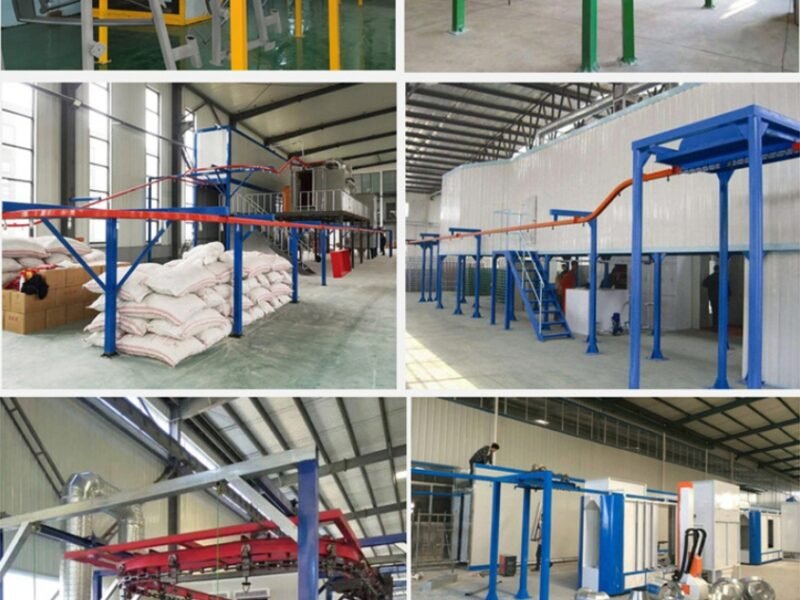
What should be paid attention to when maintaining and servicing epoxy powder electrostatic spraying equipment?
Maintaining and servicing **epoxy powder electrostatic spraying equipment** is crucial for ensuring consistent performance, prolonging equipment lifespan, and achieving high-quality coatings. Here’s a detailed guide on what to pay attention to:
### 1. **Regular Cleaning of the Equipment**
– **Powder Spray Gun**:
– Clean the **spray gun nozzle** regularly to prevent clogs and ensure an even spray pattern. Accumulated powder can cause inconsistent spraying or complete blockage.
– Disassemble and clean the internal components periodically to remove any built-up powder or debris.
– **Hopper and Feed System**:
– Empty and clean the **powder hopper** to avoid contamination between different colors or types of powders.
– Ensure the **feed lines** are free of blockages. Compressed air can be used to clear the lines, but ensure the air is dry to avoid moisture contamination.
– **Recovery System (Cyclone, Filters)**:
– Clean the **cyclone separator** and **filters** in the powder recovery system to maintain efficient powder recycling. A clogged filter can reduce suction efficiency and increase wastage.
– Replace filters regularly according to the manufacturer’s recommendations to maintain optimal airflow and filtration performance.
### 2. **Check and Maintain the Electrostatic System**
– **Electrostatic Generator**:
– Inspect the **electrostatic generator** for proper function. Ensure it generates the correct voltage required for optimal powder adhesion.
– Regularly check the **cables** and **connections** for wear, damage, or loose connections, as faulty wiring can disrupt the electrostatic field.
– **Grounding System**:
– Ensure proper grounding of the equipment and the substrate being coated. Poor grounding can result in inadequate powder adhesion and uneven coating.
– Regularly check the grounding rods and connections for corrosion or damage.
### 3. **Inspect the Powder Delivery System**
– **Pumps and Venturi Systems**:
– Check for wear and tear on **pumps**, **venturi tubes**, and other powder delivery components. Worn components can reduce powder flow consistency and efficiency.
– Replace worn parts as needed to maintain steady powder flow.
– **Compressed Air Supply**:
– Ensure the **compressed air** used in the system is clean and dry. Moisture or oil in the air supply can cause clumping of the powder and uneven application.
– Regularly check and maintain air dryers and filters to prevent contamination.
### 4. **Monitor the Curing Oven**
– **Temperature Control**:
– Regularly calibrate the **curing oven** to ensure it maintains the correct temperature for curing epoxy powder coatings. Inconsistent temperatures can lead to improper curing, affecting the finish and durability.
– Check for any hot or cold spots in the oven, which can cause uneven curing.
– **Oven Cleanliness**:
– Keep the oven clean and free from powder buildup, which can cause contamination and affect the quality of the finish.
