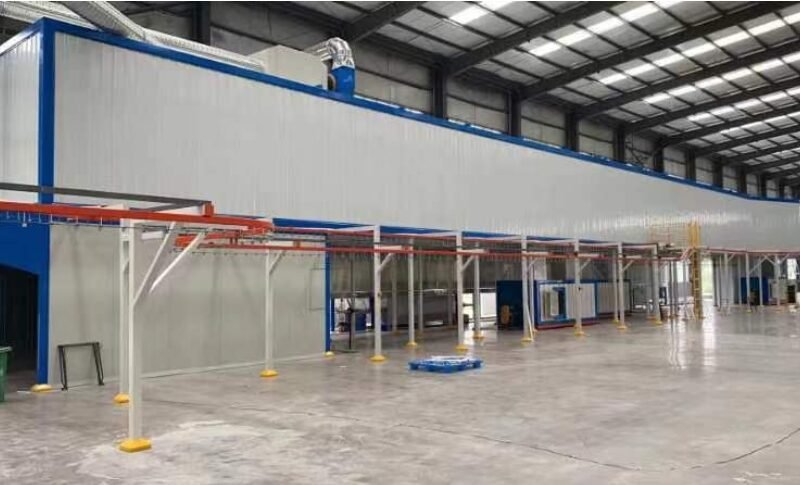
How to solve the problem of cracking on the edges of MDF powder coating electrostatic spraying?
How to solve the problem of cracking on the edges of MDF powder coating electrostatic spraying?
Cracking on the edges of MDF (Medium Density Fiberboard) powder coating during electrostatic spraying can be caused by several factors, including improper surface preparation, coating application, or curing. Here’s how to address and prevent this issue:
### 1. **Proper Surface Preparation**:
– **Edge Sealing**:
– MDF edges are more porous and absorbent than the flat surfaces. Seal the edges with a suitable edge sealer or primer to reduce absorption and prevent the powder from sinking into the fibers, which can lead to cracking.
– **Sanding and Cleaning**:
– Sand the MDF edges smoothly and clean thoroughly to remove any dust, debris, or loose fibers that can interfere with coating adhesion.
### 2. **Use the Right Powder Coating**:
– **Formulated for MDF**:
– Use powder coatings specifically designed for MDF. These powders are formulated to provide better flexibility and adhesion on wood substrates, which can help prevent cracking.
– **Flexible Powders**:
– Choose a powder coating with higher flexibility or elasticity to accommodate the natural expansion and contraction of MDF without cracking.
### 3. **Control Application Thickness**:
– **Even Coating**:
– Apply an even, consistent layer of powder on all surfaces, including edges. Avoid applying too thick or too thin a layer, as both can lead to cracking or other defects.
– **Multiple Thin Coats**:
– Consider applying multiple thin coats instead of one thick coat to build up the desired thickness gradually, reducing the stress on the coating.
### 4. **Optimize Electrostatic Settings**:
– **Adjust Voltage**:
– Lower the electrostatic voltage when coating edges to prevent excessive powder build-up, which can lead to uneven curing and cracking.
– **Proper Gun Positioning**:
– Ensure the spray gun is positioned correctly to provide even coverage on edges, avoiding excessive powder accumulation.
### 5. **Proper Curing Process**:
– **Controlled Curing**:
– Follow the manufacturer’s recommended curing temperature and time closely. MDF can be sensitive to heat, and incorrect curing can cause the substrate to expand or contract, leading to cracking.
– **Gradual Heating**:
– Use a gradual heating process to allow the MDF to reach the curing temperature uniformly, minimizing thermal stress on the coating.
### 6. **Environmental Control**:
– **Humidity and Temperature**:
– Maintain stable environmental conditions in the spraying and curing areas. High humidity can affect the MDF and the powder, leading to adhesion and curing issues.
– **Minimize Moisture Absorption**:
– Store MDF in a controlled environment to minimize moisture absorption, which can cause dimensional changes and contribute to cracking.
### 7. **Use MDF-Specific Equipment and Techniques**:
– **Preheating MDF**:
– Preheat the MDF slightly before applying the powder to reduce moisture content and improve powder adhesion.
– **Edge-Focused Techniques**:
– Pay special attention to edges during application, ensuring they are adequately coated and cured without overloading.
### 8. **Regular Maintenance and Quality Checks**:
– **Inspect Equipment**:
– Regularly inspect and maintain spraying equipment to ensure consistent application and avoid issues like clogs or inconsistent powder flow.
