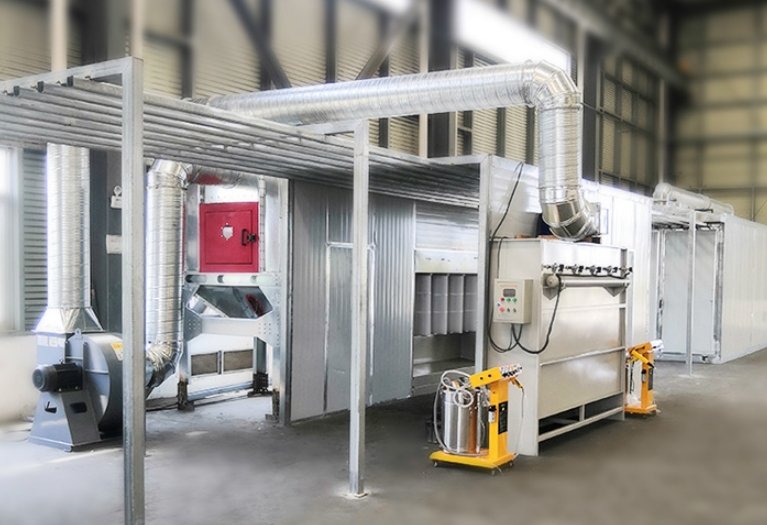
How to judge the quality of powder coating?
How to judge the quality of powder coating?
Judging the **quality of powder coating** is crucial to ensuring durability, aesthetics, and performance. A high-quality powder coating will provide a smooth, uniform finish, excellent resistance to weathering, and long-lasting protection against corrosion, scratches, and other environmental factors. Here’s a comprehensive guide on how to evaluate the quality of a powder coating:
### 1. **Visual Inspection (Aesthetic Quality)**
#### a. **Uniformity of the Coating**
– **Smoothness**: The surface should be smooth without visible defects like bumps, pinholes, or streaks. An uneven texture can indicate poor application or curing.
– **Finish Consistency**: The coating should have an even color and texture throughout the entire surface, with no areas showing under or over-coating. Inconsistencies in the finish can be a sign of poor spraying technique, curing issues, or improper powder choice.
– **No Runs or Drips**: A quality powder coating should not have visible runs, drips, or uneven thickness. This can indicate poor application techniques or inadequate gun settings.
– **Color Consistency**: If the powder is intended to be a uniform color, it should be free from any streaking, fading, or discoloration.
#### b. **Appearance of the Finish**
– **Gloss Level**: Ensure the gloss level (matte, satin, or glossy) is consistent across the surface, as uneven gloss can be a sign of poor application or improper curing.
– **Textured Coatings**: If a textured or wrinkle finish is used, it should have a consistent pattern without areas of inconsistent texture or “flat spots.”
– **No Contaminants**: The surface should be free from dust, dirt, or other contaminants. Foreign particles can stick to the coating if it’s improperly applied or not properly cleaned before spraying.
### 2. **Thickness of the Coating**
**Powder Coating Thickness** is crucial to ensure durability. Too thin a coat may not provide adequate protection, while too thick a coat can lead to defects like cracking or uneven finish.
#### a. **Measuring Thickness**
– **Magnetic Gauge**: A magnetic thickness gauge is often used to measure the coating thickness on ferrous metals (steel). For non-ferrous metals (like aluminum), an eddy current gauge can be used.
– **Recommended Thickness**: The typical thickness range for powder coatings is around **60 to 100 microns** (2.4 to 4 mils). The exact thickness depends on the application and substrate. For outdoor metal surfaces like guardrails, a thickness of 70-90 microns is common.
– **Consistency**: Check that the thickness is consistent across the entire surface, including edges and hard-to-reach areas.
### 3. **Adhesion and Bonding Strength**
The **adhesion** of the powder coating to the substrate is a critical indicator of quality. If the coating doesn’t bond well, it will peel or chip easily.
#### a. **Cross-Hatch Test**:
– This is a common test to evaluate the **adhesion** of the coating. A cross-hatch grid is cut into the powder coating, and adhesive tape is applied and quickly removed. If the coating comes off with the tape, the adhesion is poor.
– **ASTM D3359**: This standard provides a more detailed method for evaluating adhesion, scoring the coating on a scale from 0 to 5 (with 5 being excellent adhesion and 0 being poor).
#### b. **Peel Test**:
– **Peel Test**: In some cases, especially for thicker coatings, a peel test may be done. A piece of tape is applied to the coating and removed; if the coating detaches or curls, it suggests poor bonding.
### 4. **Impact Resistance**
Powder coatings should be able to withstand impacts without cracking or chipping, especially for applications like fences, guardrails, or automotive parts that may endure rough handling.
#### a. **Impact Test**:
– The **ASTM D2794** test is used to assess impact resistance. A standardized weight is dropped onto the coating from a specific height, and the coating is inspected for cracking, chipping, or other damage.
– **Visual Inspection**: After the impact test, examine the area for any signs of cracking, deformation, or delamination. A high-quality powder coating should resist these effects.
### 5. **Scratch Resistance**
Scratch resistance is especially important for coatings on frequently handled or exposed surfaces.