### 5. **Maintenance of Booth and Workspace**
– **Spray Booth Cleaning**:
– Regularly clean the **spray booth walls**, floor, and work area to prevent overspray buildup and contamination. This also helps in maintaining a clean working environment.
– Use anti-static materials or coatings for the booth walls to prevent powder from sticking excessively.
– **Ventilation System**:
– Check the **ventilation system** for proper airflow. Good ventilation ensures a clean work environment and efficient removal of excess powder.
– Replace filters in the ventilation system as needed to maintain air quality and system efficiency.
### 6. **Calibration and Testing**
– **Equipment Calibration**:
– Periodically calibrate all equipment, including the spray gun, electrostatic generator, and curing oven, to ensure they operate within specified parameters.
– Use test panels to check the quality of the coating, including adhesion, coverage, and finish consistency.
– **Powder Flow Rate**:
– Monitor and adjust the **powder flow rate** to ensure even and efficient coating application. Too much or too little powder can affect the finish and increase waste.
### 7. **Safety Checks and Maintenance**
– **Personal Protective Equipment (PPE)**:
– Ensure operators use the appropriate PPE, including respirators, gloves, and safety goggles, to protect against powder inhalation and exposure.
– **Emergency Stop Systems**:
– Test and maintain **emergency stop buttons** and other safety systems to ensure they function properly in case of an emergency.
– **Fire Safety**:
– Regularly inspect fire extinguishers and fire suppression systems. Epoxy powder can be combustible under certain conditions, so maintaining fire safety systems is crucial.
### 8. **Software and Control Systems**
– **System Software Updates**:
– If your equipment includes digital controls or software, ensure it is regularly updated to the latest version to benefit from performance improvements and bug fixes.
– **Diagnostics and Error Logs**:
– Regularly review **diagnostic reports** and **error logs** from the system to identify any potential issues early.
### 9. **Training and Documentation**
– **Operator Training**:
– Regularly train staff on proper operation, maintenance procedures, and safety protocols to ensure consistent and safe use of the equipment.
– **Maintenance Logs**:
– Keep detailed logs of maintenance activities, including cleaning schedules, parts replacements, and calibration records. This helps in tracking equipment performance and planning preventive maintenance.
### 10. **Spare Parts and Consumables**
– **Stock Spare Parts**:
– Maintain an inventory of critical spare parts, such as nozzles, filters, and pumps, to minimize downtime in case of equipment failure.
– **Consumables Management**:
– Regularly check the levels of consumables, including powders, filters, and compressed air filters, and reorder as needed to ensure uninterrupted operation.
By following these maintenance and servicing guidelines, you can ensure your epoxy powder electrostatic spraying equipment operates efficiently, produces high-quality coatings, and has a long service life.
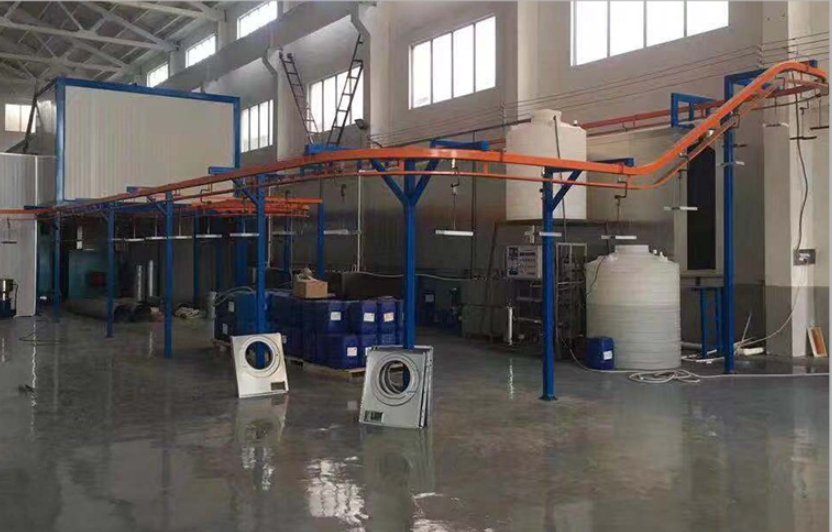
ectfe electrostatic powder
electrostatic adhesion powder
electrostatic charge powder
electrostatic coating powder
electrostatic coating vs powder coating
electrostatic dissipative powder coatings
electrostatic drum powder paint process
electrostatic dry powder coating
electrostatic enamel powder
electrostatic enamel powder coating
electrostatic fluidization bed for powder coating