
What are the quality requirements for electrostatic spraying powder?
What are the quality requirements for electrostatic spraying powder?
Electrostatic spraying powder, often used in powder coating processes, must meet specific quality requirements to ensure a durable, smooth, and aesthetically pleasing finish. Here are the key quality requirements for electrostatic spraying powder:
### 1. **Particle Size Distribution**
– **Consistent Particle Size**: The powder should have a uniform particle size, typically ranging from 10 to 100 microns. This ensures even coverage and proper adhesion.
– **Control of Fine Particles**: Excessive fine particles can lead to poor transfer efficiency and an inconsistent finish, while larger particles may result in a rough texture.
### 2. **Electrostatic Properties**
– **Chargeability**: The powder must easily acquire an electrostatic charge when sprayed. This allows the particles to adhere to the grounded substrate.
– **Good Tribo and Corona Properties**: Depending on the type of electrostatic system (tribo or corona), the powder should exhibit excellent behavior in the chosen system.
### 3. **Flow Properties**
– **Flow Rate**: The powder should have good flow properties to ensure even and continuous application without clogging or excessive clumping.
– **Fluidization**: The powder must fluidize well in the spray system, allowing for efficient spraying and coating.
### 4. **Adhesion**
– **Strong Adhesion to Substrate**: After application, the powder must adhere well to the substrate before curing, ensuring that it remains in place during the baking process.
– **Adhesion After Curing**: The coating should have strong adhesion post-curing, resisting peeling or flaking.
### 5. **Curing Properties**
– **Complete Curing**: The powder must cure fully under specified conditions (temperature and time) to achieve the desired mechanical and chemical properties.
– **Cure Flexibility**: Some flexibility in the cure window (time and temperature) is often required to accommodate various production setups.
### 6. **Color Consistency and Appearance**
– **Uniform Color and Gloss**: The powder should provide consistent color and gloss, without streaks, patches, or color variation.
– **No Pinholes or Orange Peel**: The finish should be smooth and free from defects such as pinholes, orange peel, or other surface imperfections.
### 7. **Mechanical Properties**
– **Impact Resistance**: The coating should be resistant to impacts, ensuring durability in applications where physical stress is expected.
– **Flexibility**: Depending on the substrate, the coating should have some flexibility without cracking or peeling.
– **Abrasion Resistance**: High abrasion resistance is essential for maintaining the coating’s appearance and function in high-wear environments.
### 8. **Chemical and Corrosion Resistance**
– **Resistance to Chemicals**: The powder must provide protection against chemicals like solvents, acids, and alkalis, depending on the application.
– **Corrosion Protection**: For outdoor or corrosive environments, the powder coating must offer good corrosion resistance to prevent degradation of the underlying substrate.
### 9. **Environmental Compliance**
– **Low or No Volatile Organic Compounds (VOCs)**: The powder must comply with environmental standards, containing low or no VOCs to minimize environmental impact.
– **Non-Toxic**: The powder should be free from harmful chemicals such as lead, cadmium, or other heavy metals, especially for applications in sensitive industries like food processing or healthcare.
### 10. **Shelf Life and Storage Stability**
– **Shelf Stability**: The powder should have a long shelf life without degrading or clumping. Proper storage conditions must maintain the powder’s performance characteristics.
– **Temperature Sensitivity**: The powder must resist significant changes in properties due to temperature fluctuations during storage.
