish that’s often used for industrial or modern designs (e.g., architectural finishes, office furniture).
– **Satin**: A smooth, soft sheen that’s often used for a sophisticated or semi-durable look (e.g., custom furniture or decorative parts).
– **Textured**: Adds a rough or pebbled texture, useful for functional purposes (e.g., anti-slip surfaces, heavy-duty machinery).
– **Wrinkle**: Provides a wrinkled or hammered finish, often used for aesthetic reasons or to mask imperfections.
### 4. **Durability and Performance Requirements**
Think about the specific conditions the coated surface will face:
– **Chemical Resistance**: If the item will be exposed to chemicals, oils, or solvents (e.g., automotive, industrial), choose **polyurethane** or **epoxy** powders.
– **Corrosion Resistance**: For environments with high humidity or exposure to water (e.g., outdoor equipment, marine applications), **epoxy** or **polyester** powders are ideal.
– **Abrasion Resistance**: For parts that will undergo heavy use or wear (e.g., industrial machinery, automotive), go with **polyurethane** powder coatings.
– **Heat Resistance**: If the surface will experience high temperatures (e.g., ovens, engine parts), use high-temperature powders that can withstand up to **500°F (260°C)** or more.
### 5. **Environmental Exposure**
Consider where the coated object will be used:
– **Indoor Use**: **Epoxy** coatings are ideal for indoor applications where exposure to sunlight or harsh weather conditions is minimal.
– **Outdoor Use**: **Polyester** or **polyurethane** coatings provide better UV stability, weather resistance, and color retention.
– **Extreme Conditions**: For harsh environments (e.g., chemical plants, marine conditions), look for **fluoropolymer** or **polyurethane** coatings that can handle extreme chemicals, heat, and UV radiation.
### 6. **Color and Appearance**
– **Color**: Powder coatings come in almost any color, so choose a color that fits the design or branding needs of the product. Custom colors are often available, but they can increase cost and lead time.
– **Special Effects**: Some powders are designed to create effects like metallic finishes, pearlescent effects, or other unique textures. If you need a high-end finish, look for **metallic** or **pearlescent** powders, but be aware that they can be more challenging to apply and more expensive.
### 7. **Curing and Processing Conditions**
Powder coatings require curing in a **dry heat oven** to harden and adhere to the substrate. Be sure the powder selected is compatible with your curing equipment and process:
– **Curing Temperature**: Most powder coatings cure at around **350-400°F (175-205°C)** for **10-20 minutes**, but some powders cure at lower or higher temperatures. Ensure the powder can handle your oven’s capabilities.
– **Low Temperature Curing**: Some powders are designed for **low-temperature curing** (e.g., **250–300°F / 120–150°C**), which may be useful if you’re working with heat-sensitive substrates or want to save energy.
### 8. **Application Efficiency and Waste**
Consider the efficiency of the coating process, including material waste and the ability to reclaim excess powder:
– **Electrostatic Efficiency**: Make sure the powder is designed for electrostatic spraying, as some powders are optimized for better charge attraction and material savings.
– **Powder Recovery**: **Polyester** and **epoxy-polyester blends** tend to be more efficient in terms of reusing unused powder, while specialty powders (e.g., metallics) may be harder to reclaim without a more advanced system.
### 9. **Cost Considerations**
– **Material Cost**: High-performance powders such as **polyurethane** or **fluoropolymer** will generally cost more than **epoxy** or **polyester** powders.
– **Production Volume**: For high-volume production, you may want to consider powders that are both affordable and efficient to apply (e.g., **hybrid powders** for general-purpose applications).
– **Custom Effects**: Metallic or specialty powders (e.g., textured, pearlescent) may come with higher costs due to the added processing difficulty and material complexity.
### 10. **Health and Environmental Considerations**
– **Low-VOC**: Powder coatings are generally more environmentally friendly than liquid paints because they have little to no volatile organic compounds (VOCs).
– **Safety**: Ensure proper ventilation and protective gear (e.g., respirators, gloves) when applying powder coatings, as they can release dust that may be harmful if inhaled.
### Final Decision Factors:
– **Application Use**: Indoor vs. outdoor, exposure to elements, chemicals, or wear.
– **Performance Needs**: Durability, resistance to abrasion, corrosion, or UV light.
– **Aesthetic Preferences**: Desired finish (e.g., matte, glossy, textured) and color.
– **Processing Conditions**: Compatible with curing system and temperature ranges.
– **Budget**: Cost per pound of powder, operational costs, and material efficiency.
By understanding these factors and aligning them with the specific needs of your project, you can select the most suitable powder for electrostatic spraying. Always consult with a supplier if you’re unsure about the best option for your application, as they can provide expert guidance based on your exact requirements.
electrostatic powder gun
electrostatic powder painting equipment
electrostatic powder painting equipment factory
gema electrostatic powder coating
hyper smooth 02 led electrostatic powder coating system
powder coating vs electrostatic painting
advantages of electrostatic powder coating
aluminium electrostatic powder finishing plant
buy discount electrostatic powder coating machine
buy electrostatic powder painting equipment
cheap electrostatic powder coating machine
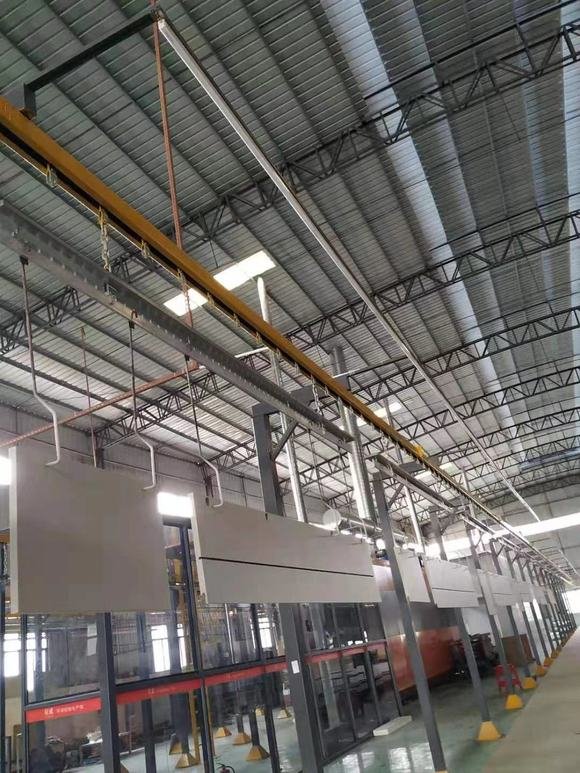