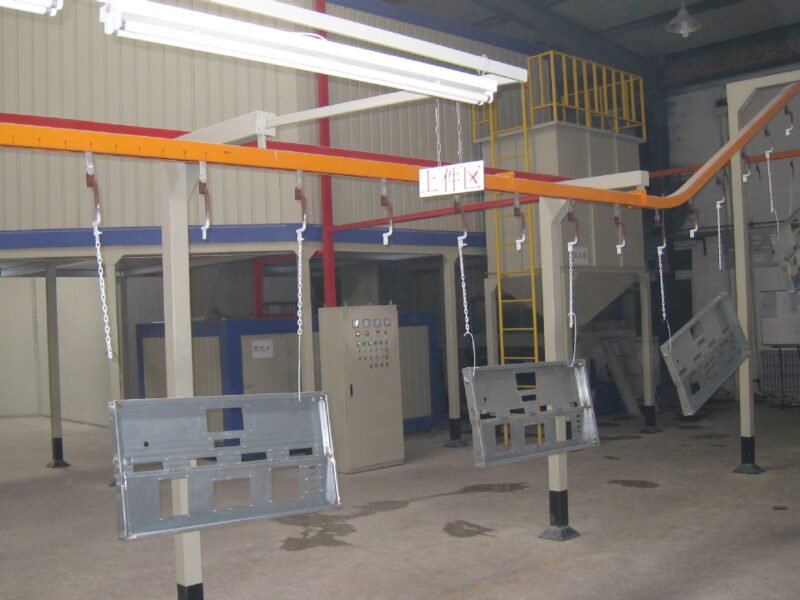
How to prevent equipment leakage during electrostatic powder spraying?
How to prevent equipment leakage during electrostatic powder spraying?
Preventing equipment leakage during electrostatic powder spraying is crucial for both safety and efficiency. Powder leakage can cause operational issues, reduce coating quality, and waste materials. Here are some key strategies to minimize and prevent leakage:
### 1. **Ensure Proper Sealing and Tight Connections**
– **Check seals and O-rings**: Regularly inspect and replace seals, gaskets, and O-rings on spray guns, hoses, and powder delivery systems. These components are often under pressure or exposed to wear and tear, which can cause leaks.
– **Tighten connections**: Ensure that all threaded or quick-connect fittings are tightened securely. Loose connections are a common cause of air and powder leakage.
### 2. **Use Quality, Compatible Components**
– **Quality powder coating equipment**: Invest in high-quality equipment that’s specifically designed for electrostatic powder coating. Cheap or incompatible parts can be more prone to failure, leading to leaks.
– **Match equipment specifications**: Ensure that hoses, nozzles, and spray guns are compatible with the powder coating system’s pressure and airflow requirements. Mismatched components may not provide an adequate seal, leading to leaks.
### 3. **Maintain Proper Air Pressure**
– **Regulate air pressure**: Too high or too low air pressure can cause instability in the powder delivery system, resulting in leakage or inconsistent powder flow. Use a regulator to maintain consistent air pressure within the recommended range for your equipment.
– **Inspect air lines**: Ensure that air supply hoses are free from cracks or holes that could cause air and powder leakage.
### 4. **Clean Equipment Regularly**
– **Prevent clogs and blockages**: Powder build-up within the system can cause pressure to build up in certain areas, potentially leading to leaks. Regularly clean spray guns, hoses, and fluidized beds to prevent clogging.
– **Avoid powder buildup**: Ensure that powder is not allowed to accumulate at points where it could block or disrupt airflow or material delivery, as this can cause leaks in the system over time.
### 5. **Use Powder Recovery Systems**
– **Install recovery systems**: Powder recovery systems help collect and reuse powder that escapes during spraying, preventing leakage into the environment. These systems not only reduce waste but also help prevent accidental leakage and contamination in the work area.
### 6. **Inspect and Replace Damaged Parts**
– **Routine maintenance**: Perform regular inspections of all powder coating equipment to identify any signs of wear or damage. Replace any worn or damaged parts immediately to avoid leaks.
– **Check for cracks**: Over time, spray guns and hoses can develop small cracks that lead to powder leakage. Ensure you replace these components as needed.
### 7. **Install Anti-Leak Features**
– **Check valves**: Some systems include check valves or air shut-off valves designed to control the flow of powder and air, preventing unwanted leakage when the equipment is not in use or when there’s a pressure drop.