Ensuring these quality parameters are met is crucial for achieving a high-quality, durable finish in electrostatic powder coating applications.
electrostatic powder coating technician
electrostatic powder coating technician jobs
electrostatic powder coating technology
electrostatic powder coating theory
electrostatic powder coating thickness
electrostatic powder coating voltage
electrostatic powder coating vs powder coating
electrostatic powder coating wikipedia
electrostatic powder coating without baking
electrostatic powder coating without making
electrostatic powder coatings
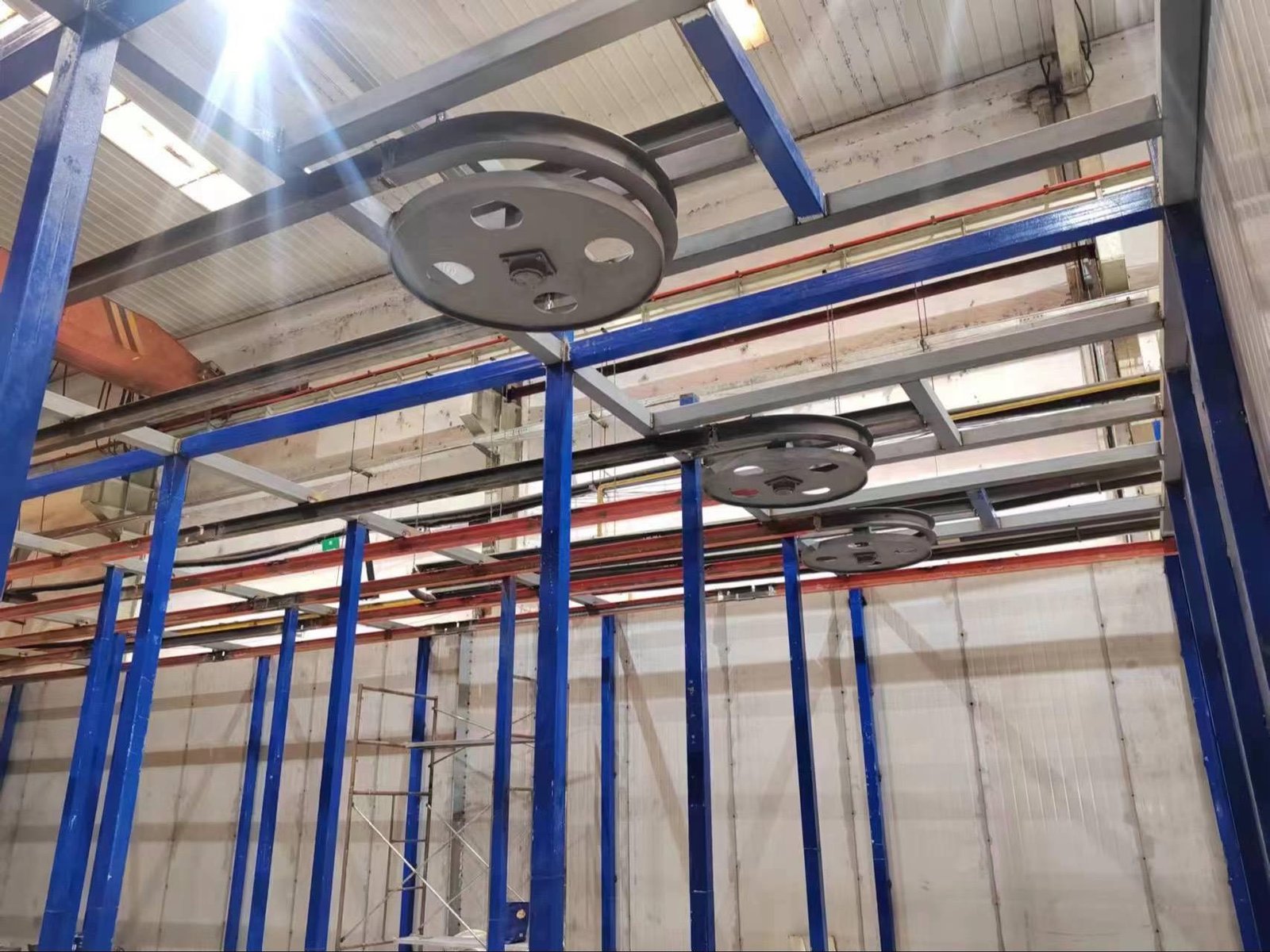