#### a. **Scratch Hardness Test**:
– **ASTM D3363**: This test uses a pencil hardness test where pencils of different hardness are used to scratch the coating. The hardest pencil that does not leave a mark is considered the scratch resistance value.
– **Visual Inspection**: After testing, any signs of visible scratches or damage indicate poor scratch resistance.
### 6. **Chemical Resistance**
Powder coatings need to be resistant to various chemicals (including solvents, oils, cleaning agents, etc.), especially in industrial or outdoor environments.
#### a. **Chemical Exposure**:
– The coating should be tested against common chemicals the product may encounter in its environment (such as oils, acids, cleaning agents, etc.).
– **Resistance**: After exposure to the chemicals, the coating should not show signs of discoloration, peeling, or bubbling.
### 7. **Corrosion Resistance**
Powder coatings are often used to prevent rust and corrosion, especially for metal parts exposed to moisture, salt, and other environmental factors.
#### a. **Salt Spray Test (ASTM B117)**:
– This test exposes the coated sample to a salt fog environment to evaluate how well it resists corrosion. A high-quality powder coating should withstand several hundred hours of salt spray without showing significant signs of corrosion or rust.
– **Observation**: Look for blistering, rust, or other signs of corrosion after the test. The longer the coating resists corrosion, the better the quality.
### 8. **UV and Weather Resistance**
For products exposed to the outdoors, the coating must resist fading, chalking, and degradation due to UV exposure and weathering.
#### a. **UV Testing**:
– **ASTM G154 or ASTM D4587**: These tests use accelerated weathering machines (like UV chambers) to simulate long-term exposure to UV light, rain, and other weather elements. The coating’s ability to resist fading, chalking, or cracking is evaluated.
– **Visual Inspection**: After testing, inspect the coating for fading, discoloration, or other signs of degradation. High-quality coatings, especially those made with polyester or fluoropolymer powders, should retain their color and integrity even after prolonged exposure to UV light.
### 9. **Flexibility and Curing Properties**
A high-quality powder coating should maintain its properties even when bent or flexed, such as on metal parts with edges or areas prone to movement.
#### a. **Bend Test**:
– **ASTM D522**: This test involves bending the coated substrate around a mandrel to see if the coating cracks or delaminates. The coating should not crack or peel under normal bending.
– **Visual Inspection**: Check for any signs of cracking, peeling, or loss of adhesion at the bend point.
### 10. **Environmental and Safety Compliance**
A good quality powder coating should comply with environmental regulations and safety standards. These include low **VOC (Volatile Organic Compounds)** emissions and adherence to industry standards for durability, aesthetics, and safety.
—
### Summary Checklist for Judging Powder Coating Quality:
1. **Visual Inspection**: Look for uniform color, smooth finish, no runs or drips.
2. **Thickness**: Measure the thickness with a gauge (typically 60–100 microns).
3. **Adhesion**: Perform a cross-hatch or peel test to assess adhesion strength.
4. **Impact Resistance**: Test for cracks or chips when subjected to impact.
5. **Scratch Resistance**: Check for scratches using hardness pencils.
6. **Chemical Resistance**: Expose the coating to chemicals and inspect for damage.
7. **Corrosion Resistance**: Perform a salt spray test and check for rust or corrosion.
8. **UV and Weather Resistance**: Use accelerated weathering tests to assess outdoor durability.
9. **Flexibility**: Test the coating for cracking or peeling when bent or flexed.
10. **Compliance**: Ensure the coating meets environmental and safety regulations.
By using these tests and evaluations, you can ensure that the powder coating you choose meets the necessary standards for your specific application and will perform well over time.
gema electrostatic powder coating
hyper smooth 02 led electrostatic powder coating system
powder coating vs electrostatic painting
advantages of electrostatic powder coating
aluminium electrostatic powder finishing plant
buy discount electrostatic powder coating machine
buy electrostatic powder painting equipment
cheap electrostatic powder coating machine
china electrostatic powder coating equipment
china electrostatic powder coating machine
china electrostatic powder painting equipment
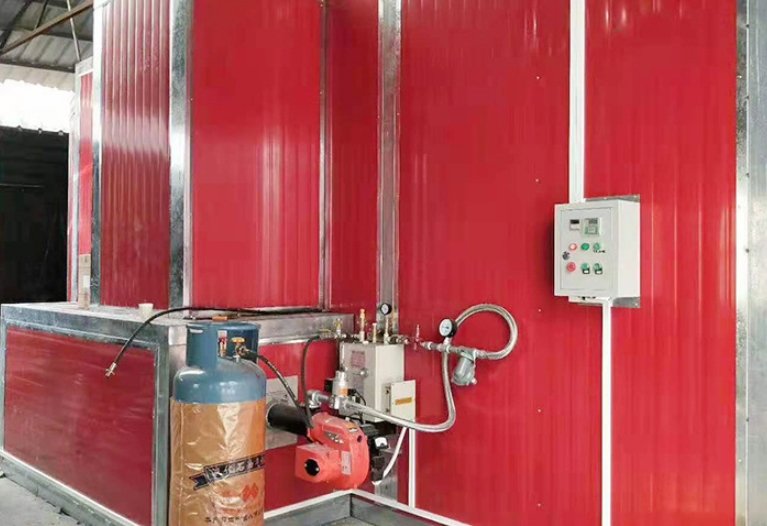