
Why does electrostatic spray powder coating need particle size testing?
Why does electrostatic spray powder coating need particle size testing?
Electrostatic spray powder coating requires particle size testing because the size of the powder particles directly affects several critical aspects of the coating process and the final coating quality. Here are the key reasons why particle size testing is essential:
—
### **1. Influence on Powder Flowability**
– **Smooth Application:** The powder particles must flow consistently through the spray gun and reach the workpiece evenly. If the particles are too large or irregularly sized, they can clog the spray equipment or result in inconsistent powder flow, causing defects like orange peel, streaks, or voids in the coating.
– **Powder Recovery Efficiency:** Proper particle size ensures that the powder can be effectively captured and reused in recovery systems, reducing waste and improving cost efficiency.
—
### **2. Transfer Efficiency**
– **Adhesion and Coverage:** The electrostatic charge applied to the powder is more effective when the particle size is optimized. Smaller particles typically carry a better electrostatic charge and are more likely to adhere to the surface evenly, improving transfer efficiency and coating uniformity.
– **Faraday Cage Effect:** Larger particles can struggle to reach recessed or complex areas due to the Faraday cage effect (where powder is repelled by electrostatic forces in corners and crevices). Particle size testing ensures the right size distribution to minimize this effect and improve overall coating coverage.
—
### **3. Coating Thickness and Consistency**
– **Uniform Coating:** The size of the powder particles affects the final coating thickness. A mixture of particles that are too large can create uneven layers, while too many fine particles can lead to excessive buildup and thick spots.
– **Achieving the Right Film Thickness:** Particle size testing ensures the powder achieves a consistent thickness for both functional and aesthetic purposes, avoiding issues like too thin or excessively thick coatings.
—
### **4. Quality of the Final Finish**
– **Surface Texture:** Powder particles that are too large or too fine can cause defects in the surface texture. Large particles may create rough, uneven finishes, while small particles might lead to an overly smooth or glossy surface.
– **Gloss and Appearance:** The ideal particle size ensures a smooth, uniform surface, contributing to a consistent gloss and color depth. For high-gloss finishes, smaller, well-distributed particles are preferred to avoid imperfections.
—
### **5. Curing and Hardening**
– **Uniform Curing:** The particle size can affect the curing process. Larger particles may not melt and flow as easily, causing poor bonding or incomplete curing, which impacts the coating’s durability.
– **Optimal Flow:** Smaller particles tend to melt more easily, leading to a smoother and more uniform coating when cured, ensuring that the coating bonds properly to the substrate and provides adequate protection.
—
### **6. Powder Recovery and Waste Reduction**
– **Reusability:** Powders with an ideal particle size distribution are easier to reclaim in a powder recovery system. This allows for better reuse of powder, reducing overall waste and improving cost-efficiency.
– **Minimizing Waste:** By testing and optimizing particle size, manufacturers can reduce overspray and ensure that more of the powder is applied to the workpiece rather than lost during spraying.
—
### **7. Improved Process Control**
– **Consistency in Coating Application:** Regular particle size testing helps maintain consistency in the powder coating process, leading to better control over coating thickness, adhesion, and uniformity.
– **Quality Assurance:** By monitoring particle size distribution, manufacturers can ensure that each batch of powder meets the required specifications and performance standards.
—
### **8. Regulatory Compliance**
– **Environmental Standards:** Particle size testing ensures that the powder adheres to industry and environmental regulations, such as those related to air quality and VOC emissions, by ensuring consistent powder application and reducing excessive overspray.
– **Performance Standards:** Many industries require specific powder characteristics to meet performance criteria, such as durability, resistance to corrosion, or UV protection, which can be influenced by particle size.
—
### **Key Points in Particle Size Testing:**
– **Testing Equipment:** Tools like laser diffraction analyzers or sieve methods are used to measure the particle size distribution of powder coatings.
– **Ideal Range:** For electrostatic spraying, powders typically have a particle size range of 20 to 50 microns, though the exact range depends on the application and the type of powder.
—
In summary, particle size testing is essential to ensure the powder coating process is efficient, the final finish is of high quality, and the coating performance is optimal. Proper particle size distribution improves transfer efficiency, reduces defects, ensures consistency, and contributes to a longer-lasting, high-performance coating.
electrostatic paint sprayer rental
electrostatic paint spraying company
electrostatic spray coating company
electrostatic spray coating service
electrostatic spray drying
electrostatic sprayer backpack
ryobi electrostatic sprayer instructions
ryobi p2807btl one+ 18v cordless electrostatic 1 gal. sprayer
what’s an electrostatic sprayer
best disinfectant solution for electrostatic sprayer
best electrostatic sprayer
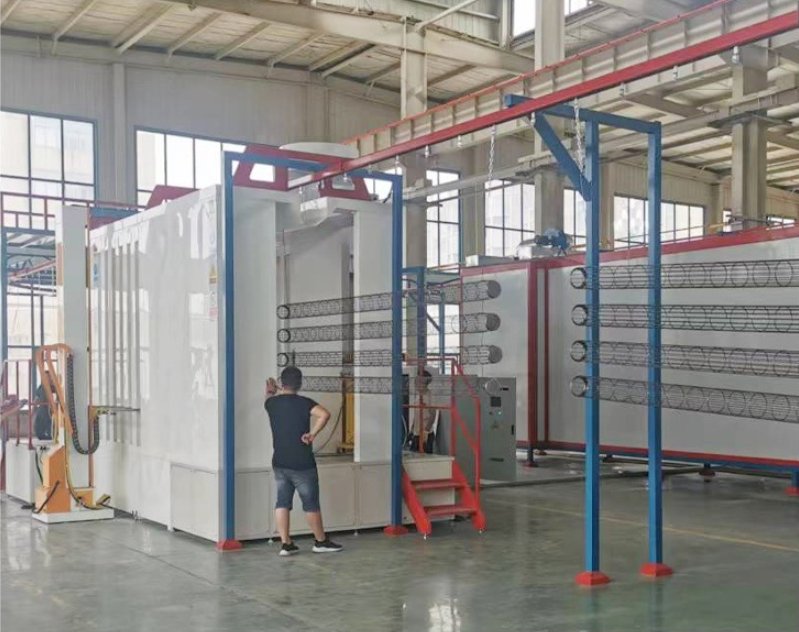