– **Powder containment**: Use dust collection systems or powder containment enclosures around the spray booth to capture any powder that escapes, helping to minimize leakage into the surrounding environment.
### 8. **Train Operators on Proper Usage**
– **Operator training**: Ensure that all operators are properly trained on how to handle and maintain the equipment. Improper use, like leaving the spray gun unattended or not correctly securing hoses, can contribute to leaks.
– **Proper shutdown procedures**: Operators should always follow proper shutdown procedures after each use, which includes turning off valves and ensuring all components are securely in place.
### 9. **Monitor the System for Leaks**
– **Pressure testing**: Periodically perform pressure tests on the system to detect any weak spots that might cause leaks. This can be done by running the system at higher-than-normal pressures and observing any areas where powder or air escapes.
– **Leak detection kits**: Some systems come with leak detection kits or detectors that can help identify small leaks that are not immediately visible.
### 10. **Use Leak-Proof or Sealed Containers for Powder**
– **Proper storage**: Ensure that powder is stored in airtight, leak-proof containers to prevent spillage or contamination. Improperly sealed powder containers can contribute to leakage if mishandled during setup or storage.
### Conclusion:
Preventing leakage in electrostatic powder spraying involves maintaining equipment, ensuring proper connections, and using quality parts designed to withstand the demands of the process. Regular inspection, cleaning, and correct operation by trained personnel are key to minimizing the risk of leaks, improving system efficiency, and reducing the waste of powder material.
ectfe electrostatic powder
electrostatic adhesion powder
electrostatic charge powder
electrostatic coating powder
electrostatic coating vs powder coating
electrostatic dissipative powder coatings
electrostatic drum powder paint process
electrostatic dry powder coating
electrostatic enamel powder
electrostatic enamel powder coating
electrostatic fluidization bed for powder coating
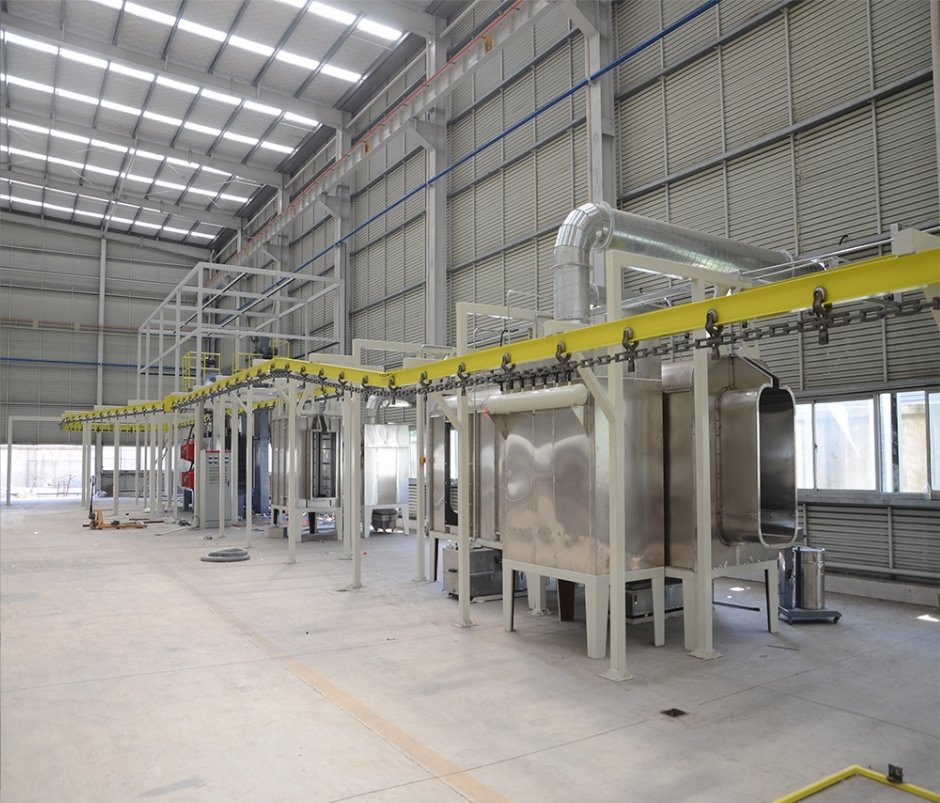