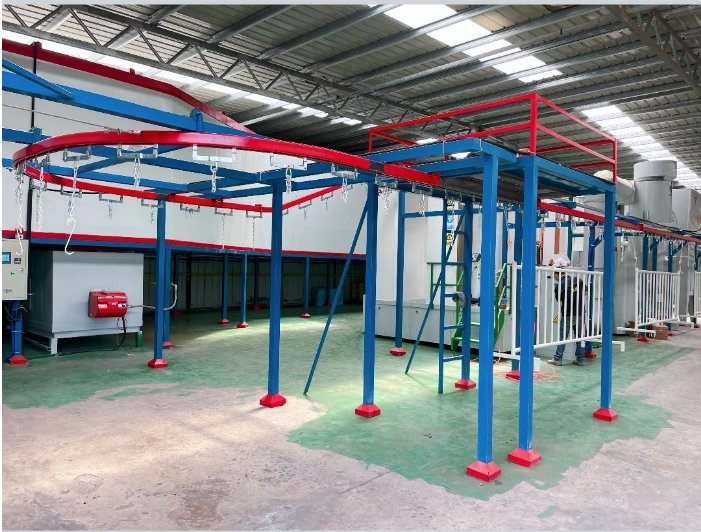
What are the quality requirements for electrostatic spraying powder?
What are the quality requirements for electrostatic spraying powder?
The quality requirements for electrostatic spraying powder are crucial to ensure the durability, adhesion, appearance, and overall performance of the coating. High-quality powder not only improves the protective characteristics of the coating but also enhances its aesthetic appeal. Here are the main factors and quality requirements to consider for electrostatic spraying powder:
### 1. **Particle Size Distribution:**
– **Importance:** The powder particles need to be uniform for smooth and even application. If the particles are too fine, they may not carry enough electrostatic charge, and if they are too coarse, they may clog the equipment.
– **Requirement:** Particle size should typically range between 10-100 microns, with most powders averaging around 30-50 microns. A balanced distribution ensures better coverage and consistency.
### 2. **Electrostatic Chargeability:**
– **Importance:** The ability of the powder to accept and retain an electrostatic charge is key to proper adhesion to the workpiece.
– **Requirement:** High chargeability ensures better transfer efficiency, less powder wastage, and better coverage, even on complex geometries.
### 3. **Flow Properties:**
– **Importance:** Powders must flow smoothly through the spray gun without clogging or forming lumps.
– **Requirement:** Excellent flowability ensures even distribution on the surface and prevents issues like orange peel texture or surface imperfections.
### 4. **Film Formation and Cure:**
– **Importance:** Proper curing is necessary to create a durable and protective film.
– **Requirement:** Powders should form a smooth, uniform film when melted and cured. The coating should meet the manufacturer’s recommended curing schedule (e.g., specific temperatures and times) to achieve optimal hardness and durability.
### 5. **Adhesion:**
– **Importance:** The coating must adhere well to the substrate to provide long-lasting protection.
– **Requirement:** The powder should meet the standards for adhesion tests (like ASTM D3359), ensuring the coating won’t peel, chip, or flake under stress or environmental conditions.
### 6. **Gloss and Color Consistency:**
– **Importance:** The appearance of the final product is critical for customer satisfaction, especially for consumer goods.
– **Requirement:** Consistent gloss and color should be maintained across different batches. Powders should comply with industry standards such as ASTM D523 (gloss measurement) and meet acceptable tolerance levels for color variation (often measured using a spectrophotometer).
### 7. **Corrosion Resistance:**
– **Importance:** Corrosion resistance is a key performance characteristic, particularly for outdoor applications or items exposed to harsh environments.
– **Requirement:** The powder should pass corrosion resistance tests like ASTM B117 (salt spray test) and ISO 12944 (for long-term exposure). This ensures the coating will protect the substrate from rust and degradation over time.
### 8. **Impact and Abrasion Resistance:**
– **Importance:** The coated surface should withstand mechanical stress and impacts without damage.
– **Requirement:** Powder coatings should comply with industry standards for impact resistance (e.g., ASTM D2794) and abrasion resistance (e.g., ASTM D4060).
### 9. **Weatherability (for outdoor use):**
– **Importance:** For outdoor applications, the powder must resist UV degradation, fading, and chalking.
– **Requirement:** Outdoor-grade powders must pass tests like ASTM D4587 (UV resistance) and ASTM D4214 (chalking resistance) to ensure long-term performance in sunlight and harsh weather.
### 10. **Chemical Resistance:**
– **Importance:** The powder coating must resist degradation when exposed to chemicals like cleaning agents, oils, or industrial chemicals.
– **Requirement:** Depending on the application, the powder should meet chemical resistance standards such as ASTM D1308 (resistance to chemical spots).
### 11. **Environmental and Safety Compliance:**
– **Importance:** Powders should be environmentally friendly and comply with regulations regarding the use of hazardous substances.
– **Requirement:** Many industries require powders to be free from harmful volatile organic compounds (VOCs) and heavy metals (e.g., lead, cadmium). Compliance with RoHS, REACH, and other environmental standards is essential.
### 12. **Shelf Life and Stability:**
– **Importance:** Powders should remain stable over time without degradation or clumping.
– **Requirement:** Most powder coatings have a shelf life of 6-12 months if stored properly (in a cool, dry environment). They should not experience significant changes in properties or performance during this period.
### Summary of Quality Requirements:
1. **Particle size consistency**: 10-100 microns range.
2. **High chargeability**: Ensures better coating adhesion and coverage.
3. **Smooth flowability**: Prevents clogging and application issues.
4. **Proper curing**: For optimal film formation.
5. **Strong adhesion**: Meets ASTM D3359 adhesion test.
6. **Gloss and color uniformity**: Consistent appearance.
7. **Corrosion resistance**: Compliance with ASTM B117, ISO 12944.
8. **Impact and abrasion resistance**: Meets ASTM standards.
9. **UV and weather resistance**: Passes ASTM D4587 (UV) and ASTM D4214 (chalking).
10. **Chemical resistance**: Protects against chemical exposure.
11. **Compliance**: RoHS, REACH, and other environmental standards.
12. **Shelf life**: 6-12 months of stable performance.
Quality control and consistency across all these factors are essential for achieving the desired performance in electrostatic powder spraying applications.

china electrostatic powder painting equipment manufacturer
china electrostatic powder painting equipment supplier
corrosion resistant electrostatic powder
difference between electrostatic painting and powder coating
difference between powder coating and electrostatic paint
diy electrostatic powder coating
ectfe electrostatic powder
electrostatic adhesion powder
electrostatic charge powder
electrostatic coating powder
electrostatic coating vs powder coating