
Why is the recycling of paint electrostatic spray powder system so poor?
Why is the recycling of paint electrostatic spray powder system so poor?
The recycling of electrostatic spray powder in powder coating systems can sometimes be inefficient due to a variety of factors. While powder recovery systems are generally designed to collect oversprayed powder and reuse it, there are challenges that affect the efficiency of the recycling process. These factors include:
### **1. Powder Contamination**
– **Foreign Materials**: During the spraying process, the powder that falls into the recovery system may become contaminated with dust, dirt, oil, or other foreign materials. These contaminants can reduce the quality of the recycled powder, making it unsuitable for reuse in some cases. In some systems, operators may choose to discard the recycled powder if it is too contaminated to maintain the desired finish.
– **Degraded Powder**: The oversprayed powder that has been collected can sometimes undergo changes in particle size or consistency. Over time, recycled powder can degrade, making it less effective for coating, which results in the need to mix it with fresh powder to maintain coating quality.
### **2. Powder Loss During Recovery**
– **Inefficient Recovery Systems**: If the powder recovery system is poorly designed or maintained, not all of the oversprayed powder is captured. In some cases, a significant amount of powder may be lost to the air or outside the collection system due to improper airflow, ventilation issues, or malfunctioning filters.
– **Over-spraying and Overcompensating**: When powder oversprays and settles into areas outside the collection system (such as the booth’s corners), it can be difficult to recover, reducing the amount of powder that can be recycled. This leads to more material waste, as the recovery system isn’t capturing all of it.
### **3. Ineffective Powder Recovery Equipment**
– **Powder Recovery Technology**: Not all electrostatic powder spraying systems are equipped with advanced recovery technologies. Older or lower-quality recovery systems may not have the capacity to capture a high percentage of oversprayed powder, leading to lower recycling efficiency.
– **Filter Clogging**: The filters in powder recovery systems are essential for capturing fine powder particles. However, if the filters are not cleaned or replaced regularly, they can become clogged, reducing the effectiveness of the recovery system and causing powder to be wasted.
– **Powder Collection Hoppers**: The hoppers or bins that collect the oversprayed powder may not always be designed for easy powder flow, which can cause the powder to clump or settle in hard-to-reach areas. If the powder doesn’t flow properly, it may not be effectively transported back into the spray system for reuse.
### **4. Loss of Powder Through Airflow and Ventilation**
– **Inadequate Ventilation**: Improper airflow and ventilation in the spray booth can cause oversprayed powder to escape from the recovery system or get dispersed throughout the environment. This leads to a significant loss of powder, especially in large, open spaces or booths with poor air circulation.
– **Air Leakage**: Any gaps or seals that aren’t airtight in the recovery booth, ducts, or filters can allow oversprayed powder to escape, reducing recovery efficiency.
### **5. Physical Properties of Powder**
– **Powder Size and Shape**: Different types of powder may have varying particle sizes and shapes that affect how well they can be collected and reused. Fine powders or those with irregular shapes may be more challenging to capture efficiently than coarser powders. This can lead to more powder being lost or discarded.
– **Powder Clumping**: If the powder becomes damp or clumps together, it can be difficult for recovery systems to separate and collect it effectively. Humidity and temperature can influence the powder’s flowability, leading to inefficiencies in the recycling process.
### **6. Powder Overuse**
– **Excessive Powder Flow**: Sometimes, operators may use more powder than necessary to ensure an even coating. While the electrostatic process does help direct the powder to the workpiece, overapplying powder results in more overspray, reducing the amount available for recycling.
– **Inconsistent Powder Application**: Uneven or excessive application of powder can also contribute to inefficient use and recovery. If the spray guns or electrostatic generators are not properly calibrated or adjusted for the workpiece, excess powder may be sprayed without reaching the surface, causing additional waste.
### **7. Lack of Operator Training**
– **Improper Settings**: In some cases, the system’s settings may not be properly adjusted. For example, if the electrostatic charge is too high or too low, or if the spray gun is held too far from the workpiece, it can lead to poor powder adhesion and excessive overspray. This waste reduces the amount of powder that can be effectively recovered.
– **Inexperienced Operators**: Operators who are not familiar with the optimal settings for powder coating may inadvertently contribute to higher powder loss, inefficient recycling, and inconsistent coating results.
—
### **8. Quality Control Issues**
– **Inconsistent Recycled Powder Quality**: The recycled powder, especially if mixed with fresh powder, may not perform as well as the original batch in terms of adhesion, finish, or color. The quality can deteriorate over time if not monitored carefully, which leads to hesitance in using recycled powder and a preference for new powder.
—
### **Strategies to Improve Powder Recycling Efficiency**
– **Regular Maintenance of Recovery Systems**: Ensuring the filters, ducts, and recovery hoppers are cleaned and maintained frequently to prevent clogging and ensure efficient powder capture.
– **Upgrading to Better Recovery Technology**: Invest in high-efficiency powder recovery systems, such as **cyclone separators** and **high-performance filters**, that can capture more powder and reduce waste.
– **Proper Calibration**: Adjusting spray guns and electrostatic generators to optimize powder flow, reduce overspray, and improve transfer efficiency.
– **Training Operators**: Ensuring operators are properly trained to minimize overuse of powder and maintain correct settings to achieve the best powder application and recovery results.
– **Monitoring Powder Quality**: Regularly checking the quality of recycled powder and establishing a safe ratio for mixing recycled powder with new powder to maintain coating performance.
– **Control Environmental Factors**: Maintaining ideal humidity and temperature levels in the spray booth to prevent clumping of powder and to improve the flowability of recycled material.
—
By addressing these factors and improving the recovery and recycling systems, it’s possible to reduce waste and increase the efficiency of powder use in electrostatic powder coating applications. Would you like more details on specific recovery technologies or best practices for improving the recycling process?
electrostatic powder combustible dust k value
electrostatic powder cooating system
electrostatic powder fluid bed for powder coating hopper
electrostatic powder inc
electrostatic powder k values
electrostatic powder line
electrostatic powder paint suppliers
electrostatic powder painting equipment company
electrostatic powder painting equipment manufacturer
electrostatic powder painting equipment products
electrostatic powder painting equipment supplier
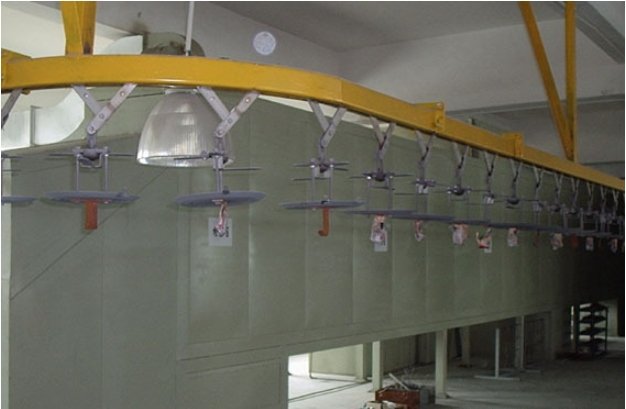