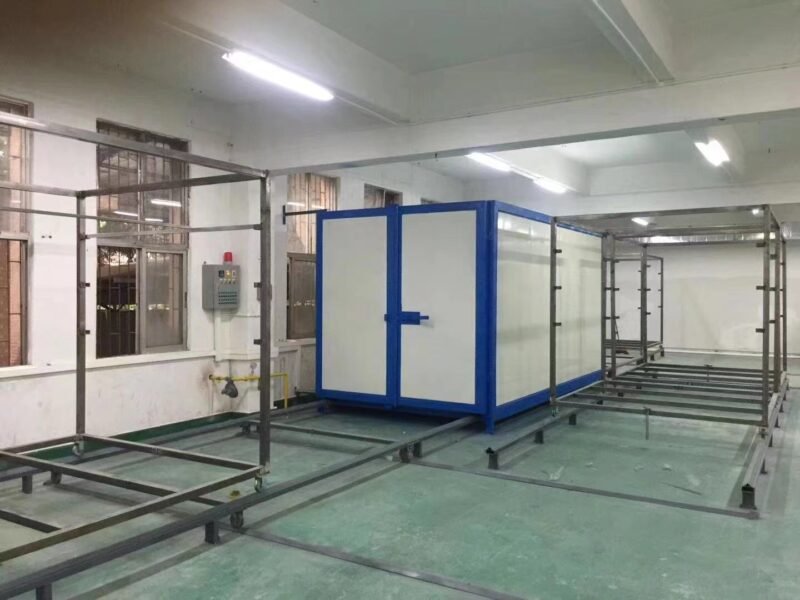
What are the reasons why electrostatic powder spraying affects the powder coating dead corner rate?
What are the reasons why electrostatic powder spraying affects the powder coating dead corner rate?
The “dead corner” rate in electrostatic powder spraying refers to areas of a workpiece where the powder coating fails to adhere or is unevenly applied. These issues are often due to factors affecting the application process and equipment. Here are the primary reasons why electrostatic powder spraying affects the powder coating dead corner rate:
—
### **1. Faraday Cage Effect**
– **What It Is:** The Faraday cage effect occurs when electrostatic forces prevent powder particles from penetrating recessed or tight areas of the workpiece.
– **Impact:** Corners, crevices, and deep recesses may have uneven or insufficient coating because the electrostatic charge repels powder particles away from these areas.
—
### **2. Improper Spray Gun Settings**
– **Voltage Issues:** Too high a voltage can exacerbate the Faraday cage effect by creating a strong electrostatic field that prevents powder from reaching dead corners.
– **Flow Rate:** Excessive powder flow can cause overspray in accessible areas, leaving corners undercoated.
—
### **3. Poor Gun Positioning and Movement**
– **Distance:** Incorrect gun distance from the workpiece can lead to uneven application, especially in tight spots.
– **Angle:** Failure to angle the gun properly can prevent powder from reaching recessed areas.
—
### **4. Workpiece Geometry**
– **Complex Shapes:** Irregular or intricate designs with sharp edges, deep recesses, or narrow spaces are more prone to dead corners.
– **Material Conductivity:** Poorly conductive materials may not attract the powder as effectively in difficult-to-reach areas.
—
### **5. Inadequate Pre-Treatment**
– **Contamination:** Dirt, grease, or residues on the workpiece surface can interfere with powder adhesion, particularly in corners.
– **Surface Condition:** Uneven or rough surfaces can create shadowing effects, leading to coating voids.
—
### **6. Insufficient Airflow**
– **Booth Design:** Poor airflow in the spray booth can prevent powder from reaching all areas evenly.
– **Air Pressure:** Insufficient air pressure in the spray gun may reduce the powder’s ability to penetrate corners.
—
### **7. Powder Quality**
– **Particle Size Distribution:** Irregular particle sizes can affect how powder flows and adheres, especially in hard-to-reach areas.
– **Chargeability:** Low-quality powders may not charge effectively, reducing their ability to adhere in corners.
—
### **8. Operator Skill**
– **Technique:** Inconsistent spraying techniques or lack of experience can result in dead corners.
– **Awareness:** Operators may overlook certain areas, especially in complex geometries.
—
### **9. Environmental Conditions**
– **Humidity:** High humidity can affect the electrostatic charge, reducing powder adhesion in challenging areas.
– **Temperature:** Extreme temperatures may alter powder fluidization or charge properties.
—
### **10. Equipment Limitations**
– **Nozzle Design:** Standard nozzles may not be optimized for reaching corners or recesses.
– **Gun Type:** Manual guns may struggle with consistency in corners compared to automated systems.
—
### **Solutions to Reduce Dead Corners**
1. **Adjust Voltage:** Lower the voltage when spraying recessed areas to reduce the Faraday cage effect.
2. **Use Specialized Nozzles:** Select nozzles designed for corners, such as deflector or angled nozzles.
3. **Optimize Gun Positioning:** Spray from multiple angles to improve coverage.
4. **Pre-Treat Thoroughly:** Ensure the workpiece is clean and properly prepped.
5. **Select High-Quality Powders:** Use powders with good chargeability and consistent particle sizes.
6. **Train Operators:** Provide training for better technique and awareness of problem areas.
7. **Improve Airflow:** Ensure proper booth design and air pressure for consistent powder flow.
8. **Utilize Automation:** Automated systems can provide more consistent application in complex geometries.
By addressing these factors, you can significantly reduce the dead corner rate and achieve a uniform, high-quality finish.
electrostatic backpack sprayer
electrostatic paint sprayer for sale
electrostatic sprayer disinfectant
electrostatic sprayer ryobi
electrostatic water spray
graco electrostatic paint sprayer
ryobi electrostatic sprayer not spraying
ryobi one+ 18v cordless electrostatic 0.5 gal. sprayer
electrostatic painting sprayer
electrostatic spray gun for sale
electrostatic sprayer used
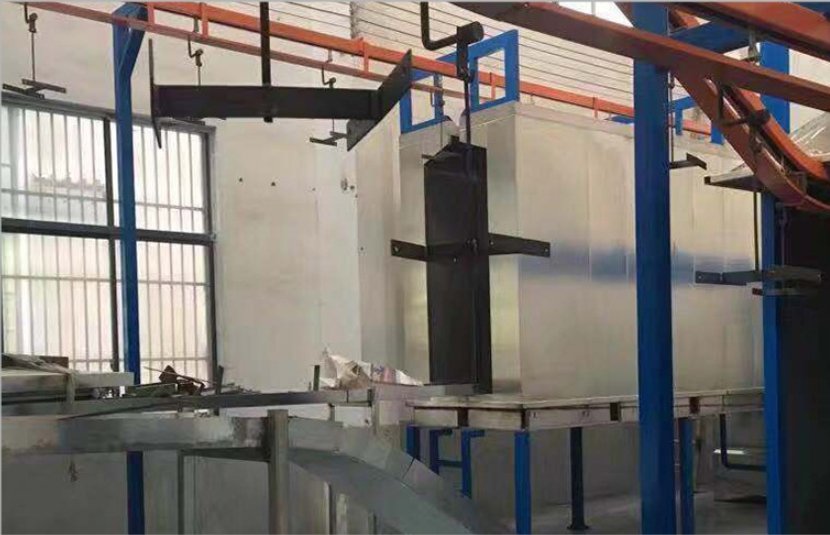