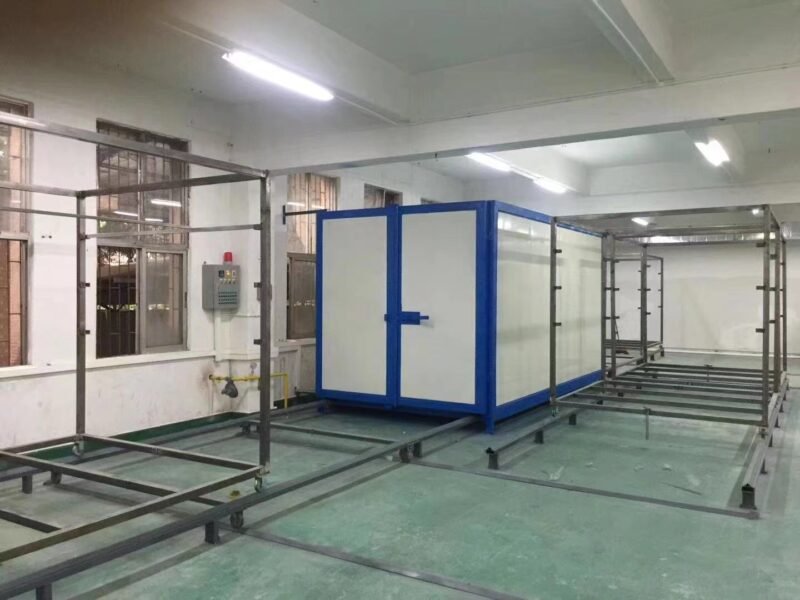
What is the electrostatic spray coating equipment production line
What is the electrostatic spray coating equipment production line
The **electrostatic spray coating equipment production line** is a manufacturing setup designed to apply coatings, such as paint or powder, onto surfaces using electrostatic spray technology. This process leverages the principle of electrostatic attraction, where the coating particles are charged and attracted to the surface of the object (which is grounded or has an opposite charge). This results in an even, efficient, and high-quality coating.
Here are the key components and steps involved in an electrostatic spray coating production line:
### 1. **Pretreatment Section**
– **Purpose**: To clean and prepare the surface of the object to ensure the coating adheres properly.
– **Process**: Includes cleaning, rinsing, and possibly applying a chemical treatment to the surface of the object. It may involve processes like degreasing, phosphating, or etching.
### 2. **Drying Section**
– **Purpose**: After pretreatment, the object needs to be dried to remove moisture.
– **Process**: This is usually done in a drying oven or chamber to ensure no residual water affects the coating process.
### 3. **Electrostatic Spray Gun**
– **Purpose**: To apply the coating (liquid or powder) to the object.
– **Working Principle**: The spray gun imparts an electrostatic charge to the particles of the coating material. When sprayed, these charged particles are attracted to the grounded or oppositely charged object, creating a uniform coating.
### 4. **Coating Booth**
– **Purpose**: The booth is where the spraying takes place. It is designed to contain overspray and prevent contamination of the surrounding area.
– **Types**: There are dry filter booths (for liquid coatings) and recovery booths (for powder coatings where overspray can be recovered and reused).
### 5. **Curing Section (for Powder Coating)**
– **Purpose**: To cure or harden the coating after application.
– **Process**: In the case of powder coatings, the object is heated in a curing oven to allow the powder to melt, flow, and form a durable coating. For liquid coatings, a drying oven might be used for drying or curing the paint.
### 6. **Conveyor System**
– **Purpose**: To move parts through the various stages of the production line automatically.
– **Types**: This can be a continuous conveyor (for high production throughput) or a batch system (for smaller production volumes).
### 7. **Control System**
– **Purpose**: To regulate and monitor the operations of the entire line, ensuring consistent quality and efficiency.
– **Features**: Can include programmable logic controllers (PLCs), sensors, and feedback loops to maintain precise control over temperatures, spray patterns, and conveyor speeds.
### Advantages of Electrostatic Spray Coating:
– **High Efficiency**: The electrostatic attraction reduces waste as more coating adheres to the object.
– **Uniform Coating**: Results in an even layer of paint or powder without streaks or variations.
– **Cost-Effective**: Reduces material waste, overspray, and labor costs.
– **Versatile**: Can be used on various materials such as metals, plastics, and even some ceramics.
### Applications
– Automotive industry (for coating car parts).
– Appliance manufacturing.
– Furniture and metal fabrications.
– Aerospace components.
