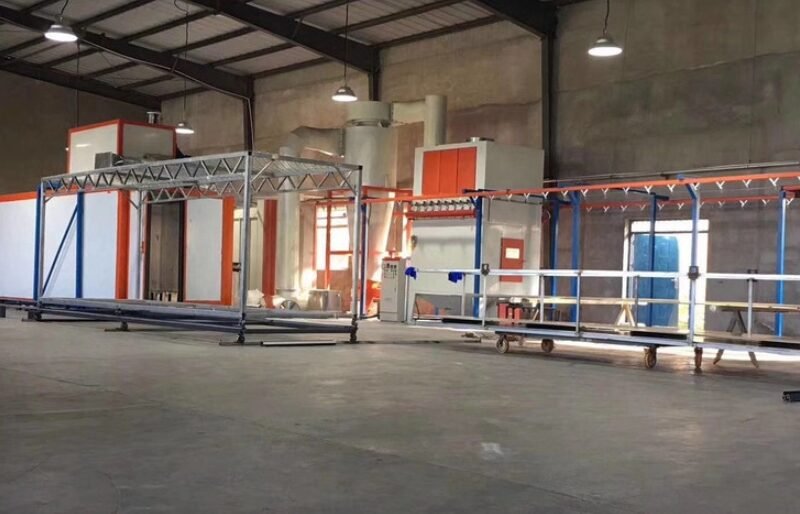
What are the key factors affecting powder coating thickness in electrostatic spraying production?
What are the key factors affecting powder coating thickness in electrostatic spraying production?
The thickness of powder coating in electrostatic spraying production is influenced by several key factors that affect the application process and the final quality of the coating. These factors can be grouped into categories related to equipment, material, and operational conditions:
—
### **1. Equipment Factors**
1. **Electrostatic Voltage**:
– Higher voltage improves powder adhesion but can cause “back ionization” if too high, leading to uneven thickness.
– Lower voltage may result in inadequate powder deposition.
2. **Gun-to-Substrate Distance**:
– Ideal distance: 15-30 cm (6-12 inches), depending on the equipment.
– Too close: Excessive powder buildup and uneven coating.
– Too far: Thin or inconsistent coating due to poor powder transfer.
3. **Spray Gun Type and Nozzle**:
– Flat or round nozzles affect the powder spray pattern and deposition rate.
– The choice of gun impacts coating thickness uniformity.
4. **Powder Feed Rate**:
– Higher feed rates lead to thicker coatings but can waste material.
– Lower feed rates may cause insufficient thickness.
—
### **2. Material Factors**
1. **Powder Characteristics**:
– **Particle Size**: Smaller particles produce thinner coatings; larger particles create thicker layers.
– **Powder Flowability**: Affects even distribution during spraying.
– **Resin Type**: Some powders are designed for specific thickness ranges.
2. **Powder Coverage**:
– The powder’s ability to cover the substrate affects thickness. Higher-quality powders tend to produce more uniform coatings.
—
### **3. Substrate Factors**
1. **Surface Preparation**:
– Clean, smooth surfaces allow for better powder adhesion and consistent thickness.
– Contaminants like oil, grease, or rust lead to uneven application.
2. **Substrate Material**:
– Conductive substrates (e.g., metals) allow better powder adhesion compared to non-conductive materials.
– Variations in surface geometry (e.g., corners, edges, and recesses) can lead to uneven thickness.
3. **Grounding Quality**:
– Proper grounding is essential for creating the electrostatic charge required for powder adhesion.
– Poor grounding causes inconsistent deposition and variable thickness.
—
### **4. Environmental and Operational Factors**
1. **Humidity and Temperature**:
– High humidity can cause powder clumping, reducing spray efficiency.
– Extreme temperatures can affect powder flow and adhesion.
2. **Operator Technique**:
– Spraying angle, speed, and pattern influence coating uniformity.
– Overlapping passes ensure even thickness but can lead to over-application in some areas.
3. **Curing Conditions**:
– Over or under-curing can affect the final film thickness as the powder melts and flows out.
—
### **5. Design and Geometry of the Part**
1. **Complex Shapes**:
– Corners, edges, and recesses can result in uneven powder deposition (e.g., Faraday cage effect).
2. **Large or Flat Surfaces**:
– Large surfaces may require careful gun movement to avoid streaks or uneven coverage.
—
### **How to Control Thickness**
– Regularly calibrate equipment (e.g., voltage, feed rate).
– Use high-quality powder coatings with appropriate characteristics.
– Ensure thorough substrate cleaning and proper grounding.
– Adjust operator technique for specific part geometries.
– Monitor environmental conditions and maintain optimal curing temperatures.
By managing these factors, you can achieve consistent and desired coating thickness in electrostatic spraying production.
electrostatic painting sprayer
electrostatic spray gun for sale
electrostatic sprayer used
electrostatic sprayer uses
electrostatic water sprayer
graco electrostatic spray gun
paint sprayer electrostatic
paint spraying electrostatics
victory electrostatic spraying
electrostatic paint sprayer rental
electrostatic paint spraying company
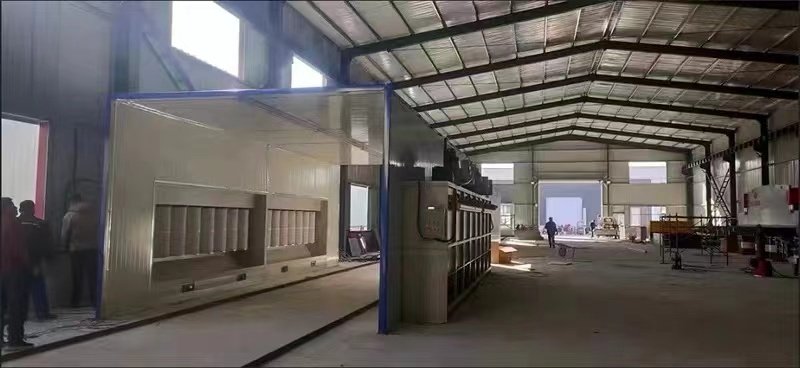