– **Quality Control**:
– Perform routine inspections of coated parts to detect and address cracking early. Adjust the process as needed based on findings.
By addressing these factors, you can minimize the risk of cracking on the edges of MDF during electrostatic powder spraying, resulting in a smooth, durable, and high-quality finish.
electrostatic spray powder
electrostatic spray powder coating ct
electrostatic spray powder coating equipment
electrostatic spray powder coating machine
electrostatic spray powder coating machine spraying gun paint system equipment
electrostatic vs powder coated paint
electrostatic vs powder coating
electrostatic wrap powder coat
electrostatic wrap powder coating
electrostatically applied powder coating
electrostatically powder coated
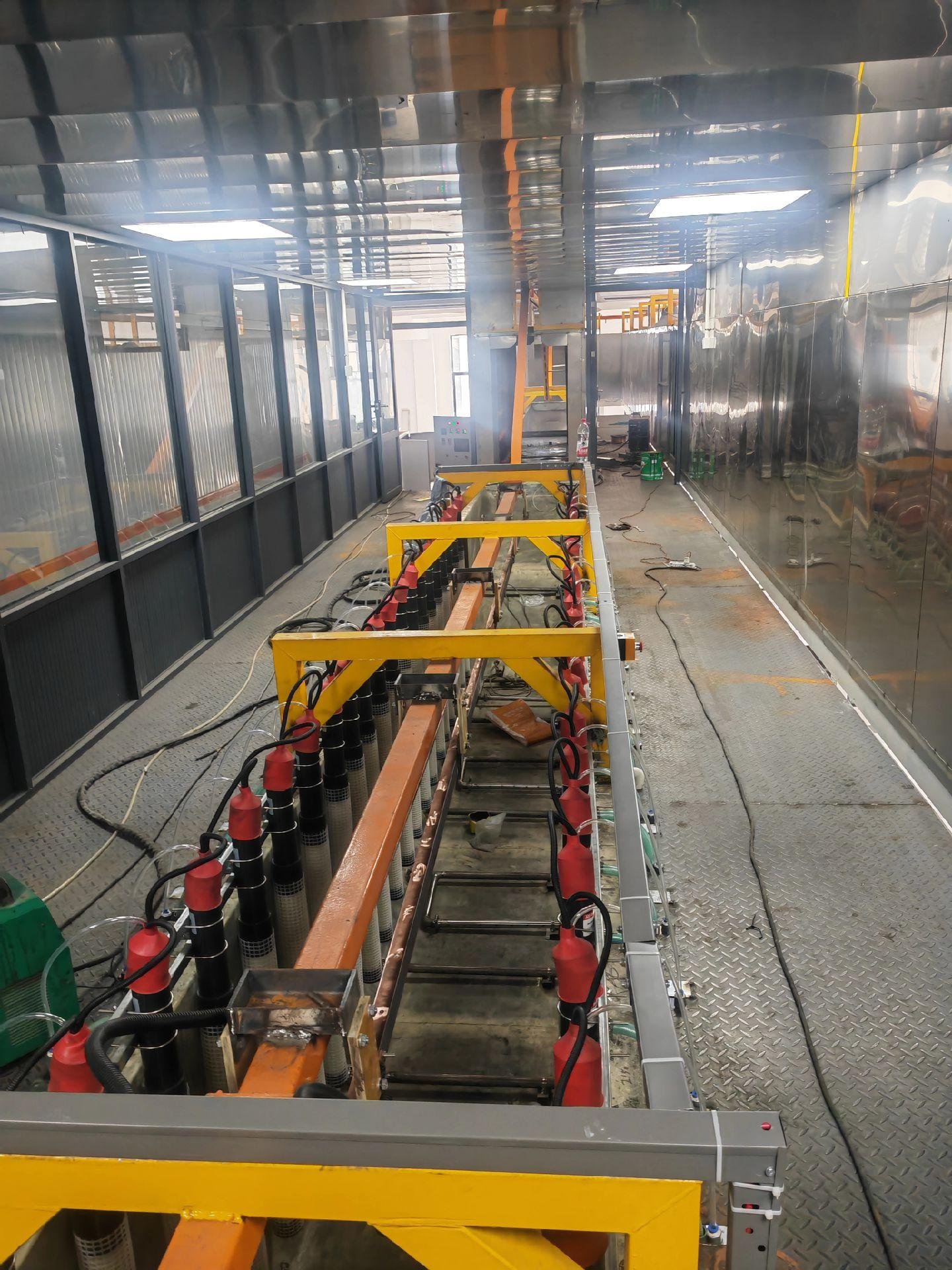