– Industrial equipment.
In summary, an electrostatic spray coating equipment production line automates the process of applying coatings in an efficient and uniform manner, making it ideal for high-volume industrial applications.
electrostatic powder spray gun price
electrostatic powder spray process
electrostatic spray gun powder coating
electrostatic spray powder
electrostatic spray powder coating ct
electrostatic spray powder coating equipment
electrostatic spray powder coating machine
electrostatic spray powder coating machine spraying gun paint system equipment
electrostatic vs powder coated paint
electrostatic vs powder coating
electrostatic wrap powder coat
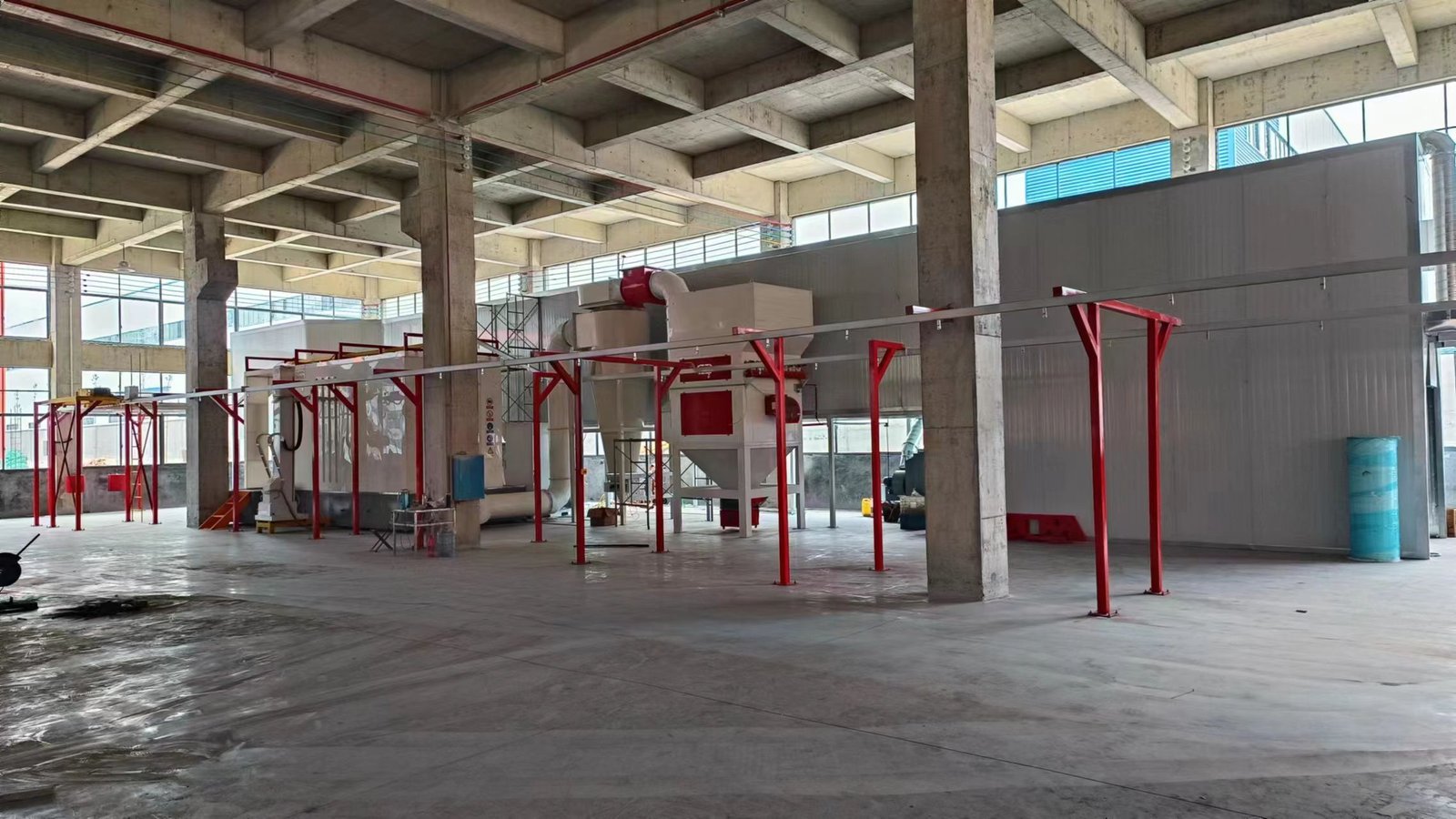