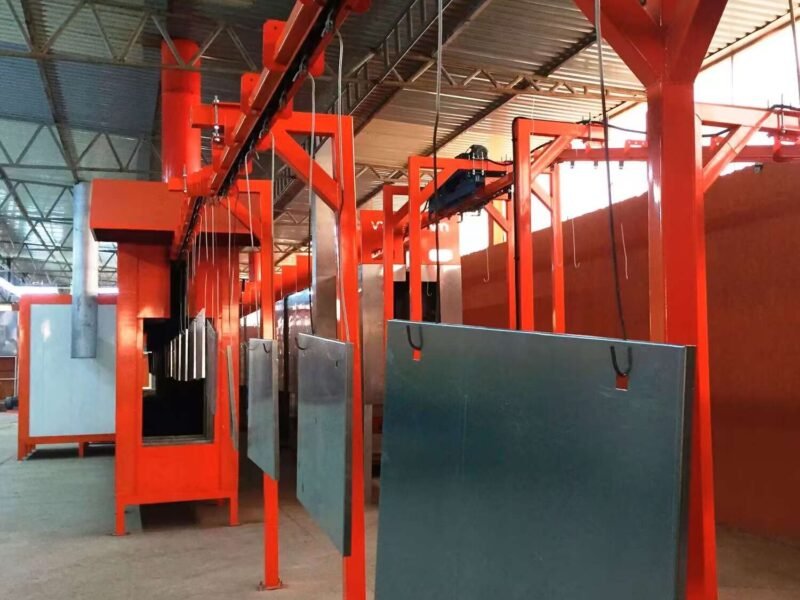
What is the reason for excessive powder on electrostatic powder spraying workpieces?
What is the reason for excessive powder on electrostatic powder spraying workpieces?
Excessive powder buildup during electrostatic powder spraying can occur due to several factors, leading to inefficient material use, uneven coatings, or defects. Here’s a detailed look at the possible reasons and solutions:
—
### **1. Excessive Powder Output**
– **Cause**:
– The powder feed rate is set too high, causing more powder to be sprayed than necessary.
– **Solution**:
– Reduce the powder flow rate from the hopper to the spray gun.
– Calibrate the feed system to ensure the appropriate amount of powder is delivered.
—
### **2. Incorrect Voltage Settings**
– **Cause**:
– High voltage may cause powder particles to accumulate excessively due to increased attraction, especially on flat surfaces.
– **Solution**:
– Lower the voltage to the optimal range (typically 60–100 kV) for the workpiece material and geometry.
– Adjust voltage based on workpiece design to avoid overcharging and uneven buildup.
—
### **3. Improper Gun-to-Workpiece Distance**
– **Cause**:
– Holding the spray gun too close to the workpiece causes concentrated powder deposition.
– **Solution**:
– Maintain the recommended gun-to-workpiece distance (6–12 inches, depending on the application).
– Train operators to use consistent spraying techniques.
—
### **4. Overlapping Spray Passes**
– **Cause**:
– Excessive overlap of spray passes leads to areas with double or triple layers of powder.
– **Solution**:
– Optimize the operator’s spraying pattern.
– Use even and consistent movements with appropriate overlap (25–50% is typical).
—
### **5. Workpiece Design and Faraday Cage Effect**
– **Cause**:
– Flat and wide surfaces attract more powder, while edges and corners may still struggle with coverage due to the Faraday Cage Effect.
– **Solution**:
– Adjust spray angles and settings to distribute the powder more evenly.
– Focus on recessed or complex areas to avoid uneven distribution.
—
### **6. Powder Reclaim System Malfunction**
– **Cause**:
– If the booth’s reclaim system is not properly calibrated, excess powder may accumulate on the workpiece instead of being captured.
– **Solution**:
– Inspect and maintain the reclaim system.
– Ensure the airflow and filtration system are working correctly to manage overspray.
—
### **7. Environmental Factors**
– **Cause**:
– High humidity can cause powder clumping and uneven deposition.
– Poor airflow in the spray booth may allow excess powder to settle on the workpiece.
– **Solution**:
– Keep the spraying environment’s humidity below 50%.
– Ensure proper ventilation and airflow in the booth.
—
### **8. Poor Equipment Calibration**
– **Cause**:
– The spray gun’s settings (e.g., air pressure, powder flow) are not optimized, resulting in excessive application.
– **Solution**:
– Calibrate the spray gun regularly.
– Adjust the air pressure to achieve efficient powder atomization without excess buildup.
—
### **9. Operator Error**
– **Cause**:
– Inexperienced operators may over-spray areas, causing uneven and excessive powder application.
– **Solution**:
– Train operators to follow standard spraying techniques and guidelines.
– Monitor application processes to ensure consistency.
—
### **10. Overspray Accumulation**
– **Cause**:
– Overspray powder can settle on the workpiece if the booth’s airflow and exhaust system are insufficient.
– **Solution**:
– Improve booth airflow and exhaust systems to manage overspray effectively.
– Use a powder recovery system to capture and recycle overspray.
—
### **Consequences of Excessive Powder**
– **Defects**: Uneven coating, drips, or sags after curing.
– **Wastage**: Increased material costs due to inefficiency.
– **Rework**: Time and resources needed to correct over-coated parts.
—
### **Summary**
To avoid excessive powder deposition:
– Optimize equipment settings (voltage, powder flow, and air pressure).
– Train operators on proper spraying techniques.
– Maintain environmental control in the spray booth.
– Regularly inspect and maintain all equipment.
Balancing these factors will ensure efficient powder usage and high-quality, uniform coatings.
electrostatic magic powder
electrostatic magic powder coating peterborough
electrostatic magic powder coating review
electrostatic magic powder coating system
electrostatic manual powder coating system cl 668 l3
electrostatic paint powder coating
electrostatic paint sprayer vs powder coating
electrostatic paint vs powder coat
electrostatic painting and powder coating
electrostatic painting and powder coating las vegas nv
electrostatic painting powder coating